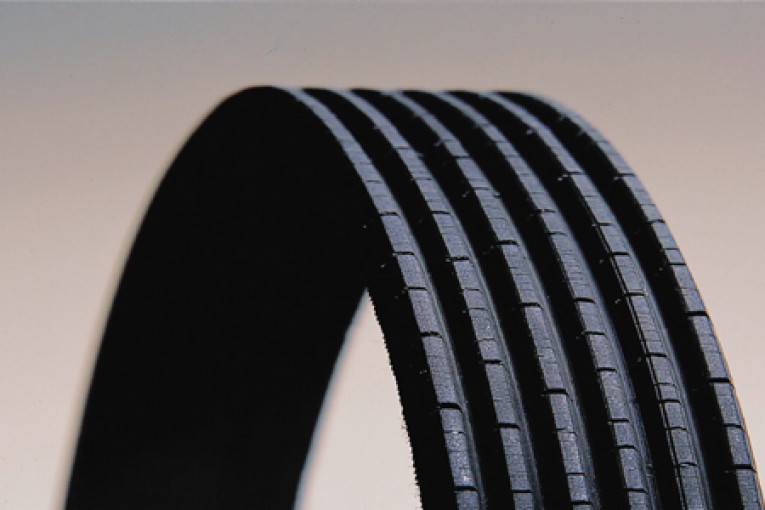
At the Gates workshop seminar that took place during May’s MECHANEX outing in Manchester, several garage mechanics from the North West of England were concerned about the same technical issue.
The query in question was that as it is no longer possible to assess the wear to a multi-ribbed belt installed on a modern Auxiliary Belt Drive System (ABDS), how is wear to be identified and what are the implications for belt wear replacement intervals?
The short answer to this question is that manufacturer recommendations for replacement remain unchanged, while testing the ABDS belt has become a very simple and more precise process to undertake.
Firstly, it’s important to explain the reason for the change and why the obvious signs of an ageing belt are no longer there.
Technical answer
In the days when belts were made using a compound including Neoprene or Chloroprene, a simple visual check could establish that the belt was old and its performance was in decline. Typically, these belts were designed with a life expectancy of around 50 – 60,000 miles, and the signs of wear that began to emerge were obvious to the experienced eye (Fig 1 below).
(Fig 1)
A basic visual check used to involve looking for the classic signs of wear, such as:
- Cracks in the belt
- Chunks of material missing
- Rib separation
These signs are no longer seen in modern ABDS belts (Fig 2 below) which – like the distinctive Micro-V Horizon solution from Gates – are all produced with a compound made from EPDM (Ethylene Propylene Diene Monomer). This material just wears away, making detection less obvious.
(Fig 2)
However, these belts offer major benefits: increased levels of durability and greater resistance to extremes of temperature are major reasons for the switch to EPDM, while it is also more resistant to contamination by oil and less likely to experience fatigue.
Compact age
Increased levels of resistance are more significant given the emergence of compact engines that are smaller, lighter and much more powerful than the previous generation of engines. They generate temperatures that are much higher than their less powerful predecessors. Although multi-ribbed belts used to cool down between the pulleys, the shorter span lengths inside today’s smaller engines limit opportunities for cooling.
Solutions, such as the Micro-V Horizon belt from Gates, were subsequently introduced as a response to these more hostile conditions.
Testing time
With few visible signs of wear, detecting its presence in the ABDS on a belt made from EPDM has had to become more precise. The solution to this is simple (Fig 3 below).
(Fig 3)
Available for free from motor factors, the Wear Indicator Tool makes it possible to determine the degree of wear – with some accuracy – while the belt is still fitted to the vehicle. Moreover, both belt and pulleys can be tested and this can be done each and every time the vehicle enters the workshop.
Pulley checks
The “narrow side” tooth profile must fit perfectly into the grooves of the pulley and no side-to-side movement must be possible. If side-to-side movement is achieved then the garage can determine that a) excessive plastic/metal has been worn away or b) pulley-ribs may be rounded instead of straight.
Either way, the belt is not transmitting the optimum level of power. A new belt running on a pulley that hasn’t been replaced will have less than optimal grip and its power transmission capabilities will be compromised.
Belt checks
The “broad side” tooth profile of the indicator must fit perfectly within the ribs of the belt. No side-to-side movement must be possible without lifting the tool out of the belt grooves. If movement is detected then a) excessive material has been worn away from the belt or b) the belt is not transmitting the optimum level of power.
Change intervals
As there are no recommended change intervals for the ABDS, installers no longer have to rely on a ‘best estimate’, based on visual wear checks. Wear to the belt and the pulley is now measurable and this is a good thing because the consequences of drive system failure could, in the worst case scenario, be catastrophic.