Andrew Vaux, Technical Support & Training Specialist at Gates talks us through the most common reasons for water pump problems.
Following recent analysis of our inspection data we’ve been able to identify the most common causes of premature water pump failure in passenger cars throughout Europe. Interestingly, the most frequently recurring issues are as a result of installer error, mainly due to:
■ Dry rotation/testing for free movement of water pump assemblies before installation;
■ Use of inappropriate seals/gaskets or sealant;
■ Incompatible/contaminated coolant;
■ Installation of worn/defective parts.
Although these are major causes, they’re not listed in order of importance and all are regularly repeated somewhere in one of our European markets on a daily basis. They all, however, can be avoided through training, access to good technical information, following the correct procedures and using the appropriate tools.
Understanding what makes water pumps fail is the key to longer operational life of the drive system and its individual components and that’s why Gates gathers so much inspection data.
It’s important to understand that the average water pump has a throughput of around 1.7 million litres of coolant over a four year (100,000 kms/60,000 miles) duty cycle. Routine replacement of the water
pump without investigating the cause of failure could condemn the new replacement to an even shorter life.
Fewer remedial repairs, more workshop efficiency and increased levels of customer satisfaction must be the goals of every workshop manager, so access to reliable technical information is essential.
The GatesTechZone
(www.GatesTechZone.com) is an important resource for any drive system specialist. It includes product support, technical tips, details about tools, installation and diagnostic procedures, as well as access to the Gates online catalogue. It also identifies the most common causes of failure and explains how errors can be avoided.
DRY ROTATION/TESTING THE WATER PUMP
As well as helping to keep the engine cool, the coolant plays an important role in maintaining an efficient seal inside the water pump. Constant lubrication of internal seals is essential.
Never dry rotate/test for free movement of a water pump assembly before install
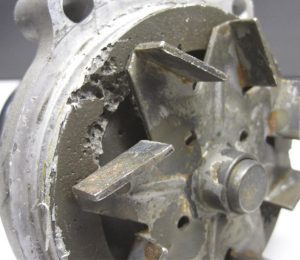
ation – even for a few seconds. Dry rotation can permanently damage the internal seals and that will cause a leak. After the system has been refilled with coolant, you should rotate the drive pulley by hand a few times. This will allow a small amount of coolant to lubricate the mechanical seal before the engine is started.
Tip: To test for free movement of the water pump assembly before installation, fill a reservoir full of coolant and immerse the water pump. A test for free movement can now be made without fear of compromising the integrity of the water pump!
USE OF INAPPROPRIATE SEALS/GASKETS
Old gaskets and seals must be replaced. If the water pump has a gasket or seal, never apply sealant as this will cause component failure. Use sealant only when specified by the manufacturer. Improper use can cause problems with water pump seating or the seal can be compromised.
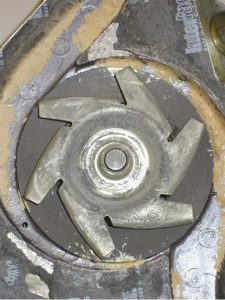
If Sealant is recommended, put an even bead along the edge and around the coolant passages (installation holes) on the impeller-side of the pump. Too much sealant will compromise the installation because it breaks off and contaminates the coolant.
Tip: Different sealants have different drying rates. Always respect the instructions of both the sealant manufacturer and the water pump manufacturer.
UNSUITABLE/CONTAMINATED COOLANT
Use of unspecified or contaminated coolants leads to premature failure of the water pump. An unspecified, incompatible or mixture of different coolants usually leads to insufficient protection against rust or corrosion.
Contamination commonly occurs in systems that haven’t been properly maintained.Abrasive particles circulate through the system, scratching and damaging the seals and internal surfaces, destroying the individual component and creating the pathways that allow leaks to develop.Before installing a new water pump, drain and flush the entire cooling system with appropriate equipment.
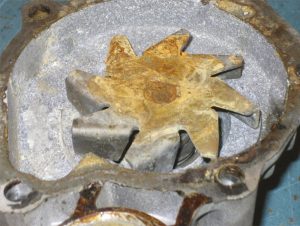
Tip: Modern cooling systems are complex, contain a range of different materials and rely on specific coolant formulations for protection from rust and corrosion. This is the key reason for the growth of manufacturer-approved coolants. Always use the recommended specification.
INSTALLATION OF WORN/DEFECTIVE PARTS
A worn belt fitted with a new water pump, or a new belt fitted with an old water pump, is a recipe for premature drive system failure. Gates recommends a complete drive system overhaul – replacing the belt and the tensioner(s) at the same time as the water pump – by means of an all-in-one kit. This minimises risk of drive system failure and optimises the lifetime of the individual components.
Tip: Follow the recommended water pump installation procedure and the kit manufacturer’s recommendations with respect to belt tensioning and torque setting.
AND FINALLY…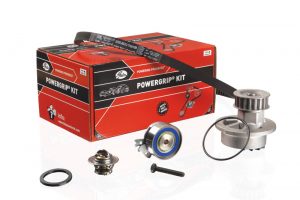
Seepage from the weep hole in a newly installed water pump is normal during the initial ‘break-in’ period – there is no cause for concern. Once the mechanical seal has seated itself, the seepage will stop. Prolonged seepage or a large coolant bleed mark around the weep hole is abnormal and indicates impending water pump failure.
By performing a drive system overhaul and following the manufacturer’s fitting instructions every time, installers can ensure a further 100,000 km/60,000 miles of drive system reliability.