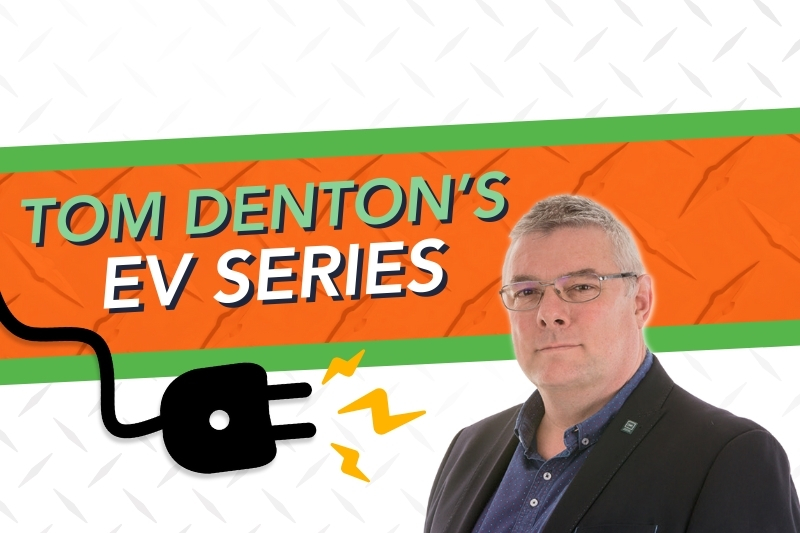
Equipotential bonding (EPB) is the process of electrically connecting metalwork and conductive parts, so that the voltage is the same throughout these various parts (an equal potential).
EPB is used to reduce the risk of equipment damage and personal injury. It is sometimes simply referred to as bonding and is commonplace in domestic and industrial electrical installations. Its main purpose is safety.
In the near future, all workshops and garages will have to deal with a significant number of high voltage electric vehicles. Checking the safety and reliability of vehicle high-voltage systems is something we will need to become more familiar with.
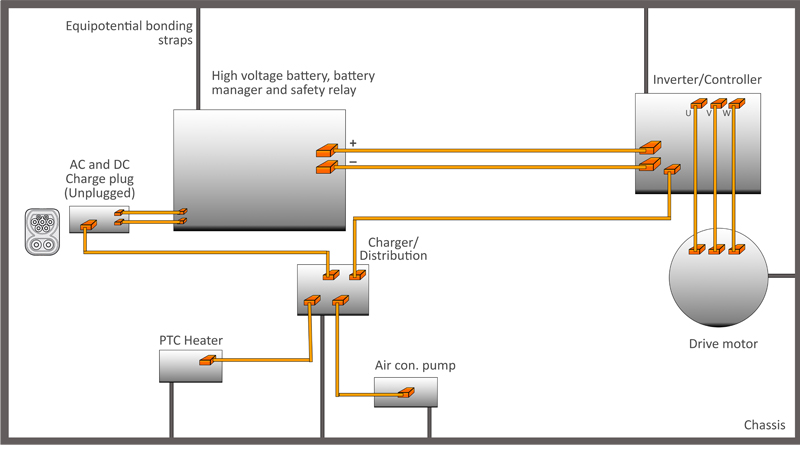
EVs use an insulated return system so that there is no connection between the high-voltage circuits and the chassis. As part of the start-up process (when the vehicle is switched into ‘Ready’ mode) the on-board insulation monitor device runs a number of tests.
If a failure of this ‘monitor’ is detected, then the vehicle will not switch on. However, if an insulation fault occurs on a HV component that is not properly bonded, the insulation monitor will not find and monitor this hazardous issue.
The reason that all the components are bonded to the chassis is so that even if insulation faults occur, the potential (voltage) difference between all the main metal components will always be zero – so no electric shock will occur. In theory, this should never happen so the bonding is like a belt and braces approach – better safe than sorry though because the high voltages used can be fatal.
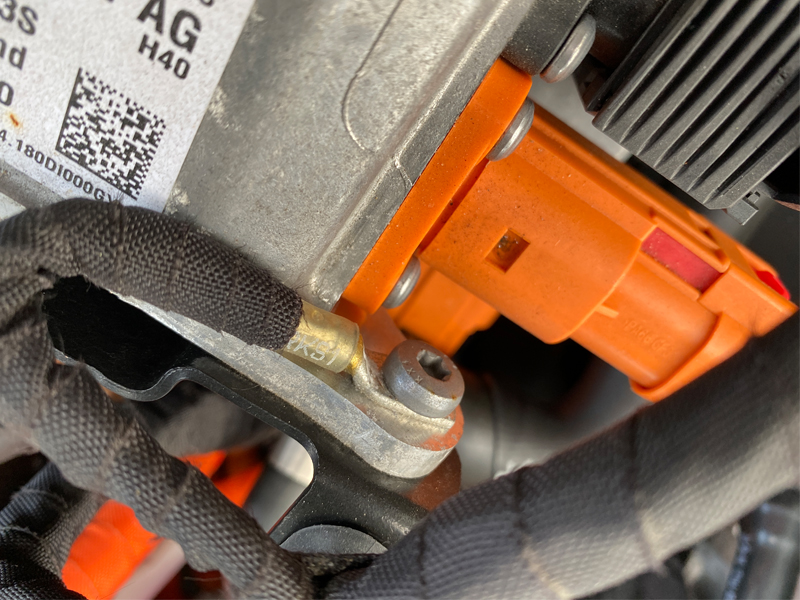
When repairs are carried out the insulation resistance or isolation strength of high-voltage system components is always tested by the technician. The continuity of cables, including the braided shielding is also checked. A value of 500 V is often used for an insulation test but for some systems it is becoming necessary to use 1,000 V. Isolation strength (insulation resistance) of some components can deteriorate over time.
A key part of UN regulation ECE R100 states the specified equipotential bonding between two HV components shall be less than 100mΩ (a tenth of an ohm). To measure milliohms (mΩ), special equipment is needed, a normal multimeter is not suitable.
EPB is used to reduce the risk of equipment damage and personal injury from high voltages. Checking EPD can be more involved than it may first appear. However, with the proper equipment, suitable training and time, it is very easy. To date, here in the UK anyway, the equipotential bonding resistance between the components and chassis, has not been carried out as a matter of course – other than as a physical ‘hand and eye’ check.
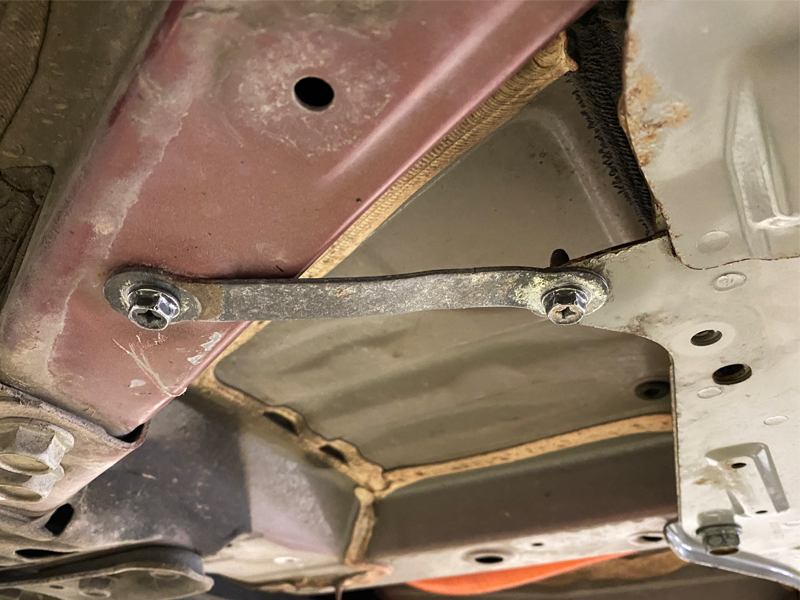
For some organisations, these sort of measurements and records are becoming more important. For individual technicians it is also becoming important to prove all tests have been carried out and so prevent future litigation.
In the next article Tom will highlight one method of testing EPB and how in the future it could become an income stream for your workshop.