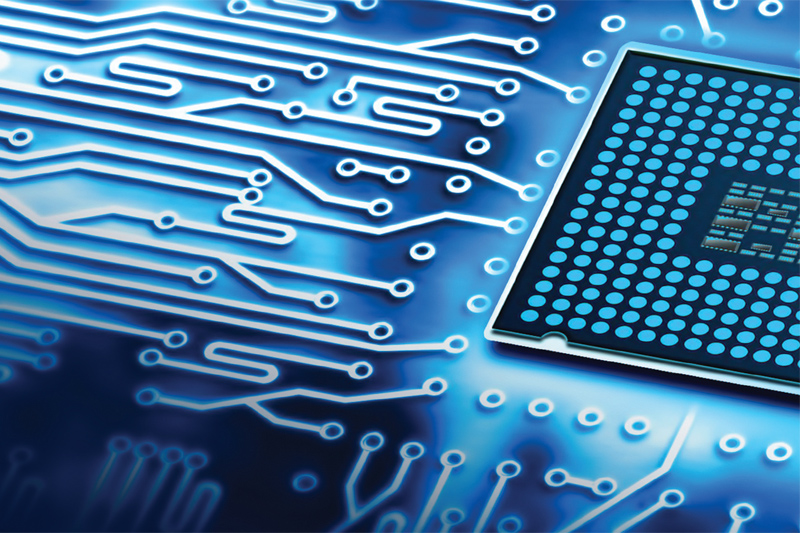
In the connected world we live in, developments and disruptions in unrelated sectors can end up impacting on the automotive industry. Neil Pattemore reflects on the recent semiconductor shortage and the increasing restrictions on independent workshops replacing OEM parts in the name of ‘cybersecurity’. Will the independent aftermarket end up at a disadvantage?
Many years ago, when I was a teenager, the village I lived in was on a main road and boasted a ‘proper transport café’. How did I know that this was a proper transport café? It always had a lot of lorries in the car park, the drivers feasted on the fry-ups and the menu offered ‘chips with everything’.
Times have moved on and the transport cafe has long since been demolished, but the ‘chips with everything’ (‘chips’ now referring to microchips or semiconductor integrated circuits) has now become the basis for almost all functions found on today’s vehicles. The current shortage in these chips has become a problem for the automotive industry, and for the aftermarket things will only get worse before they get better, but then could become an even more serious problem.
So, what exactly is happening to these chips?
The current shortage is a combination of several factors that have coalesced to create a perfect storm. Firstly, the start can be traced back to coronavirus. Like most manufacturing sectors, the semiconductor sector had to partially shut down because of the pandemic, resulting in a reduced supply of chips.
Secondly, the pandemic led to many employees working from home and this has significantly increased the demand for PCs and printers for home use. Thirdly, there was the launch of two new gaming consoles – the PlayStation 5 and Xbox Series S/X – pushing demand for chips to a new high – Sony estimates it alone sold 4.5 million units in 2020. To add to these factors, there was a fire at the Renesas Electronics factory – one of the largest semi-conductor suppliers to the automotive industry. The unhelpful backdrop to all of this has been the USChina trade war.
For the vehicle manufacturers, this came on the back of a massive downturn in demand for new vehicles (and the corresponding in-vehicle systems and components) created by the pandemic, which in turn was followed by a massive upturn in demand as the economies around the world started to recover. However, semiconductor manufacturing did not have the capacity to simply fulfil this increased demand from the automotive system suppliers.
Vehicle manufacturers have universally indicated that their production volumes will fall and profits in Q2 and Q3 of this year will be significantly down. With the decreased availability of new vehicles, the price of used vehicles has risen significantly.
How will this chip shortage impact the aftermarket?
There will be a number of both short and longer term issues arising from this chip shortage.
The most obvious is the reduced volumes of new car sales, which helps the aftermarket in the shorter term, but will become a longer term issue. However, much more critical as an immediate impact is the availability of replacement parts which use chips, as these are often ‘captive parts’ which are only available from the vehicle manufacturer. Where there is some availability, this is likely to be prioritised in favour of the vehicle manufacturer’s own dealer network and not independent repairers.
Equally, independent parts manufacturers that use chips in their own parts, may also find that those chips that are available are prioritised for the Tier One suppliers as part of the vehicle manufacturer supplier contracts.
In a separate, but parallel, issue to the chip shortage, the vehicle manufacturers are increasingly programming the replacement parts that are supplied, so that a code is required to allow the part to be activated (these can now be mechanical parts, as well as those that include chips). Often this code is only made available to main dealers, or can only be conducted using the vehicle manufacturer’s own diagnostic tool. Independent repairers can find themselves, and increasingly do, refused on the basis of ‘safety and cybersecurity’.
Of particular significance are replacement parts that are fitted as part of an ADAS. Currently, many of these parts are electronic and are coded by the vehicle manufacturer, but for independent parts manufacturers to develop these parts now involves another significant barrier. There is new vehicle type approval legislation that has been developed at the UNECE in Geneva which creates the requirement for ‘cybersecurity’ to become part of the vehicle type approval. However, whereas all other vehicle type approval requirements are technically defined (e.g. steering, brakes, emissions), the cybersecurity is individually developed by each vehicle manufacturer and is then assessed by the type approval authority. This means that the vehicle manufacturer decides who can access the vehicle and for what purpose. To develop a replacement part, an independent parts manufacturer would need to agree a ‘project’ with the vehicle manufacturer and follow the cybersecurity strategy of that individual vehicle manufacturer. This creates a significant range of issues – the vehicle manufacturer is under no obligation to agree to the independent parts manufacturer’s request, the costs involved, extending into full disclosure through the independent parts manufacturer’s supply chain for the ‘safety and security’ requirements of the vehicle manufacturer. A true ‘big brother’ scenario!
So, although the current chip shortage will create some problems in repairing a vehicle, these chips form the basis of much more significant problems for the aftermarket, which are already starting with new vehicle type approvals.