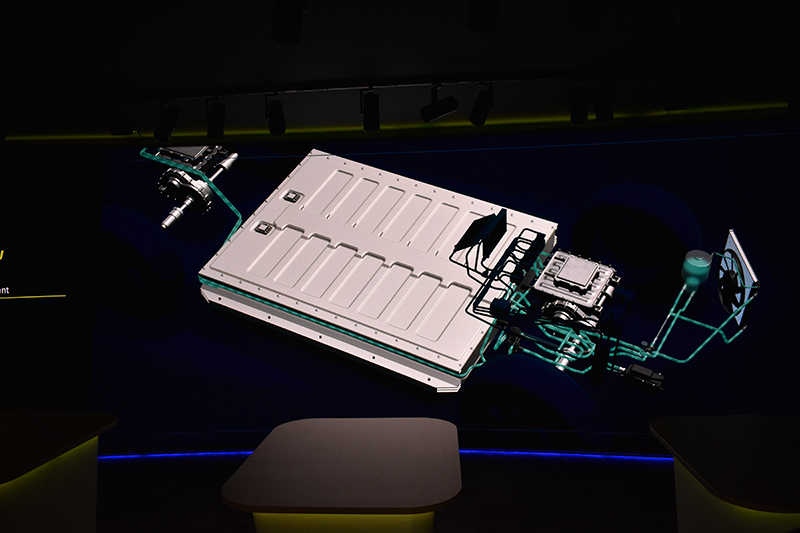
PMM ’s Kieran Nee made the journey to picturesque Rastatt to visit TI Fluid Systems, makers of all fluid-related transport systems within cars, to see inside its new e-mobility ‘Innovation Centre’.
Electricity and fluids might not be the easiest of bedfellows, yet in electric vehicles the two are inseparable. Humble coolant, already the silent stalwart of the ICE vehicle, plays a positively crucial role in the EV. As we all know, battery-powered vehicles run the risk of overheating (are almost destined to overheat, set ablaze and lead to the rapid decline of civilisation, if some in the aftermarket are to be believed), so thermal management is integral to regulating temperatures.
Whilst readers of PMM may not come into direct contact with TI Fluid Systems’ product solutions, it is still important to understand a bit about what is happening on the OE side of things, in order to be better prepared when EVs inevitably end up in independent workshops.
Let’s begin with a question I posed to TI’s CEO Hans Dieltjens: why open an e- mobility centre now?
“Electrification is being driven by efficiency – but the second element is timing. As you know, the European Union has decided that by 2035, no more combustion engine cars will be sold. So, this means that the development needs to start pretty early in order to ensure we’ll reach that point. We looked over our product range and we thought of how best to handle that.
“The first thing that came to mind to us was that we need to build in efficiency from the first step we take. That’s why we concentrated in this facility first on the simulation and our simulation ability to a greater extent than what that was available.
“We have 2D, 3D simulation options to ensure that we have the most efficient flow temperature at every spot in the car that is necessary. So that was the first part of the investment. The second part was that, well, if we know we have the most thorough theoretical framework in place, let’s see if we can quickly prove our components in a physical space.
“That’s why we built here, manufacturing these components directly here and prototype constructs in order to do that. Finally, with quick testing and real life testing potential to have it all together and in the same facility: direct feedback from your testing. Now, our engineers can talk to the simulation. So that made us think, hey, this offers the opportunity for efficiency, but the centre also offers the opportunity to lower the cycle time of a development quite significantly and get to market earlier with each product. This is how we can deliver up to 15 per cent efficiency improvements. Up to 30 per cent of cost improvements and another 20 to 30 per cent in weight savings.”
So, bringing it all into one place makes everything quicker and easier – makes sense to me. This was something echoed by chief technology officer, Johannes Helmich:
“From a hundred years of experience in fluid, the Mobility Innovation Center was developed with a clear goal in mind to be a collaborative space for our teams to design, visualise, prototype and test the next generation of thermal management systems, modules, and components for electric vehicles.”
Rigorous process
Each new product launched by the manufacturer starts off life with a need from the vehicle manufacturer. Greater efficiency, lighter products that take up less space – these are the attributes that OEMs come to TI Fluid Systems to provide in their fluid transporting solutions. Before manufacture, each item goes through a range of processes, which the team took us through in great detail:
Virtual engineering: a vehicle’s thermal management system is mapped out digitally, including CGI graphics of the interior, showing how the driver will ultimately engage in the process.
Designing: products are designed using CAD drawings to very strict tolerances, with virtual testing already built into the process. This means that products are as “good to go” as possible before even reaching the prototype stage.
Processing & Prototyping: prototypes are made using 3D printing and brought as close to perfection as possible before progressing to manufacture.
Testing: all products are extensively tested before being launched, including vibration, shock and endurance testing.