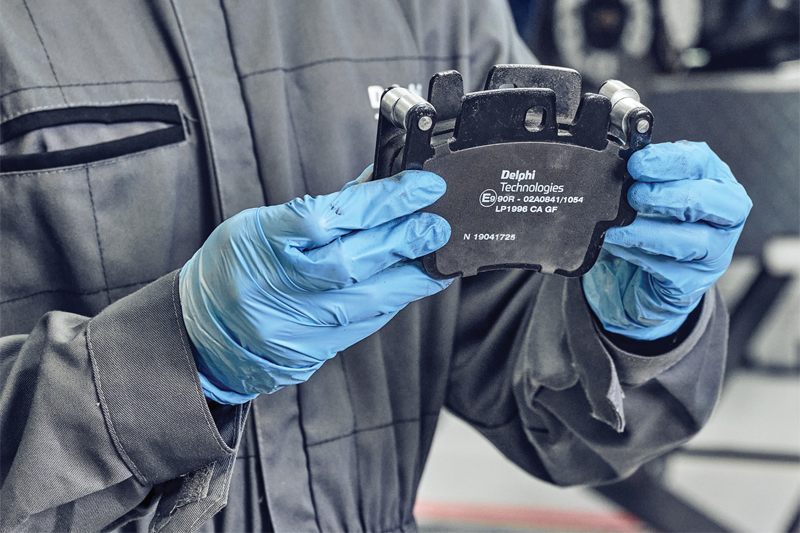
PMM hears from the technical team at Delphi Technologies on how braking components once charged with bringing a vehicle to a stop, now also have a hand in driving it forward.
Vehicles are changing. The technologies packed within them are becoming more powerful and established drivetrain characteristics are being turned on their heads.
What do we mean? Well, the brake system – once the preserve of making a car slow down – is no longer tasked with simply stopping a vehicle, but making it go, too.
Of course, we’re talking about regenerative braking. Sales of electric (EV) and hybrid electric vehicles (HEV) are increasing: latest SMMT figures show that electric and hybrid vehicles now account for 10.5% of all new registrations. Over half-a-million vehicles powered by an electrified powertrain are now on UK roads and, as the 2035 government ban on new sales of internal combustion engine powered vehicles draws closer, they will continue to be more commonplace.
The driver of this change is the fight to reduce emissions and enhance efficiency. Regenerative braking is a perfect example of improvements made in this area, and of technology challenging conventional wisdom. So, it sounds like a riddle best saved for post-Christmas pudding, but how do brakes help us both stop and go?
One step back, two steps forward
Using the principle that energy cannot be created or destroyed, just transferred or converted, a simple brake pad, disc and caliper set-up converts the kinetic energy generated through vehicles’ movement, via friction, into heat. This heat is dissipated into the environment, hence the continued evolution of methods and materials that aid efficient brake system cooling. However, a vehicle equipped with regenerative braking instead turns this ‘waste’ energy into electrical energy, which is used to boost the vehicle’s high voltage battery. This energy remains stored until it is required to provide power to the electric motors.
“Regenerative braking helps create a kind of circle of life for kinetic energy,” explained Julian Goulding, Northern Europe Marketing Manager at Delphi Technologies Aftermarket. “An electric motor obviously draws power from the vehicle’s onboard battery when providing motive power, but when the driver applies the brakes the process is effectively reversed. The kinetic energy that had been used to turn the wheels and make the vehicle move, now makes the motor turn – instead of using electrical energy, it acts as a generator and is creating it, which is then stored in the battery.”
The action described also helps to slow the vehicle, which poses different challenges for the traditional aspects of the brake system.
Working in tandem with conventional braking
Most EVs and HEVs can provide sufficient braking power through the electric motor to slow a vehicle in most driving scenarios.
“The stopping power of the electric drivetrain is very much condition-dependent, which is why the hydraulic system remains so crucial and it is vital that it is kept in good, fully operational condition,” continued Julian.
“For example, from high motorway speeds, very low speeds, when stationary, if the battery is fully charged, or too hot or cold, then the electric motor on its own cannot provide sufficient braking power and calls on the support of the hydraulic system.
“Exactly when and how often the hydraulic system is required is entirely vehicle dependent,” he explained. “For example, an early Toyota Prius from 2001-2004 never uses its hydraulic brakes unless below 7mph or under near-emergency braking situations.”
The relegation of the hydraulic system to the role of backup completely alters their operating conditions and wear patterns. “Irregular use means that rust and other contaminants can build up much faster than on a traditionally-braked vehicle,” remarked Julian. “This can impact the discs’ friction surfaces, pad mounting and even caliper pistons. Delphi Technologies has carried out extensive R&D during the development of OEquality EV-specific brake friction materials and found a wide range of wear characteristics.”
For example, the caliper carrier can suffer from accelerated corrosion due to lack of use. This can result in brake pads not fully retracting, causing accelerated wear and a huge reduction in vehicle efficiency. Brake drag can have serious negative connotations for an EV or HEV, including reduced range.
Pad to disc contact may also be compromised, resulting in a build-up of disc contaminants and eventual pitting. “The brake system is a vital part of any vehicle, not only from the perspective of efficiency but, far more importantly, safety,” concluded Julian. “Road dirt, salt and extreme temperature changes are all factors that can impact brake operation whatever the vehicle, regardless of what’s under the bonnet, so it remains just as crucial to view the entire system as a whole without simply focusing on what separates the technologically advanced and traditional.”