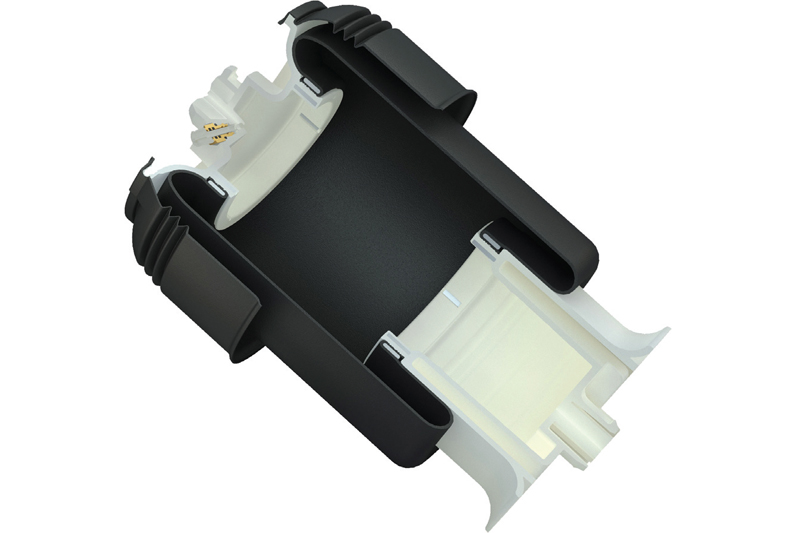
Air suspension specialist, Arnott Europe, provides readers with insight into the humble air spring and its constituent parts.
The working principle
An air spring consists of a compartment that is filled with pressurised air and a rolling piston that is connected to the axle of the vehicle or integrated on the suspension strut.
The rubber sleeve is safely secured between the two components with high-grade steel crimping rings for durable, air-tight construction. Together they form the ‘active area’ for the pressurised air. The ECU (Electronic Control Unit) uses several inputs (e.g. height sensors, vehicle speed, acceleration sensor) to calculate whether the air spring should inflate or deflate air to obtain the predetermined ride height.
Elastomer construction
Although an air spring is a wear and tear part, it can cope with high and low temperatures and has a high resistance to the constant abrasion of dirt and road debris. Arnott uses elastomer from respectable OEM manufacturers, such as Continental ContiTech, Vibracoustic and Goodyear. The sleeve construction is made with high quality elastomer material and consists of a five-layer, multi-ply design to provide a long-lasting structural integrity (see below):
- Outer elastomeric layer
- Cord layer
- Intermediate elastomeric layer
- Cord layer
- Inner elastomeric layer
Air spring characteristics
A conventional coil spring has a linear spring rate. This means that the same compression force is needed to compress it during the complete stroke. It can be tuned to progressive behaviour by changing the distance between the turns and/or varying in the thickness of the steel.
An air spring behaves differently. The force that is required to compress an air spring increases exponentially through the stroke. This means more force is needed to compress the air spring near the end of the stroke resulting in an overall comfortable driving experience.
The spring behaviour can be adapted to a more comfortable or sportier ride by changing the angle of the rolling piston. This is one of the reasons that a passenger car’s sport (air) suspension system usually features a different air spring than the standard (air) suspension for the same model.
The advantages
Air spring systems automatically level the vehicle, so the spring travel stays identical. This is very convenient when heavy cargo is transported in the boot. By comparison, a coil spring system is less comfortable, can be unstable and is more likely to ‘bottom out’ on rough roads or uneven surfaces (e.g. potholes).
By reducing the air inside the air spring, the ride height lowers at high speeds. This brings the vehicle closer to the ground decreasing the drag coefficient and thus reducing fuel consumption.
An inherent benefit of an air spring is that it naturally isolates the passengers from road harshness, resulting in a smooth and comfortable ride. Most car owners describe this as the biggest advantage of driving a vehicle with (factory) air suspension.
Look for quality
Although some cheap aftermarket air springs might look identical to the original part at first sight, the differences can be quite substantial! Making concessions such as using inferior rubber, lower grade parts, and/or consolidation in piston design can result in lower burst pressure, difficult fitment, impaired damping comfort and more NVH (noise, vibration, and harshness).