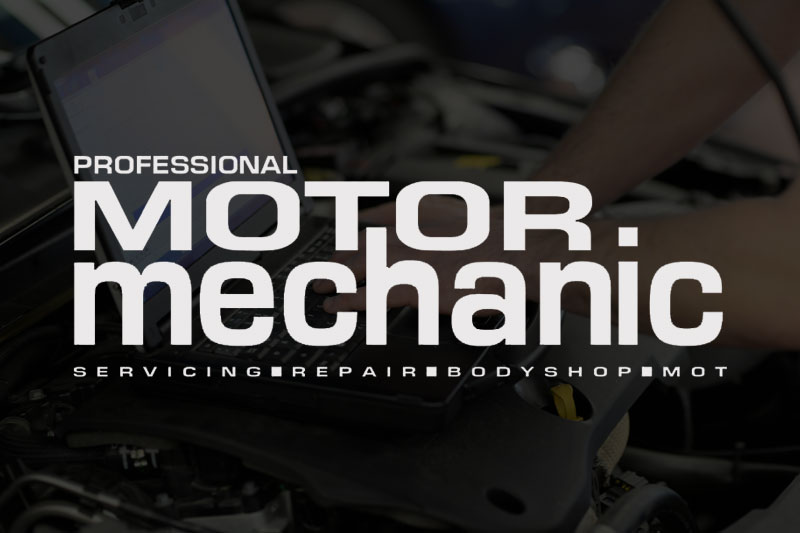
There are basically three different, non-interchangeable types of Lambda sensor. The zirconium dioxide and titanium dioxide Lambda sensors are also called switching, voltage jump or ‘binary’ sensors, because their output signal varies back and forth between two values, depending on whether the fuelling is in a rich or lean state. The third type is the broadband Lambda sensor.
Method of operation of the zirconium dioxide sensor
This sensor element has a hollow, thimble shaped design. The inside surface is in contact with ambient air. The outside surface is situated such that it lies in the stream of the exhaust gas. Both surfaces are covered with a thin, porous platinum layer which acts as electrodes.
There will always be a difference in the concentration of oxygen between the exhaust gas and ambient air. When the Lambda sensor reaches operating temperature, oxygen ions start to move through the ceramic electrolyte from the side that has a greater concentration of oxygen towards the side that has a lower oxygen concentration, attempting to reach a state of equilibrium.
As these ions leave one platinum layer and reach the other layer, a potential differential results, giving rise to an electrical voltage. If the mixture is lean, the voltage will be relatively low (approx. 0.1 volts). If the mixture is rich, it will be relatively high (approx 0.9 volts). There is a large characteristic voltage jump as the stoichiometric point (Lambda = 1.0) is passed.
Testing zirconia switching Lambda sensors
Testing with an oscilloscope is the most effective method. It shows minimum and maximum voltage, the response time and the frequency. When performing the test, the manufacturer’s specifications must be observed.
Test procedure
1. Bring the engine to operating temperature at 2,000 rev/min.
2. Connect the oscilloscope to a signal line without disconnecting the sensor from the engine control unit.
3. Set the measurement range to 1-5 volts and time to 5-10 seconds (observe manufacturer’s specifications).
4. If applicable, activate automatic signal recognition. A correctly functioning sensor swings between 0.1 and 0.9 volts with a frequency of 0.5-4 Hz.
Diagnosis tips
A visual inspection often provides the initial clues for a possible malfunction. Inspection points for the workshop are:
Resistance value of the heating element
If it is above 30 ohms then the sensor is defective.
Cables
Are they broken or is the plug broken? Is the cable seal intact? Has moisture penetrated into the plug? Are the plug contacts in good condition? Is the cable routing too tight?
Sensor body
Does the sensor show any visible damage?
Make sure you use the right sensor type
Each vehicle will have a specifically designed sensor type and therefore it is essential that they are only replaced with matching specification sensors. You can use the current NGK/NTK catalogues to identify the correct replacement sensor for each application.