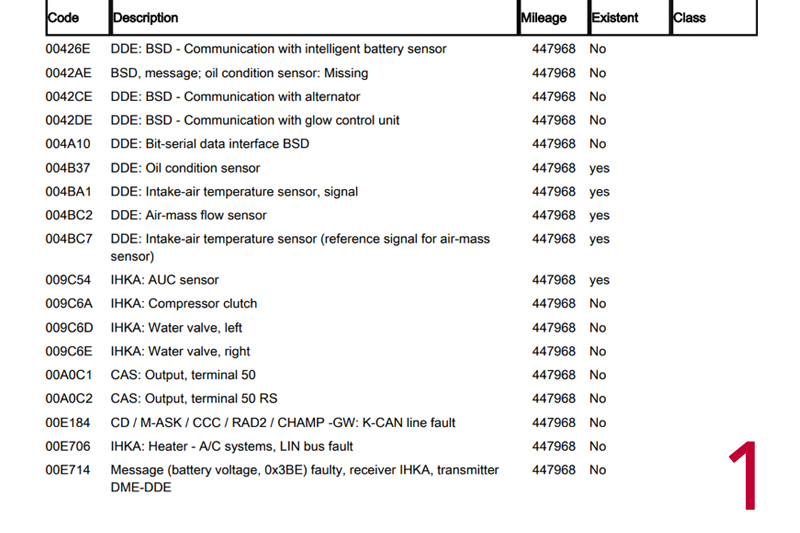
Ben Johnson investigates an (extremely) high mileage vehicle which left its driver stranded after losing power and discovers that faults, like good things, come in threes…
It has been quite a while since I’ve come across a car riddled with so many quirks that it turned me into more of a police detective than a mere fault finder. But let me tell you, last week, a nice looking E61 in M-sport trim rolled in on a flatbed truck, flaunting its seemingly flawless exterior and boasting an impressive set of wheels. Little did I know, this fine-looking car was about to take me on a wild ride.
The unhappy owner claimed that his prized possession had abruptly lost its power, leaving him stranded on the side of the road. Intrigued, I decided to dig deeper into the mystery lurking beneath the hood of this 447,968 Km driven E61 530d. Was it a sinister electrical glitch? Or perhaps something else?
The engine was the trusty M57 featuring a single turbocharger which is usually a strong and capable platform even at high mileages except in this case, which upon driving the vehicle on our car park, I found would not accelerate at all. I should also mention, for the reader’s benefit, that in Finland such high Km readings on passenger vehicles are perfectly commonplace. As with all of my fault finds I decided to interrogate the fault memory which can be seen in Fig.1.
The air mass sensor (fault code 004BC2) caught my attention the most due to the significant limitation in engine power. Instead of examining live data, I found it more convenient to visit the parts department, retrieve a sensor from the available stock, and give it a try. This approach proved to be quicker; however, in this particular case, the replacement air mass sensor had no real effect. The car continued to exhibit a lack of power, and to make matters worse, random warning messages regarding the oil level sensor started to appear. At that point, I made the decision to remove the air mass sensor and analyse the original values using the original air mass sensor. Unsurprisingly, they were similar to the readings that I had witnessed as provided by the new sensor. Recognising that resolving the substantial power loss required further investigation, I planned to revisit this component once I had identified the root cause because one thing was sure – it sure as heck wasn’t the air mass sensor at fault.
Digging deeper into this troublesome vehicle whilst starting the engine, a noticeable increase in exhaust back pressure was evident, suggesting a potential issue. During the evidence-gathering stage, it became apparent that this vehicle had possibly undergone a chip tuning modification, as the diesel particulate filter had been cut open and subsequently welded back together. Undeterred by this finding, I resolved to measure the back pressure, even if the internal components of the DPF may have been removed. Removing the Lambda sensor revealed a monolith in good condition – the oxidising catalytic converter. With time, as ever, at a premium, a back pressure reading at 4,000 RPM was taken which resulted in a value of around 230 millibars – way too high. Never one to take live data at face value (think implausible sensor values) a general specification compound meter was hooked up to the back pressure sensor hose tube bore and the same test was repeated. The results were very close to the live data value that I had observed from the Autologic tester so I was very sure that there was a high soot loading within the particulate filter.
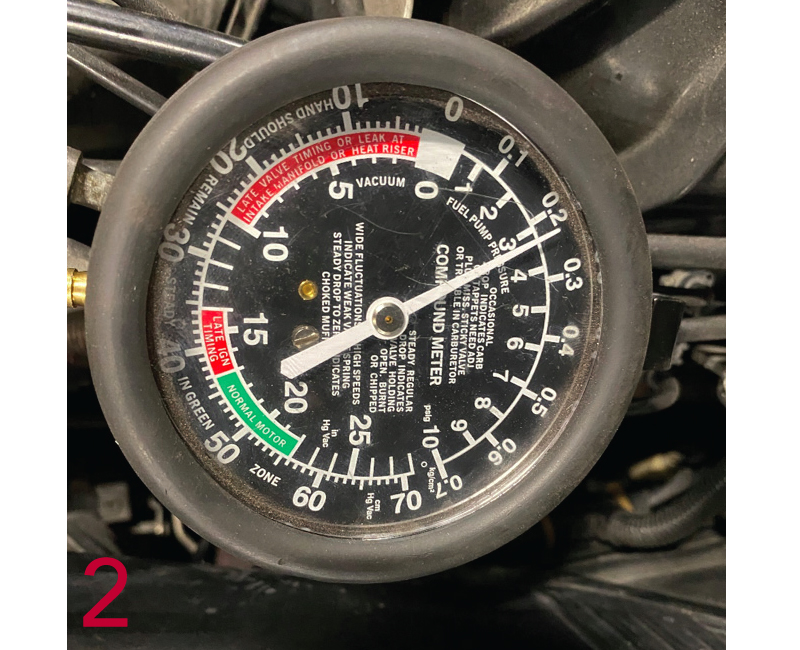
The pressure is on
The initial stage of evidence gathering posed a potential risk of misdiagnosis due to the fluctuating back pressure, which pulsated in waves, occasionally dropping to significantly lower values. These fluctuations could have been easily overlooked, as they caused unusual readings both in the live data and on the manual compound meter. For instance, the initial idle reading of 49 Millibars would randomly decrease to 11 Millibars. At 4,000 RPM cutoff speed the pressure would decrease to 170 Millibars – very strange indeed. It was important to note that I observed this change on the gauge, which, once again, ruled out the possibility of a faulty exhaust backpressure sensor (Fig.2).
The decision to unblock the DPF with JLM fluid was made and carried out. This subsequently dropped the cut off speed pressure from 230 down to 70 Millibars.
With the blocked DPF issue seemingly resolved, it was time to address the second problem: the lack of power. During a road test, it was evident that the car now drove smoothly, but only once the engine reached over 2,000 RPM did it exhibit reasonable pulling power. In the E series BMW vehicles, the BSD bus system was employed, although it has since been discontinued due to its limited fault tolerance and susceptibility to expensive repairs. For instance, if the BSD bus crashes due to a faulty or missing ground or a fault that causes a dominant signal, the DDE (Digital Diesel Electronics) is unable to control the glow plugs, read battery IBS (Intelligent Battery Sensor) data, or regulate the alternator. Additionally, the oil sensor, which is connected to the same bus, triggers a warning lamp. Thus, it is evident that this bus plays a vital role and when it goes wrong it causes no end of problems. I had encountered lots of BSD faults in the past which usually involve removing and thus isolating one bus user at a time then checking the signal on the bus to see if it is restored or not. In this way, as long as one bus user is connected at the minimum, faults can be found quickly. I had a strong belief that this fault would turn out to be something entirely different, perhaps you could call it a fault finder’s intuition.
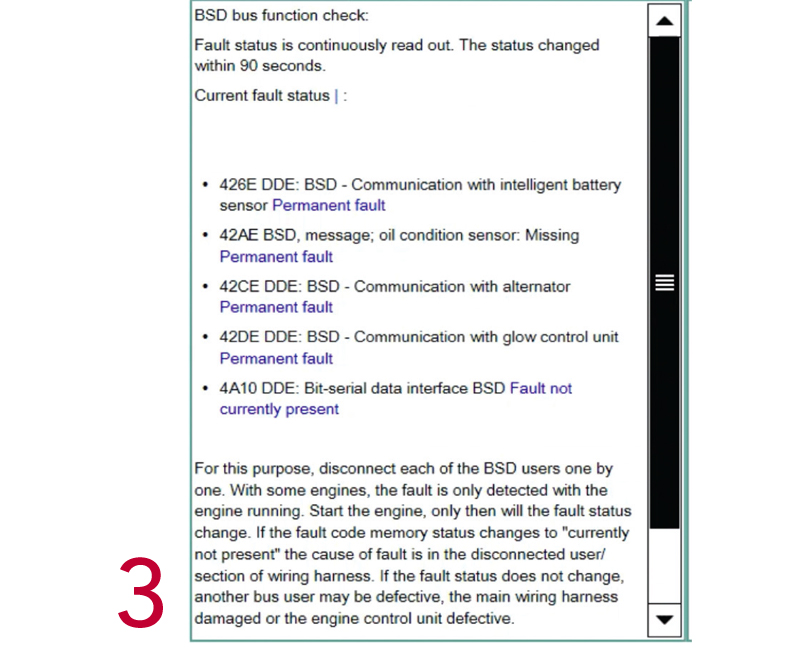
The glow plugs are responsible for heating up the combustion chamber during DPF regeneration if the cylinder temperature is not sufficiently high. Non-functioning glow plugs could certainly contribute to multiple failed DPF events. However, it was perplexing that no DPF fault codes were present, despite the high back pressure that should typically trigger them. Nonetheless, with chip tuned cars, such functionalities can be disabled, so encountering poorly written remaps at Schmiedmann is not uncommon. Our approach is to work around these issues as best as we can. Undeterred I cracked on working out what was flagging up the bus issues (Fig.3).
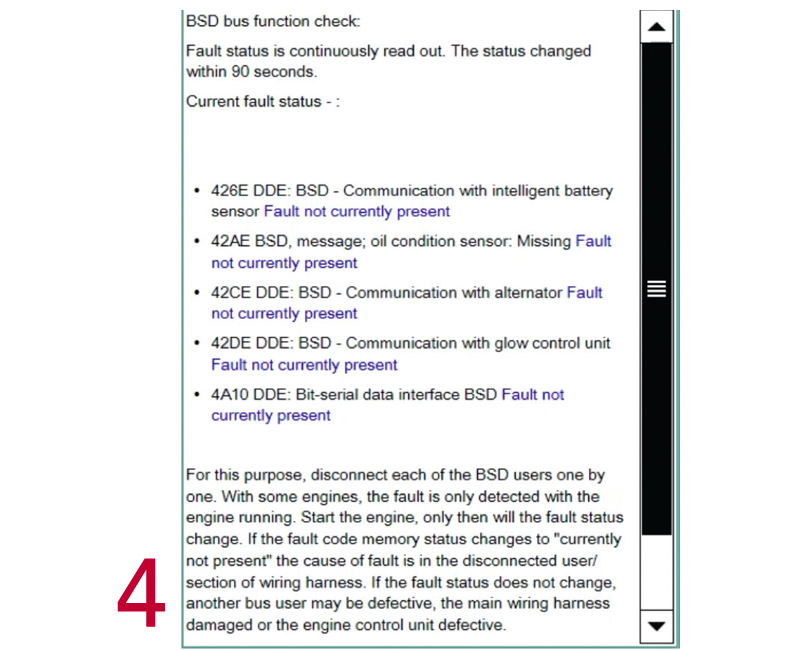
Going for the triple
At times, a seemingly simple issue with a component can have a profound impact on other parts, while unexpected events can surprisingly provide assistance. After investing considerable time into starting the engine, it became evident that the oil warning light would appear during engine cranking and while driving the car under load. Based on this observation and further road tests, I made the decision to establish an additional ground connection for the engine, suspecting that the BSD bus faults were caused by a weak engine ground. By adding a thick jump cable from the jump post to the engine, the previously persistent BSD faults disappeared. However, in order to eliminate any uncertainties, I removed the temporary supplemental ground while the engine was running, only to witness an immediate failure of the BSD. This test was repeated multiple times, consistently yielding the same outcome. In this case, conducting a voltage drop test to verify the ground was unnecessary; a visual examination sufficed. I identified a heavily corroded ground, which was promptly rectified. Subsequent road tests revealed that the BSD faults did not resurface—thus, a successful resolution. However, my satisfaction was short-lived, as the issue of lacking power at low RPM reemerged. At this point, I found myself asking, “how many faults can one car possibly have?”
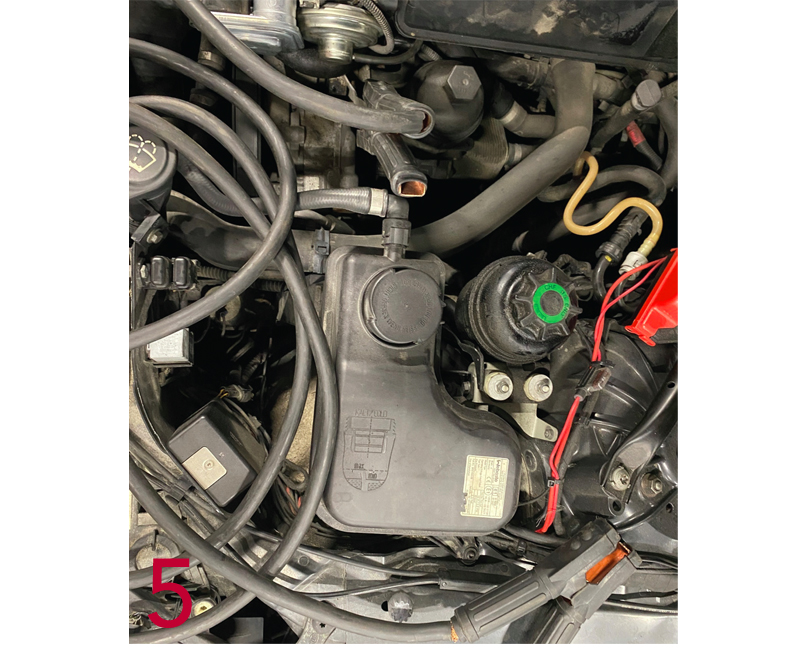
The BSD bus usually has a ground yet the wiring diagrams never show where this magical and highly mysterious ground point is located. Somewhere in the main harness the BSD bus will ground on the cylinder head. In the petrol engines this point is a brass washer moulded into the main engine harness conduit and it is bolted to ground in this way. It was clear that the lack of a decent ground due to massive resistance and draw from the starter motor was causing the BSD to fail under load, especially when cranking the starter motor continuously. In fact, the main ground cable was so worn that it eventually failed to provide enough ground path that the starter motor failed to operate.
With things looking somewhat better, the only remaining issue to address was the lack of power at low RPM. Unfortunately, this led eventually to a complete loss of power, with the car struggling to rev at all. I had been working on this problem for half a day by now and was becoming increasingly frustrated since the problem was getting worse.
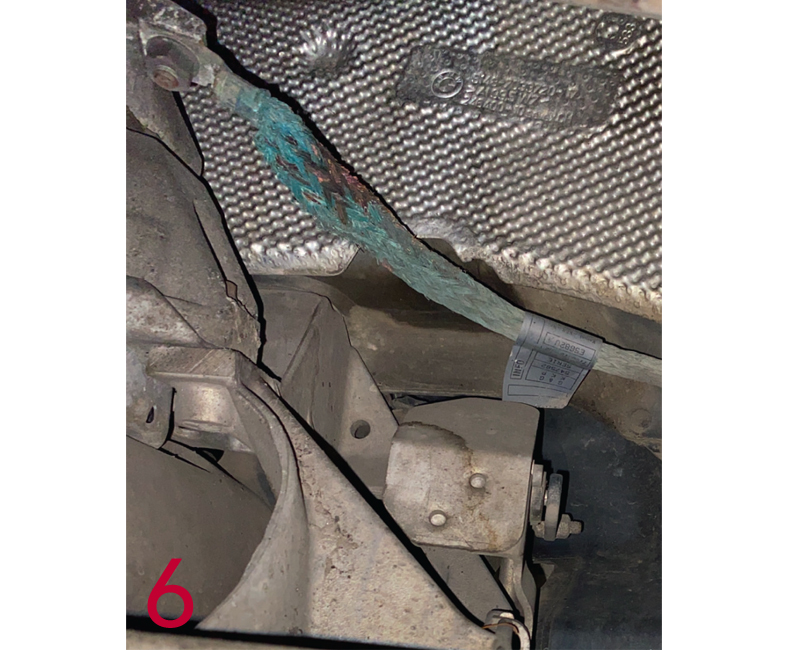
Upon examining the live data for air mass, it became evident that under load, the desired air mass value should be 1,000 Mg of air, yet the actual air mass reading was barely 370 Mg – a significantly low air mass.
To identify the root cause, I focussed on the M57 engine’s air mass measurement and the operation of the EGR valve. The air mass is digitally measured using a square wave signal that widens as the air mass increases. When the turbocharger draws in more air, the air mass reading should rise accordingly. On the other hand, the EGR valve is controlled by a solenoid valve, which supplies pulsed vacuum at a high frequency to open the EGR feed into the throttle body.
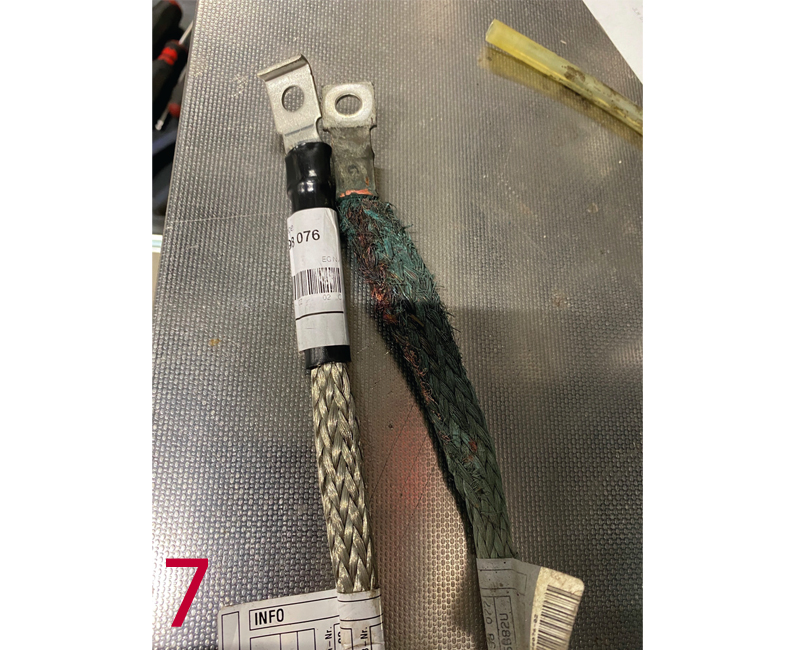
Considering the possibility that excessive, unmeasured EGR feed-in was contributing to the power loss, I decided to remove the intercooler boost hose with the engine idling. However, to my disappointment, the EGR feedin appeared to be closed. Nevertheless, when examining the duty cycle data on Autologic, it indicated that there should have been some slight EGR feed-in. Surprisingly, upon removing the vacuum pipe from the EGR valve, I discovered a lack of vacuum. Subsequent road tests with the disconnected line yielded the best driving experience so far, clearly indicating an improvement compared to previous tests. This led me to suspect that the EGR solenoid, located under the intake manifold, might be intermittently shorting or getting stuck in the open position, allowing full vacuum to pull the EGR feed-in wide open. It was frustrating that no fault codes were recorded.
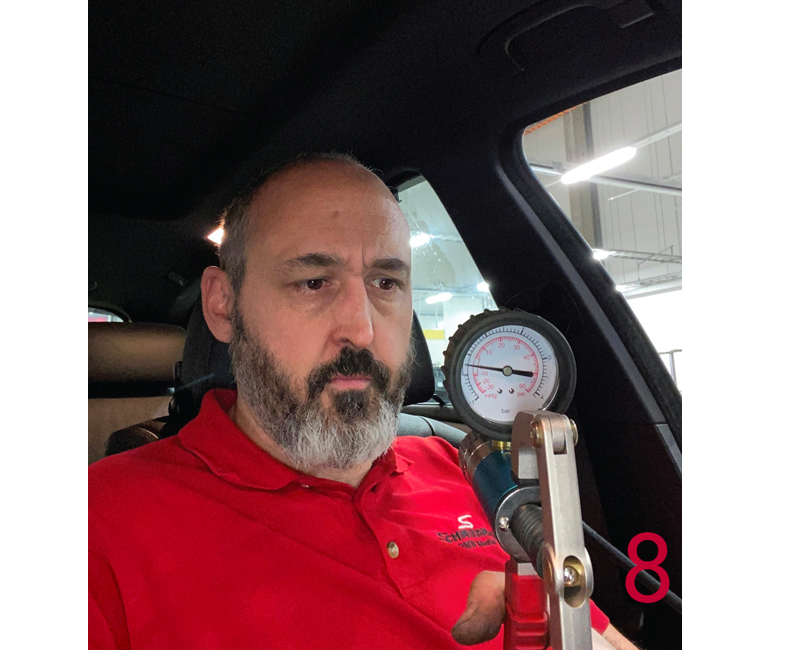
A return to normality
Before deciding to order a new solenoid, I conducted a road test using a handheld vacuum pump and a length of vacuum pipe (Fig.8). While driving without vacuum, the power delivery was excellent. However, when applying a significant amount of negative pressure, I was able to replicate the same conditions, experiencing a lack of power and poor engine response. Analysing the live data revealed an interesting observation: unlike more modern BMW diesels that calculate excess air mass based on unmetered EGR feed-in through the temperature sensor after the EGR cooler, this particular car exhibited the opposite behaviour, with the air mass decreasing as more EGR was fed in. In a more modern vehicle, an excess amount of exhaust air might result in a higher air mass reading.
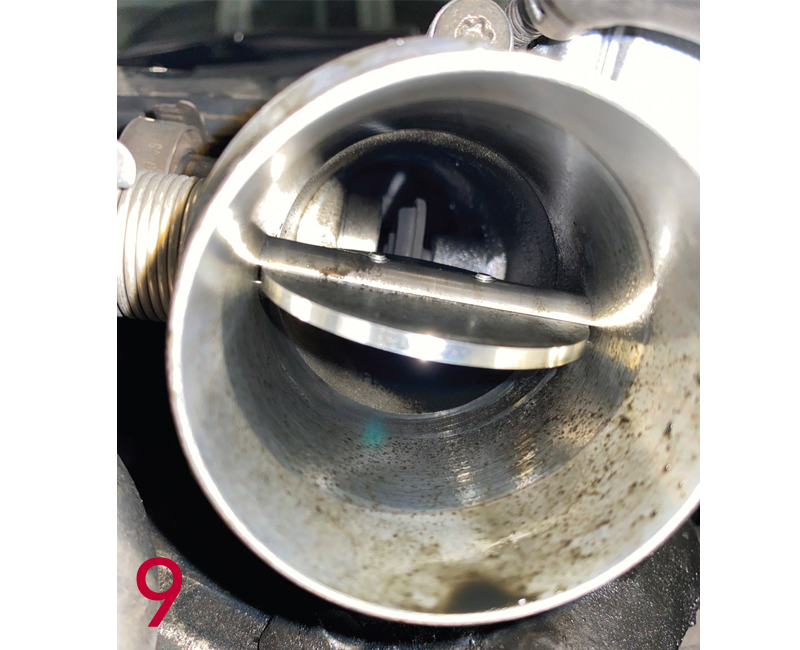
Fault finding can be frustrating, particularly when faults are not present during testing. However, that’s the nature of the task. If it were easy, everyone would be a fault finder. The final job for this vehicle was the fitting of a new EGR solenoid followed by a long roadtest. This resulted in normal air mass values and a smooth and enjoyable ride – finally!
Indeed, this challenging triple whammy of faults really made me pause and contemplate the situation as a whole, prompting me to reflect on what was happening and why. As fault finders, we often have to rely on traditional evidence gathering methods, carefully evaluating data and conducting practical simulations to effectively diagnose and resolve issues. In cases like this one, relying solely on fault codes and computerised test plans is not enough. It is through the process of thorough evidence gathering that we uncover the root causes and through knowledge of how things work we implement successful solutions. This knowledge is useful and even essential especially when faced with such badly “modified” vehicles. So, until the next edition, let us continue our commitment to diligent evidence gathering, eagerly anticipating what challenges the upcoming month will bring.