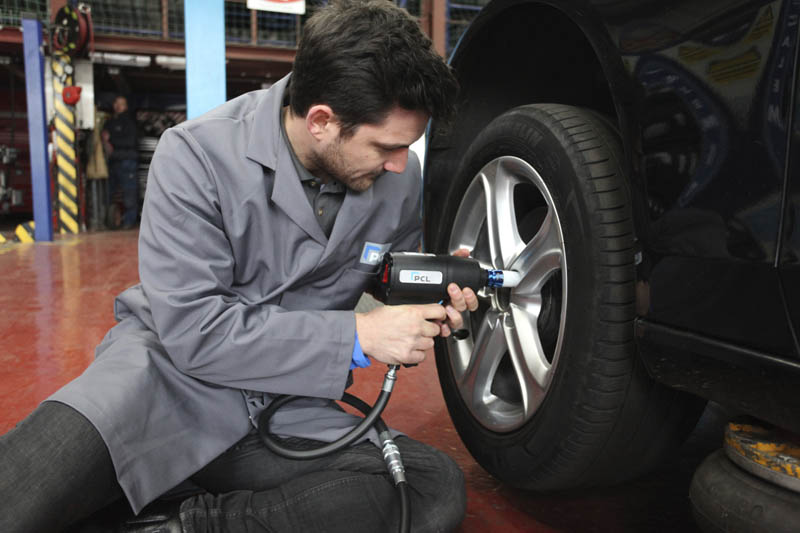
PCL Air explores some of the issues around compressed air and explains what workshop owners need to look out for when purchasing.
Compressed air systems must be kept clean and dry to ensure continued reliability. Precise pressure control also keeps pneumatic systems operating efficiently. Unregulated, unfiltered, unlubricated air pressure can increase equipment wear, leading to reduced tool life and increased costs.
Filter, Regulator and Lubricators (FRLs) ensure each tool receives a clean, lubricated supply of compressed air at the ideal pressure for optimum performance. FRL units should be mounted as close to the tool as possible – preferably at the point of use where the tool hose connects to the system – and checked regularly.
Filters are designed to remove solid particles (e.g. dust, dirt, rust) and separate liquids (e.g. water, oil) from compressed air systems.
Regulators allow the operator to adjust the pressure or flow from the compressor tank to the pneumatic tools to suit specific applications.
Lubricators release controlled quantities of oil into the air system, to help prevent friction and wear of pneumatic tools and equipment. They are installed after filters and close to the point of use.
Five Factors to consider when selecting an air treatment unit
1. Environment
The unit must be designed and constructed from appropriate material to withstand temperature and climate.
2. Lubrication
For frequently used tools like impact wrenches and ratchets, a lubricator is required and must always be fitted at the final stage downstream on the air supply after any filtration. In-line lubricators can be connected on the tool or hose itself.
A fitted lubricator is not always needed, for example if only one air output is available. Also, some tools, including digital tyre inflators and spray equipment, require little or no lubrication, and mechanical inflators may only need monthly lubrication. Therefore, a frequent lubricator is not necessary and may cause impacted performance. Simply oil the relevant tools manually using general air tool oil.
3. Airflow and port size
FRL units must be properly sized to match the required air flow. Significant increases in flow rates can be achieved using larger ports but changing port size within a system can affect the fine tuning to flow rate, which may be required for some applications.
Always refer to the equipment manufacturer’s recommendations and select an FRL with an air flow capacity greater than the tool’s requirements.
4. Filtration level
When considering the level of filtration required, you must factor in the unit’s micron rating. Most industrial equipment and tools like impact wrenches only need 10-micron filtration, whilst more sensitive components and instruments typically demand 5-micron filtration. Food, beverage and pharmaceutical applications routinely demand even finer filtration. Ask the equipment manufacturer for exact filtration requirements.
Don’t opt for a finer filter than necessary. Smaller micron-rated filters have higher pressure drops across the filter, so opting for a 5-micron filter when a 10-micron unit is enough will increase energy consumption and equipment wear, leading to higher operating and maintenance costs.
5. Drain type
Standard filters commonly feature a manual or semi-automatic drain at the bottom of the filter bowl. A manual drain requires the operator to manually release the accumulated solid particles and liquids from the filter, while the semi-automatic drain will automatically drain when the system is depressurised, however the operator can still manually open the drain when in use.
Some filters feature a built-in auto drain, alternatively auto drains can be purchased separately. Designed to remove all contaminants from the filter automatically, auto drains typically feature a float which will open the drain when liquids reach a certain level, the drain will also open when the air system is depressurised.
Auto drains are recommended for applications that require high/continual usage or humid environments where frequent drainage is required. Auto drains are also ideal when the filter is installed in a hard-to-reach area.