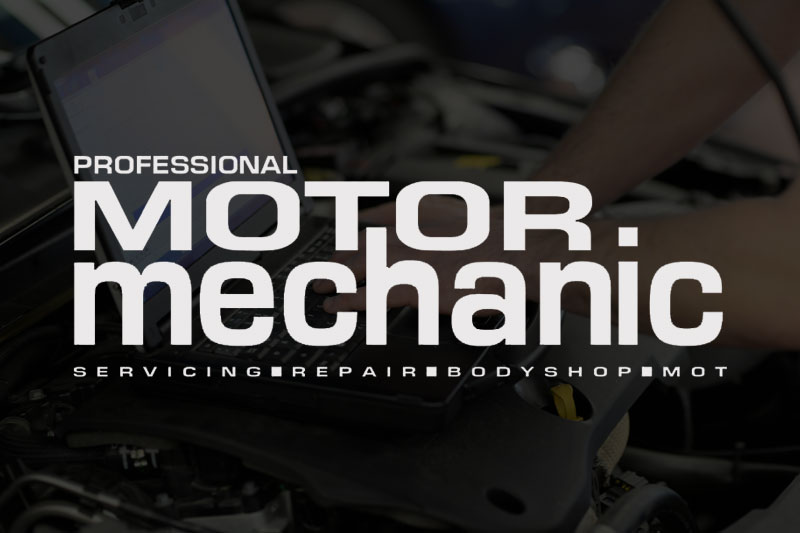
In the not-so-distant past, and despite the major manufacturers naturally investing in improving the performance of their products, most batteries were all generally of lead-acid type, designed to cater for large current discharge when starting the engine and subject to continuous charging while the vehicle was in use.
As far as the workshop was concerned, providing the battery was maintained properly – topped up with de-ionised water, kept from excessive discharge and regularly charged etc – it would provide a reliable source of power until it inevitably needed to be replaced.
Replacement was a simple and straightforward process, which was only complicated by the fact that in more recent years a current had to be maintained in the system to ensure the power to the ECU and related equipment wasn’t lost.
Start-Stop arrives
However, the introduction of Start-Stop vehicles has driven a major change in battery technology. Start-Stop (otherwise known as micro-hybrid) engines have become the preferred route for most of the VMs in order for them to reduce the fuel consumption of their vehicles and achieve the EU requirement for fleet average vehicle emissions.
The traditional lead-acid ‘starter’ battery is not suitable for this type of engine and, therefore, cannot be used. Instead, it requires a battery that can deliver the starting power of a traditional automotive battery with the cyclic (charge, discharge, charge etc.) capacity of a specialist mobility battery. The result is the absorbent glass mat (AGM) battery, which was first developed by VARTA® for whom Manbat is the UK’s largest supply partner.
Let’s go through some of the key questions about this sort of technology:
Q. What challenges do technicians face when changing AGM batteries compared to lead-acid based batteries?
A. With a Start-Stop vehicle fitted with an AGM battery, the technician cannot just replace the battery in the way that they have done with a traditional battery.
Instead, as the battery is intricately linked to the vehicle’s on-board electronics via a battery management system (BMS) or intelligent battery sensor (IBS), it has to be integrated into the system and paired with the BMS/IBS, which requires specialist equipment. Without the equipment to assist the technician and introduce the battery into the system, the vehicle could illuminate error messages on the dash, fail to charge the battery or simply not start at all.
Q. Is dedicated training on how to test, diagnose and fit these new batteries a requirement?
A. Training is particuarly important because the number of potential faults in a Start-Stop system is far greater than for a traditional electrical system. Becuase the engine is switched off as frequently as possible, and only restarts when the vehicle needs to move off or when the state of charge of the battery drops to a pre-determined level, the BMS is extremely complicated.
Therefore, the correct testing procedure and fault diagnosis is vital. This is also complictaed by the fitting challenges mentioned previously.
Q. Will any AGM battery do the job?
A. As with every aspect of the trade, fitting the correct battery for the application is paramount. For entry-level or smaller Start-Stop vehicles, for example, an AGM battery might not be the appropriate replacement, as the original fitment could be an enhanced flloded battery (EFB). Although these batteries have similar characteristics to AGM batteries, they are not the same and the two should not be interchanged. Likewise, just installing a larger capacity lead-acid battery is no solution for Start-Stop battery replacement.
To prevent error messages and other installation-related problems, quality Start-Stop batteries should be the first thought when being replaced, as these will have the necessary 2D codes to ensure the battery is a ‘match’ for the vehicle and will be ‘accepted’ by the BMS/ECU.
Q. Are there any specific procedures for the removal, fitting or disposal of AGM batteries?
A. Technicians working on Start-Stop vehicles will find that there is no guarantee that the battery will be under the bonnet! Therefore, they need to have access to accurate technical information, such as TecRMI, or similar workshop-related technical data, to pinpoint the exact location of the battery, be it in the boot floor or, as is the case in at least one application, beneath the front passenger seat!
Handling AGM batteries themselves is no more hazardous than their traditional lead acid cousins, in fact, as they are general completely sealed units, chemical spillage is actually less likely; however, they are heavy, so health and safety procedures should obviously be followed carefully.
When it comes to responsible disposal, workshops have to understand their environmental responsibilities and ensure batteries are disposed of legally, but they should also be aware that they could benefit financially from responsible battery disposal as batteries have a ‘scrap’ value.
Q. Are there any specific maintenance requirements?
A. Providing the vehicle’s BMS is working as it is intended, these batteries require no specific maintenance. There are fully-sealed and maintenance-free.
Q. Will garages need to upgrade their equipment to work on Start-Stop vehicles?
A. Without the correct equipment, workshops cannot test the battery and the associated elements with the Start-Stop system. this equipment allows them to diagnose whether a fault lies with the battery, alternator, BMS, IBS or elsewhere.
Q. What advice should garages give their customers when their battery needs replacing?
A. Workshops should choose a quality battery when undertaking replacement, but this is even more important when working on Start-Stop vehicles for the reasons previously discussed. VARTA is the largest OE battery supplier to Europe’s VMs and has led the development of Start-Stop technology.
As a result, by fitting VARTA, a like-for-like replacement is highly likely, but whatever the original battery, the necessary quality is guaranteed.
For non-Start-Stop applications, it is recommended that you ensure the correct specification battery is selected by using an application guide, such as the one utilised in Manbat’s recently launched Lucas Battery Catalogue.
Only when the vehicle has been fitted with additional electrical equipment, or when the vehicle has been modified to cope with extreme conditions, does the battery need to be upgraded. In this instance, the enchanced performance of an AGM battery could be an advantage, even though the vehicle doesn’t utilise a Start-Stop system.