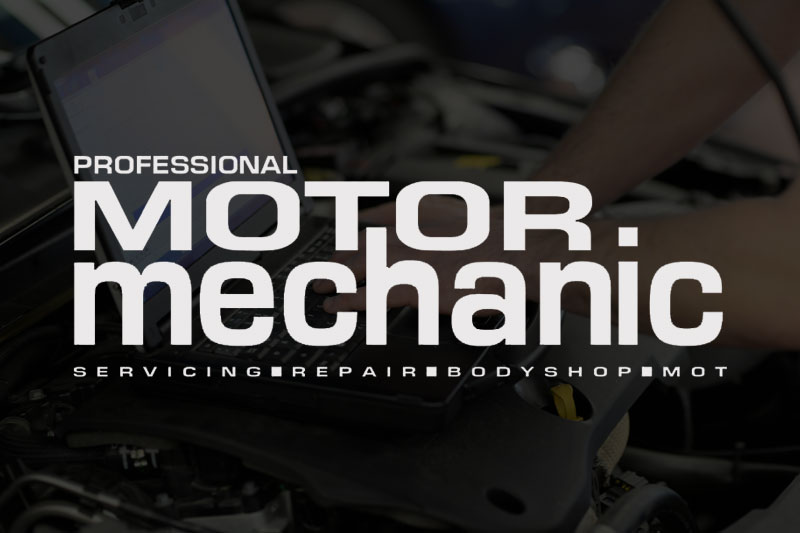
In the event that a turbocharger needs replacing, yet the actual cause of failure is not remedied, it will almost certainly be damaged again. Inevitably, the new turbocharger will automatically become the first suspect. Whether the turbocharger really was to blame is often only investigated after the supposedly defective component has been replaced therefore, in order to save time, frustration and money, it is advisable to identify the actual cause of damage for every failure.
SUSPICIOUS NOISES: WHISTLING AND CLANGING
When whistling noises occur immediately after installation, it is often hastily concluded that a crack in the turbocharger or a manufacturing defect is the cause. However, an examination of the returned turbocharger usually reveals something else:
A gasket inserted the wrong way around
This reduces the diameter and therefore also the flow rate, which can lead to whistling noises and/or a decrease in performance.
Incorrect fit of the hoses/components of the charge air line
This can cause air to escape and, as a result, whistling occurs.
Incorrect mounting of the housing
For certain types of turbochargers, the compressor housing is adjusted by loosening and tightening the mounting screws. If the screws are not tightened correctly, they can become loose during engine operation. The resulting angle of the housing causes the impeller to strike the housing, thus audible as “scratching” or whistling.
Detached metal
Rattling/clanging can indicate a detached piece of metal in the exhaust manifold. This error must be eliminated immediately to avoid major turbocharger and consequential damages.
Correctly fitted gasket Incorrectly fitted gasket
INDICATIONS OF BLOCKAGES: SMOKE FORMATION AND OIL LOSS
Smoke emissions and loss of oil are among the most common reasons for an unnecessary turbocharger replacement.
Almost all series turbochargers have hydrodynamic bearings. In this case, oil acts to “separate” the moving parts. An adequate supply and removal of oil is therefore essential for the durability and operation of the turbocharger. If the oil supply is hindered or the oil pressure is too low, an adequate lubricating film cannot form; mixed friction occurs between the shaft and the bushing, resulting in major turbocharger damage. Clear indications for inadequate lubrication include a loose nut on the impeller, a broken shaft (pictured, left), or discolouration due to high temperatures. If the defect is not remedied prior to the installation of a new turbocharger, then this one will also become damaged immediately after installation.
A blocked return line or excessive crankcase pressure can clog the oil return (pictured, right). Because the oil can no longer flow out into the oil sump after lubricating the bearings of the turbocharger, it accumulates in the bearing housing. At the same time, the oil pump supplies fresh oil to the bearing points for lubrication and cooling.
The oil must now somehow flow out of the bearing. However, since the return flow is blocked due to the clogged line, it searches for another path: despite the sealing piston rings, it is forced into the compressor and turbine side, where it enters, is carbonised, or is burnt in the combustion chambers via the intake air and the exhaust system via the turbine.
Broken shaft shank Carbonised oil return line