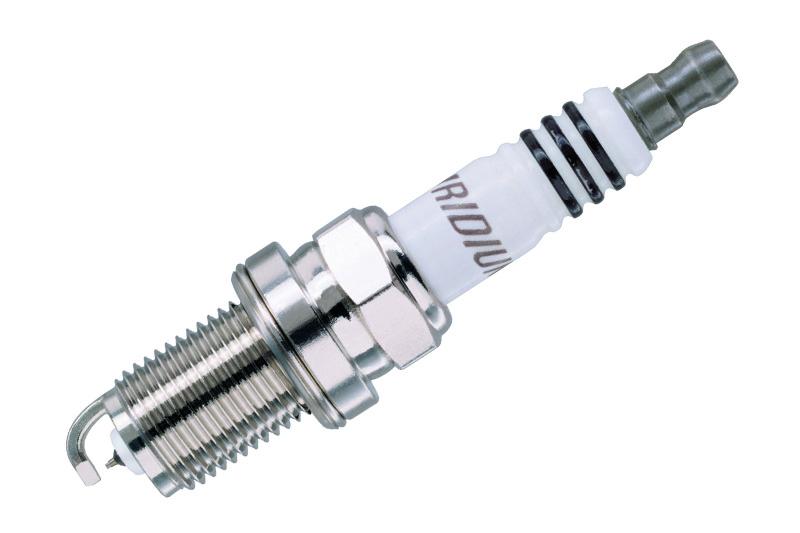
Ron Merralls of NGK takes a detailed look at the anatomy of a modern spark plug.
When it comes to spark plugs, the section most people are aware of, and the part that is so crucial to its function, is the insulator. The familiar white ‘ceramic’ is a part that cannot be taken for granted. It has to prevent the escape of 30,000V or more.
The insulator is in fact alumina, which is aluminium oxide – a mined substance obtained from bauxite. It is chosen because after being processed, formed, sintered and glazed, it offers superior insulation properties, resistance to chemical attack, extreme hardness and high strength. Although the insulator on a modern plug looks remarkably similar to those of days gone by, NGK’s expertise in this field means that design and production methods have remarkably increased the dielectric strength and resistance to thermal shock.
Most modern plugs incorporate a resistor to guard against electrical ‘noise’. NGK’s accurate and stable resistor material is constructed from glass impregnated with carbon. Altering the ratio of the substances means that the vehicle manufacturers’ value can be met and will not break down or alter over the service life of the plug.
The historical preferred choice of material for the centre electrode has been a copper-cored nickel alloy. Nickel alloy is a material which provides a good service life and the copper provides a great method of ensuring heat is conducted away from the electrode tip quickly.
Platinum and iridium alloy plugs are more often the choice of vehicle manufacturers now. NGK laser welds small pins of these precious metals to the electrode tip. Iridium is the best material, as it is truly a precious metal – being one of the least abundant elements. It is chosen for its hardness, resistance to heat, oxidisation and wear. Although the pin can be just 0.4mm in diameter, it will last longer than a conventional 2.5mm diameter nickel alloy electrode plug, whilst also significantly improving ignition performance. It is worth noting that all NGK precious metal plugs still incorporate a copper core in the main centre electrode. As a result of these benefits, iridium plugs in particular are used extensively in race engines and are becoming increasingly popular as the upgrade choice for road vehicles.
Ground electrodes can be visually different when comparing different part numbers – some plugs have one and others can have up to four. However, plugs that look the same often have unseen differences in this area. Subtle differences in their shape, construction and material often exist. High specification alloys are often required and some are a layered copper design. This is the result of working closely with VMs to produce the perfect plug for the engine.
Design characteristics and material are often crucial to the engine type to guard against overheating and vibration fatigue. Developed for the VMs, and more recently available to the aftermarket, are the DFE (double fine electrode) plugs which incorporate a precious metal pin welded to the ground as well as one welded to the centre electrode. This pin-to- pin spark discharge design is the most sophisticated in obtaining superb ignition performance coupled with long life.
The NGK factory invests heavily in quality, research and development and pushes technology forward to meet the VMs’ requirements both now and in the future.