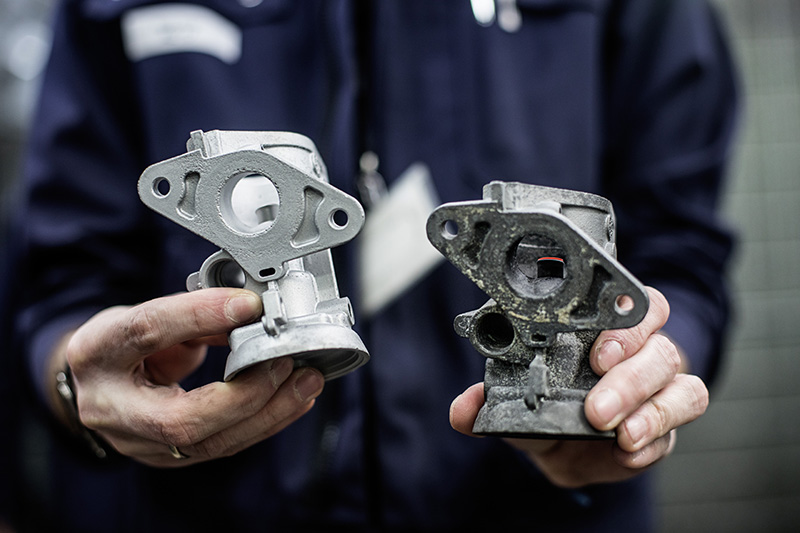
BORG Automotive explains all you need to know about EGR valves.
The concept of Exhaust Gas Recirculation was developed by General Motors in the 1970s. The goal was to reduce emissions of nitrogen oxides (NOx), a gas harmful to health. One of the central elements of the EGR concept is the EGR valve, which controls the flow of recirculated exhausts. In most cases, if failure of the valve occurs, it needs to be replaced by a new one, which is a costly repair job. That’s why a growing number of workshops use remanufactured EGR valves from BORG Automotive.
Today, the concept of EGR is common to both petrol and diesel cars; ever stricter emission regulations have made it vital for modern engines. As the conditions for producing NOx are best at very high combustion temperatures, diesel engines are very good at producing NOx, as there is a very lean fuel mixture and very high pressure at ignition. However, many modern petrol engines have such high temperatures at combustion that they too produce a lot of NOx.
But what does EGR mean exactly? To keep the answer short and simple: EGR redirects a certain amount of exhausts from the manifold and adds it to the freshly aspirated air. In doing so, it reduces the share of oxygen in the air-fuel-ratio, thus decreasing the combustion temperature in the cylinders.
Thanks to this temperature reduction, up to 50% less NOx is emitted. Depending on the engine, the share of recirculated gases varies from 5 to 35%.
In many cases a cooler is added to the recirculated exhaust gas, cooling the gas using coolant from the engine, which cools down the gas, helping to make it possible to add more exhaust to the intake at a lower temperature. In many cases, these also have a bypass valve to allow gas to flow around the cooler when warming up.
On some newer vehicles there are two valves adding exhaust to the intake – one taking gas from behind the DPF and one taking the high pressure gas from the exhaust manifold.
EGR valves: the gatekeepers
In general, the EGR valve operates at partial throttle and under 2,500 rpm. It is part of a complex regulated circle steered by the engine control unit. The ECU uses data supplied by various engine sensors and RPM speed to calculate how much exhaust needs to be recirculated and instructs the EGR valve accordingly. Simply put: A high EGR flow is mainly used at cruising speeds and at midrange acceleration. At low speeds and partial load, the EGR flow is low. There are also times when there is no EGR flow at all, such as when the engine is warming up or idling – or when it runs at full throttle.
In principle, when servicing cars, workshop personnel can come across four types of EGR valves, which also mirror the further development of technology over the past decades: pneumatic; solenoid; DC motor powered; and electronically controlled.
- Pneumatic EGR valves feature a vacuum air inlet, a membrane and a return spring. The inlet is operated by negative pressure. The inlet manifold pressure serves as control parameter
- Solenoid EGR valves are operated by an electric unit, which is installed on the valve. They were developed to become independent from the manifold vacuum and to allow for a more precise and quicker adjustment of the valve. They run at 12 V and come with a three-pin terminal linked to the ECU. Inside of the solenoid unit is a plunger surrounded by a coil. By energising this coil, the ECU pushes the plunger up or down to open or close the valve
- EGR valves with DC motors offer increased opening force and a quicker response time. They feature an electrical motor and a gearing system (also a sensor which provides information about the position of the valve), which transfers the motor’s movement to the valve cover
- Electronically controlled, digital EGR valves include an integrated computer to regulate the valve movement. The digital unit monitors the position and condition of the valve and communicates constantly with the ECU
The most common sources of failure
As with all parts, EGR valves are subject to wear. If they operate under bad conditions, they might break down before they have reached the end of the originally planned lifespan. The most common sources of failure include suboptimal injection, failing injectors and defects that cause higher oil consumption, causing abnormal amounts of soot to be produced at combustion. Also, the driving pattern of the vehicle can have influence on the lifespan of the valve – short drives with cold engine and low loads tend to build up soot in the exhaust and therefore also the EGR. This all leads to an abnormal accumulation of carbon deposits, and a stuck valve.
“If an EGR valve defect occurs, the workshop would be well advised to search for the true source of the failure,” says Jesper A. Jensen, Product Manager at BORG Automotive, European remanufacturer of EGR valves. “If the cause of the damage is a faulty sensor or a defective injection, a new EGR valve would only solve the problem for a short period of time. If the underlying malfunction is not fixed properly, any EGR valve will fail too early.”
In some cases, the engine light can be switched on and an EGR failure can be stored in the ECU, even when the valve is still working – most often this can be caused by a faulty air mass sensor, which is used to calculate flow of EGR, or clogging of tubes in the EGR system.
Remanufactured EGR valves
Using original parts for replacement of a faulty EGR valve is costly and even more expensive the younger the car is. To offer a repair of uncompromising quality at a favourable price point, a growing number of workshops are turning to remanufactured parts. BORG claims to offer the widest range of EGR valves with more than 400 part numbers, and a European car parc coverage of 95%.