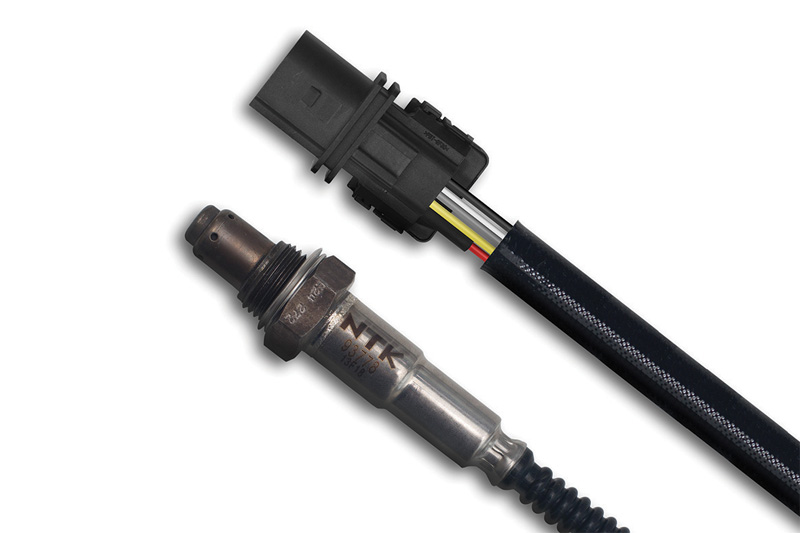
NTK, a brand of Niterra, explains what garages need to know about lambda sensors, why they need to know and offers some technical advice.
Motorists today can turn to the workshop as a fantastic source of knowledge and services for their increasingly complex vehicle. They require their vehicles to be more economical and environmentally friendly than ever without compromising performance, so the pressure is on garages to be more emissions savvy than ever.
One way to help optimise the car’s engine management when entering the workshop for service or maintenance work, is by fitting a new lambda (oxygen) sensor, as they slowly degrade over time.
This is often the simplest step to breathing new life into tiring engines with the benefits of fitting a new lambda being immediate and measurable as they are said to support optimum egine efficiency, reduced emissions and increased economy.
Wide coverage
Garages need to be able to fit high-quality parts to their customers’ vehicles safe in the knowledge they are providing their customers quality and performance they can rely on. With a range of more than 400-part numbers from OE to IAM giving 76 per cent coverage of European vehicles in operation, NTK is said to be the number one lambda choice of most of the world’s leading vehicle manufacturers.
Becca Knight, marketing manager for NTK brand owner Niterra UK, said: “As the leading supplier of lambda sensors both for OEMs and the aftermarket, Niterra is continually providing sensors which help to make engines cleaner, more efficient, and our wide application coverage makes NTK the go-to solution for the car on the ramp.
“Many part numbers are brought into the aftermarket from the OE side of our business so motorists can be confident that their engines are fitted with components which meet or exceed vehicle manufacturers’ specifications. By choosing NTK they are not only selecting performance parts for their customers but also lots of support for the technician and the workshop.”
Niterra advises garages to fit a new NTK lambda sensor whenever they replace a vehicle’s catalytic convertor as a worn or failed sensor can result in drastically reduced control of the fuelling system which could result in increased fuel consumption, uneven running, generally poor performance or failure of a MOT emission test.
The company also advises garages should always fit a bespoke OE-quality lambda sensor for the vehicle and application they are working on, and steer well clear of ‘universal’ sensors. A ‘universal’ lambda sensor is designed to cover as many applications as possible by splicing in the old connector from the unit being replaced. In theory, this sounds like a good idea. In practice, the potential for a mismatch with the vehicle’s system or subsequent premature failure is very high.
Power of ceramic
Niterra’s long pedigree in producing NTK oxygen sensors dates back to the 1980s since when the reduction of harmful emissions has made significant advances, not least thanks to the development of new technologies and extensive research.
Today, highly efficient ceramic heaters in lambda sensors ensure that the sensors start measuring sooner and respond faster.
To achieve more accurate measurements to meet the ever more stringent Euro emissions regulations, huge efforts are being made in the continuous improvement of the ceramic components. In addition, a variety of sensor types have been developed catering to specific applications. They include broadband sensors and lambda sensors whose electric resistance changes depending on the air-fuel ratio.
With this dedicated engineering background, Niterra has the technical expertise to help technicians solve many problems they face in the workshop for lambda sensors.
Lambda sensors are part of the NTK portfolio of vehicle electronics that includes NOx, MAF/MAP, camshaft/ crankshaft, EGT sensors, EGR valves, along with the recently introduced exhaust pressure sensors, comprising of differential, absolute and high-pressure type sensors.
Technical tips:
- Often a fault code can be read that correctly relates to an issue with the lambda sensor and replacing it can clear the code. However, upon the removal of the sensor, closely inspect the inside of the connector for any oil contamination – however slight. Some vehicle models are known for an engine oil leak to allow oil to enter the wiring loom, migrating to other areas of the loom via capillary action – which is the root cause of the fault code.
- Fault codes recorded for lambda ‘sensor 2’ (rear) can lead to the query that ‘the sensor required has more wires than the one supplied’. NOx sensors always have more wires than a Lambda sensor and outwardly are very similar in appearance, the lambda sensor will be close by!