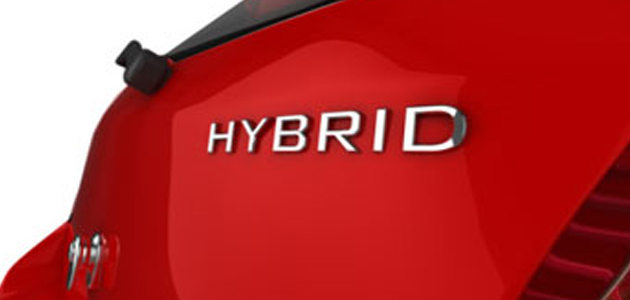
The RMI’s Independent Garage Association (IGA) has made some serious strides in its offering for independent garage members over recent times. One major element of this is the introduction of free training for technicians, delivered on site, in an effort to arm garages with the skills and knowledge required to service and repair the vehicles and technology of today. Hybrid vehicles represent one current gap on the IAM list with repairs still ‘out of reach’ for a huge number of outlets who may be lacking the health and safety awareness and skill-sets required to undertake hybrid servicing.
The popular electric/hybrid – with 4.5 million vehicles sold worldwide – is a favourite for many reasons, not least the fact that it is tax-free and exempt from the London Congestion Charge thanks to its Euro 5 compliant, high energy efficiency levels. For these reasons, among others, it is expected that many more will enter the UK market over the next number of years, with servicing opportunities presenting themselves to the aftermarket.
Taking centre stage for our day of training on the fundamentals of hybrid technology, alongside Harish’s Auto Services, was a brand new 2012 Toyota Prius Hybrid. RMI Technical Trainer, Lee Simonds wasted little time in getting on to some of the car’s characteristics, stating: “Miles to the gallon is very good as far as the Prius is concerned. For frequent motorway drivers, you’re looking at around 58 MPG while town driving goes into the 60s, and maybe even the 70s. This is an efficient, low maintenance petrol engine and requires an oil and filter change every 10,000 miles.”
In the trunk
Unlike conventional vehicles, inside the trunk of the Prius is a 201.6V Nickel Metal Hybrid (NiMH) battery which sits across the whole width of the boot and is utilised with the sole purpose of looking after the hybrid system. Lee explains: “Inside this high voltage battery is a PCU (Power Control Unit) which looks after and controls the NiMH battery. In total the battery weighs about 29kg.
“The NiMH battery contains 28 modules, at 7.2V per-module, which are connected in series. Meanwhile the battery ECU monitors the whole current flow of the battery pack and if one module drops as much as one volt, the hybrid system will shut down.”
Also located in the boot is a standard 12V lead acid battery (pictured below), normally found underneath the bonnet in its own tray.
Describing the role of this battery and why it is housed in the boot, Lee says: “The 12V battery that you see here is for the vehicle electrics, lighting (interior/exterior) and the other electric functions that the vehicle requires. The battery gets its charge from two large motors in the gearbox that’s located in the engine.”
With the technicians in attendance clearly surprised to find out the 12V battery played such an important role in the Prius, Lee went further by saying: “This 12V battery works hand-in-glove with the hybrid battery. Put simply, one can’t work without the other.”
Under the bonnet
You won’t find an alternator or starter motor underneath the bonnet; instead there are two big motors (MG1 AND MG2) in the gearbox that do the job of the aforementioned components. “The inverter, located inside the engine, is water cooled through the radiator and also contains a booster,” Lee explains. “There are three capacitors – over 100A each – which smooth out the power. Additionally, there’s an integrated circuit crash sensor which sends a signal to the hybrid ECU and it also monitors for SRS (airbag) deployment signals, so in the event of an accident, the HV battery pack is isolated by the PCU.”
Stressing the importance to be extra cautious when working on these modern hybrids, Lee said: “As it’s a hybrid, it’s very quiet. These cars run on motors so you can’t hear them. It’s important that you’re extra careful when dealing with them as well. When you exit the vehicle you must always remember to switch the power off.”
Safety first
Summing up just how dangerous the high voltages contained in these vehicles can be, Lee said: “You can’t see it, you can’t hear it, you can’t smell it – however you CAN feel it!”
The industry standard states that workshops should have a designated hybrid work bay, which just isn’t practical in the real world, as most independents simply don’t have the room. In reality, what you really need is the correct signage, according to Lee: “Good, clear signage all around the hybrid vehicle is imperative. You should have at least one sign on the roof of the vehicle and some signs around the car to let the other guys in the workshop know you’re working on a high voltage vehicle.”
For your own safety, it is also important to make sure you have all the relevant Personal Protective Equipment (PPE) essentials before commencing work. “Gloves, certified to 100 ac V, boots and goggles are the main items needed when working on these vehicles,” said Lee.
We’re not going to give away all of the details of Lee’s presentation here, but one of the clear messages from the training was the fact that hybrid vehicles are no different to full-petrol vehicles in terms of servicing and MOTs – in fact Lee stressed this point on more than one occasion. There are some procedures that require the correct health and safety knowledge and equipment before you undertake them, but this simply involves proper training and understanding, such as that provided by Lee and the RMI.
At the end of the workshop the mechanics at Harish’s Auto Services were given a quick ‘Knowledge Assessment’ to see just how much they took in and understood. Each mechanic passed with flying colours and everyone received a certificate for their efforts.
It was clear from the time we spent with the group that the workshop was useful and left the mechanics feeling confident and empowered in terms of understanding the safety measures they should follow when working on hybrid vehicles. As such, we would recommend other garages consider taking the RMI up on their generous new training offer!