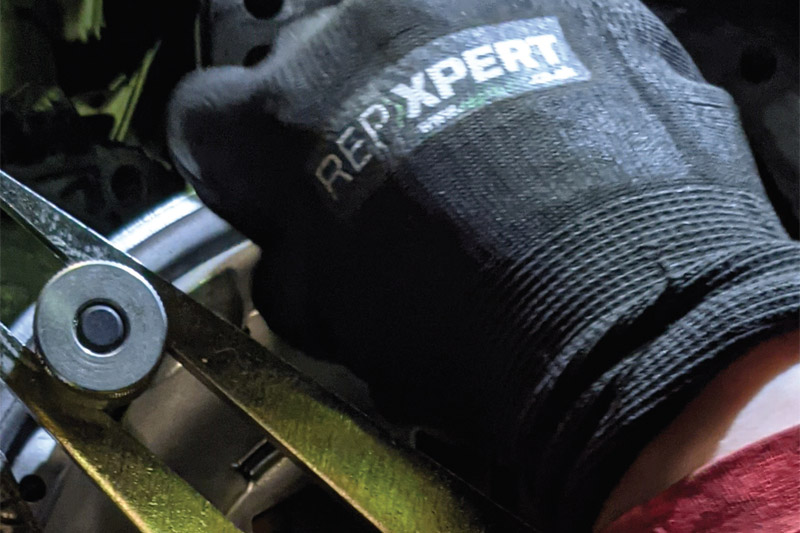
Changing a clutch can be lucrative business. Empowered with knowledge and tools, it can fulfil the client expectation that your workshop can look after them should things go wrong. In this case study, Hayley Pells of Avia Autos explores the decision process involved to sell a Dual Mass Flywheel (DMF).
Originally the main family vehicle, the presented 2009 Renault Megane ended up becoming the school run mode of transport. A recent service included the rear brakes – noticing that the fronts were not far behind with drop links and top mounts required, a presentation of clutch failure meant working out ‘How much?’ was on the cards. I constructed an estimate that included the DMF.
A couple of battle scars, but a surprisingly crisp interior for the age, I’ve completed more services and light repairs on this vehicle than I care to remember. It had never previously presented any tricky faults or required a recovery wagon…it may even still have the original battery. The family have some sentimental attachment to this vehicle, so options were discussed, and the good history of the car meant it was saved from the scrapyard.
The practical approach
Getting the box out was problematic and frustrating, but with the help of penetrating oil, I eventually had the components carefully laid out on the workshop table and the gearbox successfully removed.
Clutch unbolted and inspected, there was no clutch material to speak of. I have not seen anything like it for an age. Photos taken for posterity, we removed the unit and the DMF was exposed. At this point, I would not have faltered – I had estimated for the DMF, therefore one should be fitted. Why bother with the time of measuring play? Full of curiosity after a recent REPXPERT Teatime Training session, I decided to test the DMF to see if it was fit for purpose.
That day, I had access to not only a specialist Sykes-Pickavant tool, but also a specialist pair of hands to help wield it in Alistair Mason, a REPXPERT for Schaeffler, who just so happened to be visiting.
Using the tool was an interesting experience. Alistair pointed out that it was possible to check the rotational free play of the DMF using a method of counting teeth or degrees on the attached gauge. This information could then be cross referenced with the manufacturer’s specifications through the Schaeffler REPXPERT app.
We found that the DMF was just within tolerance, so a debate occurred – would this flywheel need replacing? The unit was an example of the years of careful driving and maintenance by the owner, so should it be reused?
I asked Alistair for his opinion. The poor state of the friction plate called it for him, and the obvious heat transfer raised questions about further damage. The work would be completed as planned, and my understanding of the internal workings, as explained by Alistair, allowed me to talk with knowledge and confidence to my customer about why it was the right decision.
The tools for success
Replacing the flywheel was uncomplicated, but I did need assistance to catch the weight of the flywheel as I unbolted it. Alistair then deployed his second case of goodies in the LUK fitting tool. If any money was going to be spent, I’d like that Self Adjusting Clutch (SAC) fitting tool. When the first opportunity for private Googling presented itself, I had a look at how much it costs and concluded that for the number of clutches I do, I could investigate hiring one.
During the clutch installation process, I questioned Alistair on whether there was a workaround without the tool. Alistair explained the clutch could be fitted without it, but there are risks of de-adjustment, judder, or possibly stripping the threads out of the flywheel. The tool removes a costly risk from the job, which if went awry, could easily match the price of purchase.
The DMF came with a bulletin for the fitment of the concentric slave cylinder. With the guidance on what to do with the rubber washer ahead of the bleed nipple noted, it was replaced and the old one was set into the packaging with the old components out of habit.
Time to reintroduce the box! It was coaxed back into position with the transmission stand and a bit of a jiggle. To put the selectors back on, I used Sharpie pen marks to remind me which went where and to serve anyone who comes in after me to know this wasn’t its first transmission rodeo.
Bolting up went well, but a suggestion from Alistair about the bleed pipe made me nervous. After carefully checking the instruction on which clip was to be in what position, I gingerly pulled the pipe into the notched position, half expecting it to come away in my hand. It didn’t – a gentle bleed with my pressure bleeder clicked it back into position and a good pedal was achieved. Gearbox oil topped up, earth strap and sensors back in, I reflected that it can be nerve wracking having work observed, but I enjoyed the opportunity to train with Alistair. His OE technical experience was incredibly useful, giving me feedback and advice on the job.
Lessons learnt
In conclusion, the tooling on loan from Schaeffler was superior to what I had at my workshop. If I were to actively chase SAC work, I would commit to improving my fitment tooling in this area. I found the job satisfying on completion and talking to others who routinely complete this work, I wondered if I should consider it more? With regards to the DMF, would I measure another? It would be best practice; you have the information to give to the customer should there be any question.
However, my opinion remains: estimates should be worst case. I briefly worried if I had replaced DMFs previously that could have been an unnecessary expense. After much thought, I have decided I am comfortable with my insistence on replacing the DMF; my new measuring skills from Alistair will give me sufficient information for an informed decision if none were available. The emergence of an ‘all-in-one-box’ solution strongly suggests that I am not alone in my DMF thinking.