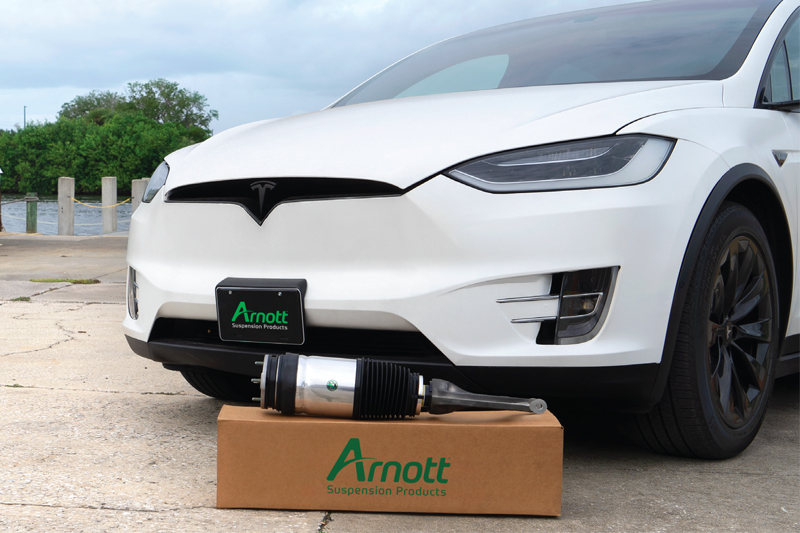
In this article, Arnott investigates the impact increased adoption of electric vehicles is having on air suspension technology.
The most obvious difference between a vehicle with an internal combustion engine and an electrical vehicle is that an ICE ignites and combusts fuel (spark-ignited for gasoline engines or compression-ignited for diesel engines) while an EV uses a battery powered electric motor for propulsion. This difference in powertrain impacts the vehicle in several areas, for example there are fewer moving parts in an EV because of the electric motor, with no exhaust pipe or DPF for example.
Although EVs are generally heavier and have a lower point of gravity than ICE vehicles, the suspension system of EVs did not undergo dramatic changes. In reality, the conventional coil strut and spring/shock absorber set-up, or air suspension set-up (whether or not accompanied with adaptive damping technology) looks very similar to the set-up used in ICE vehicles. Nevertheless, different set-ups and technologies are still platform-specific meaning shocks are tuned to optimise for trim level, have different damping curves/shock settings, etc. just like ICE vehicles.
From a practical standpoint, due to the similar suspension set up, a mechanic can repair and replace suspension system components of an EV as easily as on an ICE vehicle. No additional EV specific special tools or training are required since the suspension is not part of the high voltage system.
EV specific suspension
One of the unique characteristics of electric vehicles is their increased weight and alternative weight distribution within the vehicle caused by battery packs, the position of the traction motors, etc.
Air suspension technologies have commonly been used in ICE vehicles to combat load differences and to optimise the ride and handling in varying driving conditions. The air suspension’s autoleveling capability is the reason why manufacturers design their EVs with air suspension to obtain the desired ride and handling features while maintaining a high level of comfort for the occupants.
A second challenge for EVs is the travel range, which is affected by the amount of electricity the battery can store and how efficiently it is used. Some factors that have influence on the range are the driving conditions and ambient temperature, eco/sporty driving style, use of electronic systems such as the air conditioning or heating, the total vehicle weight (including the occupants and additional cargo) and the drag. To maximise the travel range capacity, EV manufacturers opt for air suspension because it can contribute to lower fuel consumption. Air suspension can lower the vehicle body at high speeds. This decreases the drag coefficient of the vehicle thereby potentially increasing the travel range.
With the increase in electrification of the car park, we will most likely also see an increase in the use of air suspension systems as the EV market takes advantage of the beneficial characteristics of these systems.
For Arnott’s team of engineers, developing suspension for EVs is a natural evolution from what they have been doing for decades. With an Arnott-owned test lab, test track and fleet, the engineering and prototype teams can take an idea from a white board to a complete concept, producing prototypes and being able to drive those prototypes on the vehicle. Each design is then independently evaluated by other engineers who will do a similar, independent ride evaluation. This feedback loop continues until what they deem the “perfect ride” is accomplished. This proven track-record in engineering, designing, and manufacturing air and suspension aftermarket components is now extending into reliable and long-lasting suspension solutions for EVs.