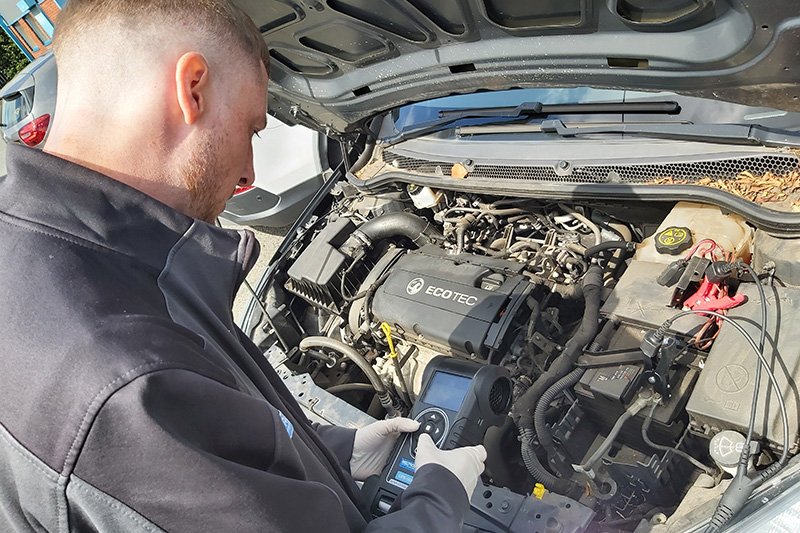
Rotronics’ Managing Director Ken Clark takes a look at battery testing in the workshops of tomorrow.
Futureproofing technology in a modern workshop is essential, and that is just as important when looking after batteries as any other component in a vehicle. If we consider how we use batteries now and how that has changed over the years, there are increased demands and loads, so the way we test, charge and maintain them has to step up a notch. The demands on batteries have increased due to more sophisticated power hungry “standard in-vehicle systems”, such as navigation, heated seats, windows, steering wheels, entertainment and start/stop technology. Whilst the increased use of AGM and EFB technologies has improved battery performance, batteries have not doubled in size to cope with double the work, battery maintenance remains an essential requirement in minimising risk of premature failure.
Any modern workshop must know how to cope with maintaining batteries in combustion engines, EV and hybrid technologies and the single most continuous component in these varied formats is the 12 V battery. Having the battery management technology to be able to test and charge accurately is key to maintaining vehicles at their optimal level.
The latest generation testing technology available to support these technologies, measure not only the cranking ability of a vehicle battery, but more importantly the RC (Reserve Capacity). This process is known as conductance profiling and is an essential component enabling greater accuracy supporting modern day battery diagnosis.
The modern workshop will require the most efficient wireless-enabled kit, offering state of the art conductance profiling and charge acceptance testing, enabling updates to take place remotely. All of which lead to a more accurate test decision for modern start/stop vehicles. It is no longer acceptable to just do the cranking amp analysis, we also need to understand the consumer loads.
CPX900
The CPX900 conductance profiling battery and system analyser allows workshops to provide live information to their customers and email test results, which assists in deciding on the best course of action for the battery. The CPX900 offers a comprehensive health inspection, and this assesses the reserve capacity available in the battery and its cranking ability. For workshops frequently conducting inspections, MOTs and servicing, this is ideal technology as Wi-Fi and Bluetooth connectivity is standard. Any software updates are wireless, and it can be fully connected to the Rotronics subscription-based ROBIS portal.
DCA8000
The DCA8000 can analyse most batteries within two minutes and once the initial test is complete, the charge time will be inside the range of any expected service time. This is excellent in terms of workshop planning as it provides an approximate charging time to assist in productivity. Like the CPX900 it has automated software updates and data analytics. The DCA8000 suitable for all 12 V suitable for 12 V battery charging including lithium, along with a 70 A battery support capability.
With the speeding up of electrification, the 12 V battery remains just as important as ever before as it is used for loading up consumer components, and there is no CCA requirement on an electric vehicle.
We are all dealing with and reading about vast amounts of data every day and it is important that your workshop battery management technology helps to give a birds’ eye view into your team’s continuity of testing – or lack of continuity. The CPX900 can seamlessly integrate into the Rotronics ROBIS online portal to see if technicians are testing correctly, and if they are entering the correct information about the battery type. The information input is essential and can assist in identifying training needs in the workshop. Through the work that Rotronics does with customers and from the bank of 4.6 million tests to date, we know that 20% of tests that are carried out have wrong information entered. The CCA of the battery or the type of battery are continually mis-entered, and this leads to misdiagnosis and potentially inappropriate corrective actions.
ROBIS is a bit like a new problem-solving team member or technician who has responsibility for achieving optimal battery performance and has the road map to guarantee that your customers’ vehicles start first time. ROBIS helps put in place consistent battery management quality standards and workshop practices. The industry-first system acts as a remote technician, working in partnership with your team and a much-needed resource; your lowest cost digital analyst and technician who is working for you 24/7 365 days a year.