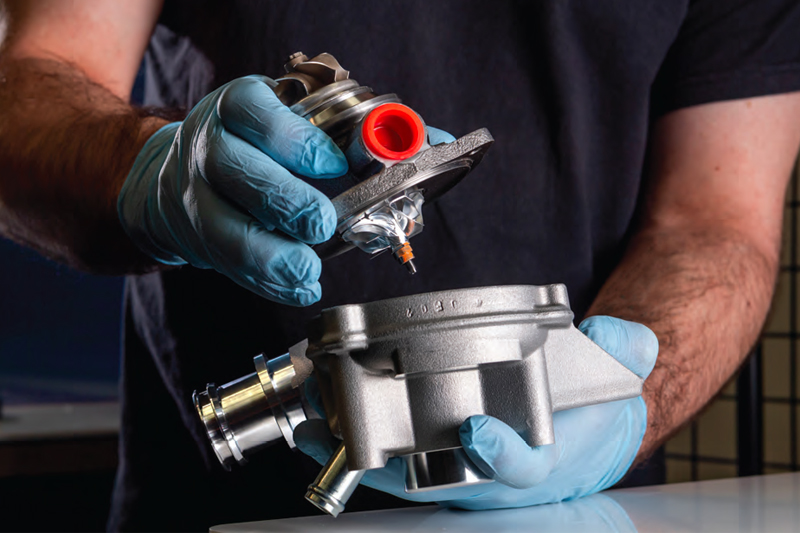
Remanufactured turbos offer workshops an ideal solution to provide customers who are still feeling the pinch, at least so says Melett.
There is no better time to offer a remanufactured turbocharger to customers as the current economic climate has led to a perfect storm for vehicle owners. From a customer viewpoint, remanufactured products using high-quality components can be considered the same as a new product, providing a more attractively priced alternative to the original.
Turbocharger remanufacturing is increasing in popularity within the aftermarket, as an original equipment turbo can often be very expensive to replace. Remanufacturing preserves as much of the material in the original product as possible, therefore using less raw materials than in the manufacture of new products.
Remanufacturing involves vehicle parts being rebuilt to a standard equal to, or greater than, the original manufacturer specification. At times, aftermarket design improvements mean that remanufactured parts often outperform the original equipment originals, as any design defects can be engineered out. The process ensures that the original design and quality specifications are all met, so technicians and end users can be confident in the quality of the remanufactured vehicle part they receive.
Preconceptions of quality
In the past, low-quality components from unreputable suppliers have been used in the remanufacture of turbochargers, which has created preconceptions about the reliability of remanufactured parts. However, this opinion about remanufacturing has changed significantly in recent years.
A professional turbo repairer will carry out pre-production checks of all old units to ensure that only the best quality turbo core is selected for remanufacturing. All parts are inspected for damage and wear. Any worn or damaged parts will be replaced. The core assembly is balanced and only when a unit passes the final balancing tests is it deemed ready for final assembly. Tom Wright, group product manager at Melett, said: “The entire UK economy is being gripped by the cost-of-living crisis, and the garage and automotive sector is no exception. With service providers and customers concerned about spending, it’s important to consider the benefits in cost offered by remanufactured components, with significant reductions in price when compared to original equipment products.
“Cost savings aside, we’re reminding the industry that there’s no compromise on safety and part quality. The use of highquality components in remanufacture ensures a long-term, sustainable approach on vehicle repair and servicing.”
Automotive Parts Remanufacturers Association (APRA) Europe recently reported that remanufacturing saves millions of tons of carbon equivalent emissions, 85 per cent of raw materials and 55 per cent of energy compared with new production, meaning remanufacturing is sustainable and resource friendly.
“Remanufacturing provides additional benefits on a wider scale, with the environment benefitting from carbon savings and reduced emissions from not having to extract raw materials in the manufacturing process of a new turbocharger,” Wright added.