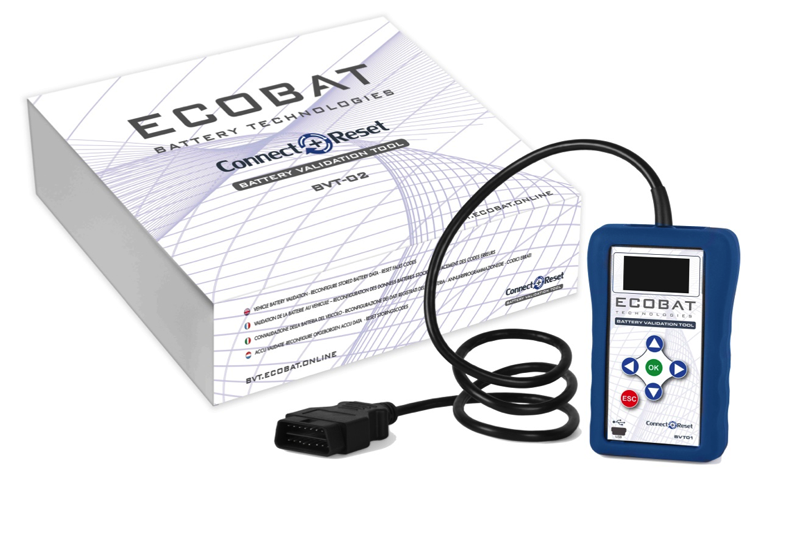
The most common cause of vehicle breakdown across Europe remains battery-related, says Ecobat.
Providing ‘traditional’ SLI (starter/lights/ignition) batteries are maintained properly – charged regularly and kept from excessive discharge – they are a remarkably reliable source of power until they need to be replaced at the end of their natural service life. As replacing them is a simple job for the technician, there is no great profit potential for the workshop.
However, as vehicle development continues, aligned with increasing political pressure for more environmentally friendly cars, most SLI batteries will disappear, as manufacturers have turned to a more appropriate battery that meets the demands of the new technology. To address the developmental and environmental issues, the most common solution is start/stop technology, which in turn has driven the development of AGM (absorbent glass mat) car batteries. First developed in the 1980s for use within the military, the charge and discharge characteristics of AGM batteries are ideal for start/stop vehicles, due to their design and efficiency.
In addition, AGM batteries provide a number of other advantages over their SLI cousins, such as increased performance, durability and lifespan, as they are designed to make at least 350,000 starts, compared to 30,000 from a SLI battery. However, because most drivers tend to deactivate the start/stop system, they are only making the number of starts the SLI battery is designed to make and are subsequently lasting significantly longer than was expected.
As a result, AGM batteries still do not feature greatly in the marketplace, despite the fact that most cars now use them. Therefore, there is a danger that technicians and workshops could be unprepared and lacking the correct understanding and tools needed to communicate with these potentially complex AGM battery systems. Nevertheless, by the end of the year, 12% of battery replacements will be AGM, and by 2020, it is expected that this will increase to a fifth.
Ecobat Battery Technologies (EBT) says it is on hand to provide the right tools workshops need to test, diagnose, find and crucially install AGM batteries. Whenever a vehicle enters the workshop, there is an opportunity to test the battery and establish what the next point of action should be. A battery testing tool is an essential aid for workshops as it can provide accurate readings, without the need to remove the battery.
The device also tells the condition of both AGM and SLI batteries, meaning that technicians can determine the battery’s state of charge, starting capacity, electrical consumption and charging voltage, so that they can assess the health of the battery and, if necessary, apply the precise charging regime to keep it in the best possible condition.
Should an AGM battery need replacing, technicians can turn to another tool that will allow them to install the battery with confidence. The battery validation tool (BVT) follows a ‘connect and reset’ process through a simple sixbutton/LED graphics display, meaning they can view the order to validate the replacement. When connected, the BVT will go through the reset procedure to correctly introduce and integrate the battery into the vehicle’s electronic systems.
Without the use of a BVT, technicians cannot validate the battery properly and failure to do so can cause issues with the start/stop system, leading to the shutdown of some electrical systems and the premature failure of the replacement, because the system has not recognised the battery as it should have done.
In addition, as the installation of an AGM battery is a potentially time consuming job, it also becomes significantly more profitable for the workshop. Therefore, it is more important than ever for technicians to understand how AGM batteries function and how they can be maintained/replaced. In doing so, workshops will be investing in the future and be able to stay ahead of the game.