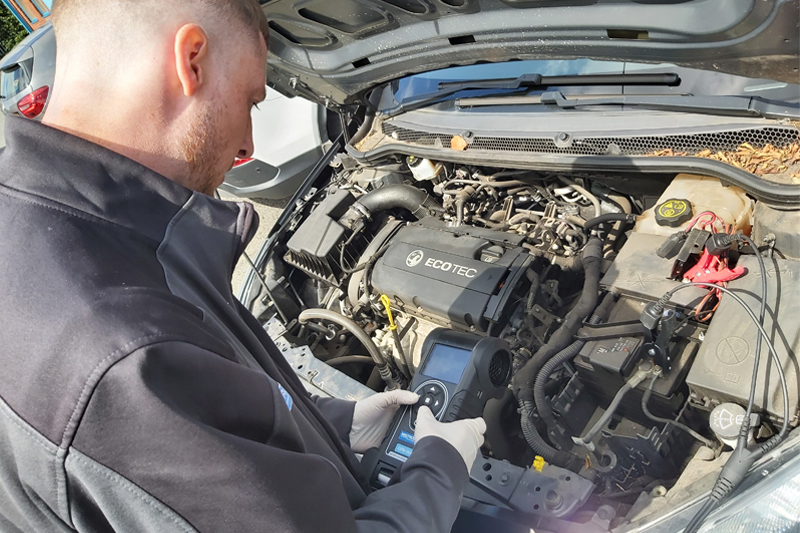
Most of a vehicle’s vital organs are thoroughly checked during a routine service, but we keep seeing evidence that the battery, the beating heart, is frequently neglected. Rotronics investigates how adding battery checks to a routine service could bring revenue to your workshop.
It seems illogical to check every inch of a vehicle and not the battery. The brake pads, the tyres and the exhaust may be in perfect condition, but the car won’t leave the forecourt or get off the drive for very long if the battery fails. We asked Ken Clark from Rotronics for advice to readers, to help demonstrate how including regular battery test and charge checks will make any workshop more professional and profitable.
Speaking from experience
Ken can talk from personal experience about the importance of routine battery testing and charging. His own family vehicle’s battery was left in very poor condition following a workshop visit for an inspection due to flashing warning lights. After the inspection, his vehicle was up and running again but the battery was at a very low voltage because the engine had been running for four hours in repair.
Ken Clark, managing director at Rotronics, explained: “After several hours of tests, I received all the results in a report that included a fantastic video. I was told in the video about the condition of every corner of the vehicle. Except for one essential piece of information: the health of the battery – which was not talked about once in the report.
“When I got back to Rotronics HQ, the vehicle was tested and charged with the Midtronics DCA8000 and I discovered that the battery was significantly discharged. If I hadn’t known what to do and been alert to the battery issues, the battery would have failed speedily. So, it wouldn’t matter that everything else on the car was working, I would have needed roadside recovery.”
Ken has provided a simple guide for technicians to avoid this situation for their own customers. To make sure that your customers’ batteries are not in a worse state when they leave your workshop, add the following to your own workshop service and repair processes:
- Make it mandatory to test and charge all vehicles.
- Charge for Charging: that means that every vehicle that comes into your workshop should have a battery test and charge according to the results.
- You can do the maths on charging £5-£10 per test and charge.
- It takes under a minute to test a battery.
- Don’t miss out on replacement revenue opportunities for batteries that are at the end of their lives.
- If the battery is going to fail anyway, it’s better that you provide a replacement in your workshop setting than the customer sitting at the side of the road.
Such a big deal?
Just how extensive is this issue of ignoring the battery? Ken and the team surveyed visitors to Mechanex 2022 and discovered that just under 60 per cent say that they test every vehicle, meaning over 40 per cent are ignored. Those batteries are at risk of being defective and the technicians have missed a golden opportunity to sell a new battery. However, when probed further, 74 per cent admitted they would only use a battery charger if the vehicle would not start, so Ken feels that the 60 per cent number is optimistic.
The Rotronics team are the creators of ROBIS which provides easy-to-access battery reports via an online dashboard and reporting system from battery data that has been collected from national/regional workshops. This works in conjunction with the EXP1000FHD.
Through analysing 12-months’ 2022 ROBIS data, covering five independent, single-site workshops, the Rotronics team could see that of the tests conducted, only 24 per cent of the vehicles had batteries that could be considered “good”. 37 per cent of the batteries needed to be “charged” and 39 per cent needed to be “replaced”.
Three quarters of all batteries tested needed attention and would have caused the customer to have a roadside breakdown if not charged or replaced.
Recouping the costs
The Rotronics team, armed with data, have been working with a number of nationwide, multi-site workshops, to help get them on board with charging appropriately after a test.
Ken Clark says: “We keep discovering large site workshops who will battery test, to tick a process box, but then won’t charge appropriately. They may as well not bother because it’s the appropriate charging that really makes the difference to the long-term health of a battery.
“We recommend using the DCA8000 for appropriate testing and charging because it’s a plug-in-and-leave option which will show you what the test recommended and how the battery has been charged – without you lifting a finger. The results can be printed out or emailed to your customers, so that you have a foolproof method of validation.”
In a time when the cost of living is top of everybody’s mind and workshop budgets are being fiercely protected, Charge for Charging makes real sense, when it is coupled with providing excellent customer service. It could also give you a tangible point of difference to other workshops in the eyes of your customers.