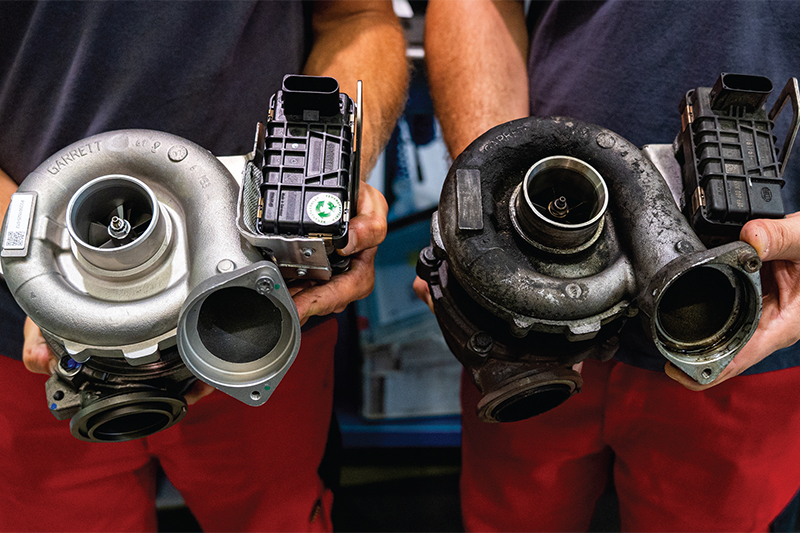
PMM ’s editor Kieran Nee asked three remanufacturers to share their knowledge and expertise to highlight the benefits and challenges of the remanufacturing process.
For any of our readers unfamiliar with the remanufacturing process, Shaftec’s marketing manager Adrian Kitchen outlines the four steps that go into each remanufactured product: inspection, disassembly & cleaning, reassembly and testing. Before all else, “every single part is checked and its fate determined by either being fit for remanufacturing or being damaged and unfit for remanufacturing. The part is then stripped bare ready for cleaning/de-greasing. As soon as the parts are clean, they are shot blasted. Now the components are organised onto part specific trolleys and handed over to our team of professional builders who assemble the part using new components. Every single part that flows through this department is tested using purpose-built machinery.”
So what advantages, exactly, can this process bring to the aftermarket? Remanufacturing’s OE credentials are something that the three companies I spoke to all emphasised. Autoelectro’s UK sales manager, Nick Hood pointed out that “because the original OE body remains, mechanics can rely on an accurate fit” and cited the importance of technical knowledge: “Understanding how a part, like a starter motor or alternator, operates and why it fails is invaluable; it enables us to support a workshop with technical information that it wouldn’t otherwise receive from a spurious source that imports new units.” Borg Automotive argues that remanufacturers can even go one better than OE, claiming “we can adjust part numbers which are “born” with faults.”
The nature of remanufactured products, with the “core” of the product coming not from a factory but from the car parc itself, means that whatever cars are still on the road are, in theory, able to replenish the stock of products available. This method of sourcing stock from existing cars makes it more reactive to what is needed. As Borg points out, “in some cases, remanufactured parts may be the only option for older or hard-to-find vehicles, as new parts may no longer be available. This is a big help to drivers of older cars who struggle to find replacement parts.
Of course, one of the biggest benefits of remanufacturing is its low environmental impact. According to Borg: “Remanufacturing helps to conserve resources by giving used products more than one life. This reduces the need to extract and process raw materials, which can be energy-intensive and environmentally damaging. A study shows that remanufacturing on average saves 96 per cent of the raw materials used in manufacturing the original automotive part.” Shaftec’s Adrian adds: “As an individual company we aren’t making a significant dent in the reduction of greenhouse gases but our contribution along with all the other remanufacturers out there does help to make a sizeable impact on a more environmentally friendly way of producing parts.”
So far, so good. But as you might imagine, receiving core from existing cars and transforming it into OE-quality components is not without its difficulties. Autoelectro’s Nick Hood details some of the challenges they face: “A general reluctance to return old core. This is heightened by the introduction of units that are surcharge free. There are more vehicle-specific units these days too; there aren’t many instances where one reference fits different applications. What’s more, the economy of scale on purchasing is not what it was. Remanufacturing a part on the periphery of a range results in buying a limited number of components; therefore, it becomes more expensive to remanufacture that part.”
Not all parts are appropriate for remanufacture, according to Borg – the following should not be remanufactured: “Parts that are severely damaged or worn, parts that have reached the end of their service life, parts with safety-critical functions, parts that have been recalled and wear parts.”
To conclude, I asked what advice can be given to any workshops considering buying remanufactured parts. Autoelectro emphasised the quality aspect of it: “Remanufacturing is an unusual concept in some ways; in normal circumstances, offer someone a product that’s brand new or remanufactured, I think most people’s disposition would be to choose new because it’s perceived to be better – and this is where the quality argument falls within the aftermarket. Just because a part is brand new in the aftermarket doesn’t mean it’s the same quality as OE.”
Borg urged workshops “it is important to research the supplier of the parts to ensure that they are reputable and have a track record of producing high-quality products.” Meanwhile, Shaftec finished by clearing up a myth about the area: “A lot of people label remanufactured parts as “reconditioned”. We are completely stripping parts back with sophisticated machinery and replacing the components that actually fail. We do not re- manufacture Chinese units, only OE parts.
Special thanks to Autoelectro, Shaftec and BORG Automotive for their participation.