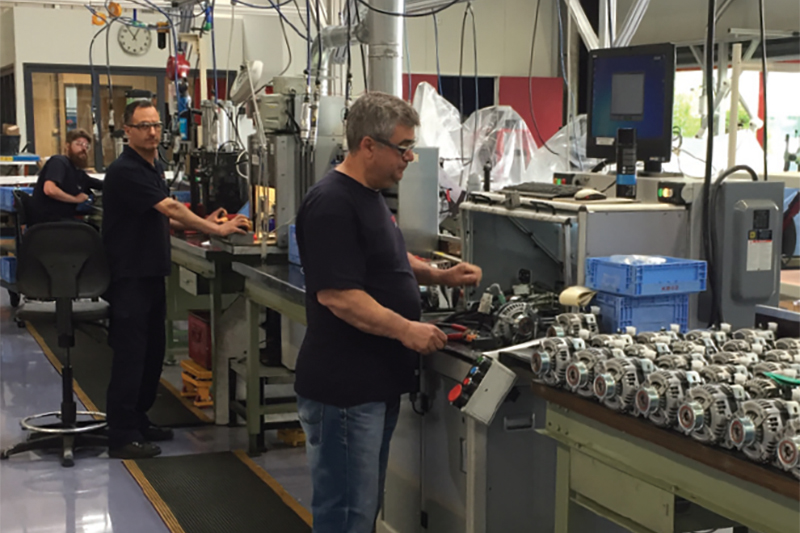
Andre Koppenhol, the manager of Denso’s remanufacturing team, discusses the benefits of remanufacturing and shines a light on a less well-known aspect of the business.
Denso is widely recognised as one of the world’s largest original equipment component manufacturers and system suppliers, with an extensive aftermarket portfolio. Our remanufacturing programme however, is less well known, despite being active in the European market for more than 10 years.
The reasons behind having a remanufacturing programme at Denso are actually threefold: to deliver high quality products of the same standards as the original component on the vehicle, but manufactured in an environmentally friendly and sustainable way.
Today, if a product like a starter or alternator fails, or the battery in their hybrid vehicle breaks down, European motorists have a choice as to whether they replace it with a brand-new unit or a remanufactured one.
Each of these components is the same in terms of quality, in fact in some circumstances, such as when it’s rebuilt according to the latest OE standards compared to a new unit of a four-year-old design, you could even say it’s better. So, the choice for the driver is whether they prefer a remanufactured unit that is more environmentally friendly and cheaper to purchase, or a completely new one.
Remanufacture vs repair
An example of a repair, would be if there was a problem with a solenoid on a starter, which could simply be replaced and the fault rectified. In contrast, remanufacture is when the unit is completely disassembled and every component is cleaned, examined, tested and recycled, or if necessary, replaced. It is then rebuilt and tested against the standard of the original unit, so that as far as its performance and reliability is concerned, it will become, in effect, a new unit.
However, a distinction needs to be made when it comes to diesel components such as injectors, which due to their complexity cannot be repaired in the sense of replacing just one small part, they have to be completely remanufactured.
To shine a light on the process, let’s take diesel pumps and injectors as an example. There are two sides to remanufacturing these products. The first is the remanufacture of diesel injectors carried out by us in our own facilities, which is an operation only for our vehicle manufacturer partners and their dealer networks. The second consists of diesel parts remanufactured through our service repair network, a service offered to both VM dealers and the independent aftermarket.
This network is made up of independent diesel specialists based throughout Europe, who are trained and authorised by us to execute diagnostics, service and repair to our standards. This means they are able to remanufacture these components to the same OE standards, the only meaningful difference being that they are more limited in their production capacity compared to our mass production-focused facilities.
Service repair network
It’s worth adding that the service repair network is an important part of Denso’s service and repair solution for both the independent aftermarket and the VM’s dealer networks. It provides them with a comprehensive diesel support package that means that any diesel fault can be diagnosed and repaired by a true specialist, with an extremely high level of competence. The network therefore follows our QCD (quality, cost and delivery) principle, which means that an end-user can simply walk in with a problem and leave with a high quality, low cost and quick delivery solution.
A remanufactured component needs to be completely dismantled and cleaned and any substandard parts replaced with original parts, so the real question is “Is the process really any more environmentally friendly than manufacturing a completely new unit?” In short, yes, it is! Our philosophy is to reuse as much as possible and in the case of alternators this is usually around 85 per cent and with batteries it’s close to 90 per cent. This automatically provides great environmental gains, but there are also considerable CO2 reductions in not having to produce every part from scratch. So, the process is considerably more environmentally friendly.