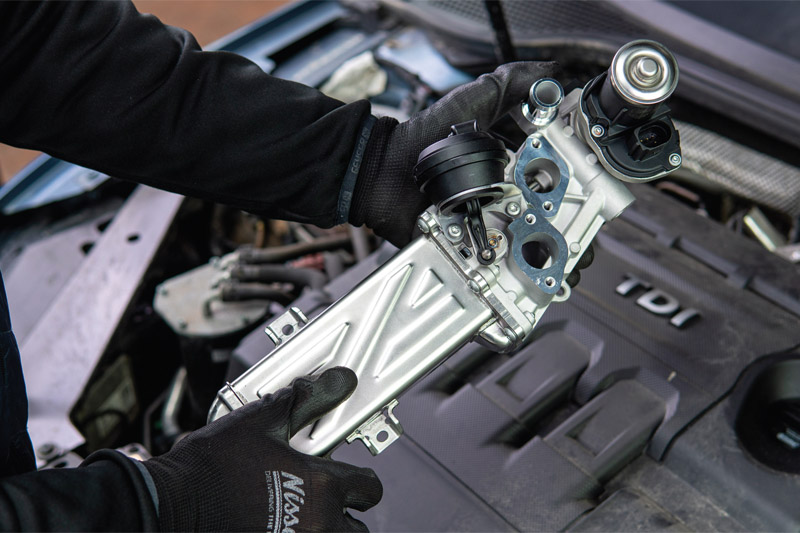
PMM looks into how the Nissens technical team tackles EGR valve problems on prominent TDI applications.
The exhaust gas recirculation (EGR) valve is an integral part of a vehicle’s exhaust emission control system, influencing the operation of the engine and its combustion process. Failure, malfunction or removal of the EGR valve will cause the engine not to operate properly. Furthermore, valve failure can provoke faults in the exhaust emission control and cause severe failures of related devices such as the diesel particulate filter, catalytic converter or turbocharger. In addition, impaired performance of the vehicle’s exhaust emission system will seriously affect the environment and may breach regulated emissions levels.
Common signs of EGR valve malfunction
- Engine check control lighting on the dashboard
- ECU setting the engine into limp mode
- Reduced engine power
- Significant changes in fuel consumption
- Engine emitting pinging and knocking sounds
- Rough, uneven idling
- Stalling and hesitation during acceleration
- Exhaust gases escaping within the engine compartment
Safety
By their very nature, EGR valves are generally located in the engine compartment and close to heat-generating components, so they can get very hot. Technicians should therefore be mindful of the danger before starting diagnostic and replacement procedures and make sure the vehicle has cooled down to a safe temperature before undertaking the work.
The problem
The EGR valve used in multiple VAG diesel applications utilising the 1.4, 1.6 and 2.0L TDI units can be particularly problematic, as it is especially susceptible to heat and vibration, as well as excessive engine load. Naturally, the faulty valve has to be replaced because its failure will impair the function of the entire exhaust emissions system, so affecting the engine’s proper operation. However, as the issues are largely due to the design of the original part, workshops must be aware that these malfunctions can occur both in the original, and a replacement part.
Fortunately, the Nissens Efficiency & Emissions division has stepped in to provide a solution to the problem by addressing the issues that contribute to the valve’s premature failure and ensuring its proper function and long lifespan, despite exposure to the harsh working conditions it has to deal with.
By applying several design improvements over the original and proving them over a series of comprehensive tests, the team has developed a durable replacement part that performs to the standards defined by the vehicle manufacturer and therefore provides the aftermarket with a competitive, quality solution.
The Nissens solution
Gearbox design – Recognising the problems associated with heat and lubrication, the Nissens team significantly reduced tolerance and therefore friction, by applying specific PTFE, high-temperature resistant grease. Furthermore, the plastic material of the gear wheels in the two-stage gearbox has been upgraded.
Improved design of the valve stem – To avoid the known, severe malfunction of the valve caused by the engine load and vibrations, Nissens improved the valve’s stem and lever arm fixings by applying a unique design of spiral pin.
DC-motor design upgrade – The motor’s bearing system has also been improved to ensure its flawless operation and long service life, despite the vibrations and frequent temperature changes it has to deal with.