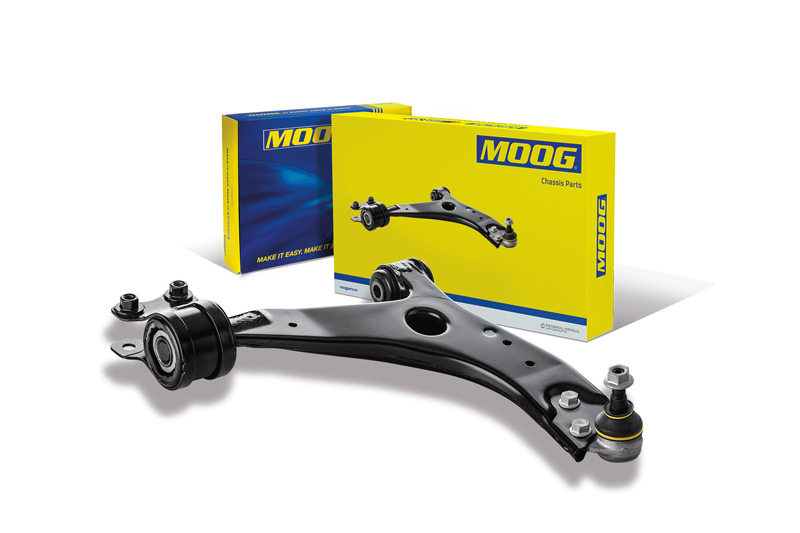
Moog takes a look at fitting steering and suspension parts with help from its expert support team, the Garage Gurus.
Starting off with advice for when you’re refitting suspension arms or replacing ball-joints. After refitting suspension arms, avoid tightening the bush bolts while the vehicle is still hanging. This will create a ‘pre-stressed’ condition which will lead to extremely premature wear of the track control arm bushes. To avoid initial over-tightening, limit the first torque to a value which allows the bush inner tube to rotate within its seat while the vehicle is progressively recovering its neutral position. Once the vehicle is fully grounded the final torque value can then be applied.
To avoid thread damage or worse, don’t use a torque gun when tightening the ball joint nuts. A torque wrench allows for more precision and control. The company also recommends not re-using the old clamping bolt as it could be damaged or bent and to always use a new clamping bolt.
Often accidental damage is caused to the ball joint dust boot with the tool used to fit the ball pin into the wheel knuckle so take care to avoid this. Also, avoid pinching the ball joint dust boot when pressing in the ball joint. Finally, remember, always carry out a proper wheel alignment.
When replacing bushes to new suspension arms
Always use specialised tools for extracting the old or installing the new bushes as not doing so is likely to lead to trouble. Also, avoid pressing the bushes at the wrong contact point. It is important to press the outer tube of the bush, pressing the inner tube or the rubber is likely to damage the bush.
Avoid incorrect bush orientation. As it is crucial that the bush is aligned at the correct angle to ensure correct performance. Lastly, make sure the bush is pressed in straight.
When to renew the entire suspension arm
Moog recommends the replacement of individual bushes and/or pressed ball joints only once, the next replacement should be a fully assembled arm.
Recurrent replacements of bushes (or ball joints using pressed technology) can significantly alter the shape and dimensions of the bore. Deformation can arise through successive extraction and pressing operations, usually resulting in an enlarged bore diameter which in turn means the bush or ball joint will not be securely housed. This is especially the case when the arm body material is sheet steel.
A full suspension arm replacement should also be undertaken if there is excessive corrosion on the arm body. Finally, some suspension arms simply don’t allow the replacement of individual ball joints, so that even if an individual bush replacement is possible, any excessive clearance appearing at ball joint level can only be fixed by a replacement of a full assembled suspension arm.
Re-using fixings
The company recommends always using new fitting accessories/hardware in place of those dismantled. Safety-critical bolts, nuts, washers etc. are supplied with Moog parts to match vehicle manufacturers standard metal grades and in many cases, exceeding OEM parts in terms of coatings.
To maintain safety and make fitment more efficient, its suspension arms have all parts pre-fitted, for example, ball joints are already bolted to the correct tightening torque.
Replace in pairs
Always replace suspension arms, flexible axle mounts, ball-joints etc. in pairs. In normal service both sides of the axle will have a similar wear rate, therefore it is appropriate to replace components at the same time.
In the case of uneven wear or damage, it is important to identify the underlying cause and address the issue appropriately before replacement. In such cases it is still best practise to replace for both sides of the axle. Firstly, this allows for a one-shot wheel alignment and secondly, it ensures there is no issue with vehicle behaviour. Consistency and balanced performance could be compromised if there is any difference in part design, either through supersession or manufacturer variation. It could also lead to problems during an MOT inspection.
The overriding message is to always choose reliable, durable and easy to fit parts as this can reduce a whole host of problems right from the outset. Look for add-on benefits like zinc flake coating on accessories and flanged nuts which enhance locking force and raise corrosion resistance. Suppliers such as Moog, include synthetic grease that enables easier fitting of ball joints and use TPU dust boots which provide better protection against water and contaminants than traditional chloroprene dust boots. It’s hybrid core technology also provides durability benefits through double stud strength and a carbon fibre bearing which reduces the amount of play that evolves in service.