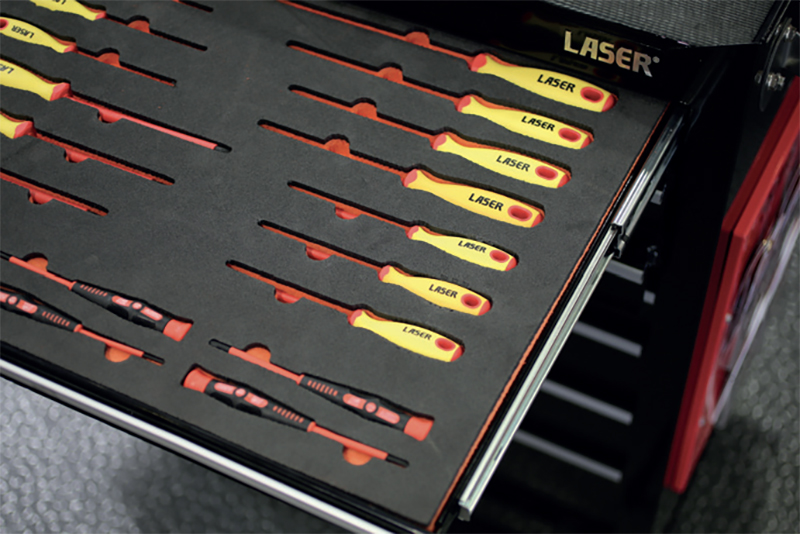
Laser Tools guides the PMM audience through some of the essential gear for running an EV-ready workshop.
Hybrid and BEV (battery electric vehicles) commonly operate with voltages typically from 300 V DC to 900 V DC – anything beyond 60 V DC is classed by health and safety as ‘high-risk’ and can cause serious injury or even fatalities. When Laser Tools considers these workshop safety concerns, it is important to look at the whole picture and subdivide ‘hybrid and BEV safety’ into four separate categories:
- Workshop safety
- Vehicle safety
- Personal safety
- High voltage tools and test equipment
Workshop Safety is about making the working environment safe – for employees, but also for members of the public/customers who may be around vehicles in the workshop. It’s important that there should be a designated area cordoned off and identified as a “Danger: High Voltage” area, with appropriate barriers and signage. It is also important that high-voltage rescue and first-aid equipment be available in case of emergency.
Vehicle safety is about making the vehicle safe for a technician to work on. PHEVs (Plug-in Electric Vehicles) and BEVs will normally have some form of isolator switch, commonly known as an MSD (manual service disconnect) switch, which should be removed before any work is carried out on the vehicle. This has the effect of isolating the high voltage battery from the rest of the vehicle. However, it’s important that other technicians in the workshop are aware that this is a high voltage vehicle, and do not attempt to start, or move the vehicle. Thus, appropriate identification, (for example, warning signage, lock-out tags & locks, etc) should be used.
Personal safety is about providing protection for the technician working on the vehicle – appropriate insulated gloves and face shield should be worn to protect against high voltage leaks and arc flash risk, along with appropriate insulated safety footwear, or insulated floor matting. If working within the high voltage battery and/or circuitry, further specialist protection, such as full arc-flash safety workwear to protect against arc flash burns risk, may also be necessary as the technician will now be working within a live high voltage environment.
High voltage tools and equipment – the electrical industry has specific standards for test equipment which is to be used in a high voltage environment. This is known as the CAT standard, a minimum of CAT III 600 V, or CAT IV 1,000 V is required to ensure the test tools are suitable and safe for working on high voltage systems. Hand tools are required to be fully tested and insulated to IEC 60900:2018 standards and carry the international symbols for high voltage tools. Typically, the tools required will include socket sets, wrenches, screwdrivers, pliers, torque tools and hex and torx keys – although most vehicle manufacturers will only use a limited selection of sizes of each.
Laser Tools has approached the subject on the basis of offering a “one-stop-shop” for workshop high voltage vehicle requirements, covering all aspects of workshop safety, vehicle safety, personal safety, and appropriate tools and equipment. In order to make it easier for the workshop owner to decide on basic requirements, Laser Tools has created a number of starter packs covering each of the above safety aspects.
The company has gained invaluable experience by working with vehicle manufacturers and importers on the requirements for their main dealer service workshops when working on high voltage vehicles. This includes both normal service functions and specialist high voltage work. This experience has allowed Laser Tools to create suitable packages for independent workshops, and to pass on the knowledge gained.