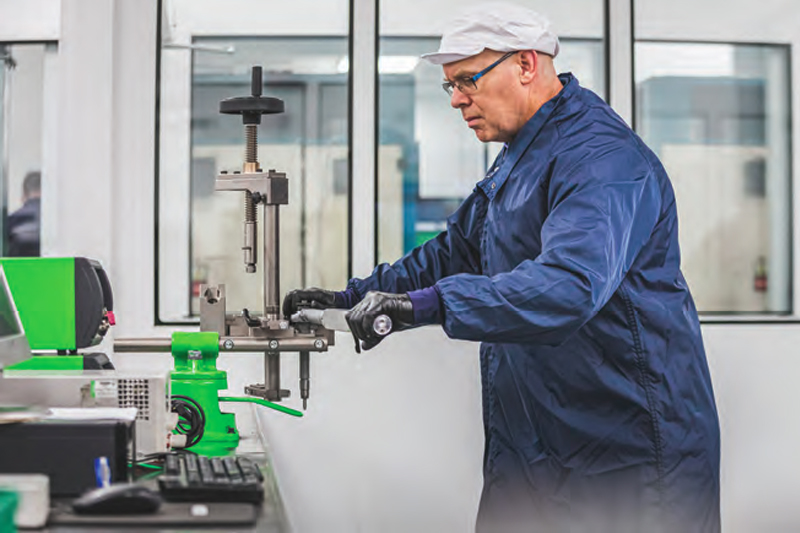
Carwood discusses the environmental benefits of remanufacturing, arguing that quality parts needn’t cost the earth.
Remanufacturer and technical service provider, Carwood has been exercising its inner wordsmith lately to enter a new phrase into the common tongue which perfectly, and succinctly, captures the harmony that remanufacturing brings to both the environment and to customers’ wallets – about time, we hear you say. Well, it was worth the wait: “Quality parts that don’t cost the Earth” is the new tagline the firm has borne unto the world and in PMM’s humble view it is just so.
We are big fans of remanufacturing at PMM: the sustainable practice returns used parts to a like new or, some say, better than new condition, all whilst protecting valuable resources, recovering waste and saving you money. What’s not to like?
As an OE-approved remanufacturer for, and a supplier to, some of the biggest names in the industry, Carwood has a proven track record of producing high-quality parts, that perform just as well, sometimes better, than the original. Whilst its full portfolio includes rotating electrics, electrical and electronics, engines, HVAC and electric rewind, its aftermarket range focuses on OE-approved fuel pumps, injectors, turbochargers and DPF cleaning.
Whether it’s for the likes of Jaguar Land Rover, Caterpillar or Perkins, the Ministry of Defence, a top-end factory-owned race team, a fleet or an independent workshop, every part it remanufactures goes through the same rigorous, multi-stage process – each one is systematically disassembled, cleaned and inspected, all wearable or out-of-spec components are replaced with like-for-like OE, before being reassembled and end-of-line tested to OE spec.
Take its common rail injectors as an example. With the latest generation injectors operating at pressures up to 30,000 psi, through clearances as small as 1 micron, even the smallest amount of dirt or contaminant, can cause the injector to seize and potentially fail. To prevent this, the company builds all its injectors, and pumps, in an ISO14644, Class 7 certified clean room, capable of filtering down to 0.5 microns.
It also performs hundreds of test steps, using the very latest OE test plan data, to calibrate each injector – a critical stage which allows the ECU to adjust fuel delivery and optimise engine performance when the injector is installed back into the vehicle. Without this, the injector simply has to guess how to perform.
The requirements for its remanufactured turbochargers are just as demanding. Every variable vane turbocharger, for example, is mounted and tested on either a turbo technics VTR (vane test rig) or G3 power rig, to ensure that the actuators and variable vanes are set and calibrated to OE specification for optimal performance when fitted to the vehicle.
Such is the level, that Carwood remanufacturing has been likened to the production of the original component – the only real difference being that it returns a used part to its original condition, instead of producing a brand new one.
It’s also why the company is certified to ISO 9001:2015, quality management, and ISO 14001:2015, environmental management standards, demonstrating the company’s unwavering commitment to provide products and services that meet, and even exceed, both customer, and regulatory requirements.
Stocking parts
Carwood is equally committed to ensuring it has the right, high-quality parts in stock too. Its wide-ranging lineup includes old and latemodel applications for car, van, truck, bus, agricultural, industrial, rail, marine, defence and motorsport. And together with its UK-wide network, it will ensure it gets them to you as quickly as possible.
Should you require it, Carwood also provides a range of technical support services including specialist diagnostics, repair and installation at its Coventry workshop and access to a technical hotline for best-practice advice on removal, refit, fault-finding and repair.
It’s only through its meticulous, OE-driven approach, that Carwood can offer a same-as, or even better-than-new product, with warranties to match. Yet because it reuses the core, it’s a fraction of the cost – typically at least 25 per cent cheaper than the OE. Meaning you can access a costeffective alternative to new, without compromising on either the quality of the product or your service.
Carwood parts don’t cost the Earth in the literal sense either. Through this process, the company is able to capture the materials and value added – labour, energy, and manufacturing processes – that were embodied in the original part during production, so that it can be used again, rather than being landfilled or recycled. In doing so, its remanufactured parts save up to 70 per cent of the resources versus new. And because much of the material already exists in its final form, and therefore not as much work is required to process it, it uses up to 85 per cent less energy and creates less greenhouse gas emissions too.
So by restoring used products, to, or better than, the OEM’s original specification, you can get proven-quality products, at a competitive price, and for an increasingly wide range of vehicles too. All whilst helping to conserve valuable resources and material. That’s exactly why Carwood describes it as “quality parts that don’t cost the Earth”.