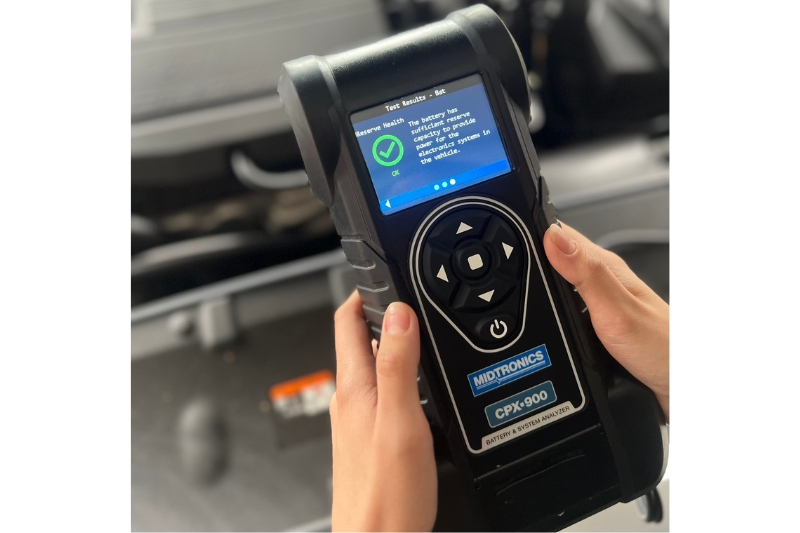
As cars continue to evolve rapidly, batteries are increasingly being recognised as the glue that holds everything together. Here, Rotronics gives an overview of how batteries have evolved to cope with increasing demands both from drivers and the manufacturers and explains how garages can capitalise on this change.
Lead-acid battery technology is 150 years old and still found in most vehicles on the road today. It’s gone through transformations over the years to increase stability and durability, which you see in batteries for today’s ICE vehicles. The first rechargeable battery for electric vehicles was invented by Thomas Edison in 1901 – a nickel-iron battery that could be charged twice as fast as a lead-acid battery. Of course, we know now that EVs were ahead of their time!
In the late 1990s, hybrid electric vehicles started gaining popularity with Toyota’s introduction of the Prius. This marked a significant development in the automotive industry, with manufacturers shifting their focus towards developing more efficient and sustainable vehicles.
Since then, EV battery technology has undergone several transformations to improve power output, energy density, and overall performance. The use of various lithium-ion battery chemistries has become commonplace due to their high power-to-weight ratio and longer lifespan compared to traditional leadacid batteries. More recently, manufacturers have started experimenting with solid-state batteries, which promise even higher energy density and faster charging times.
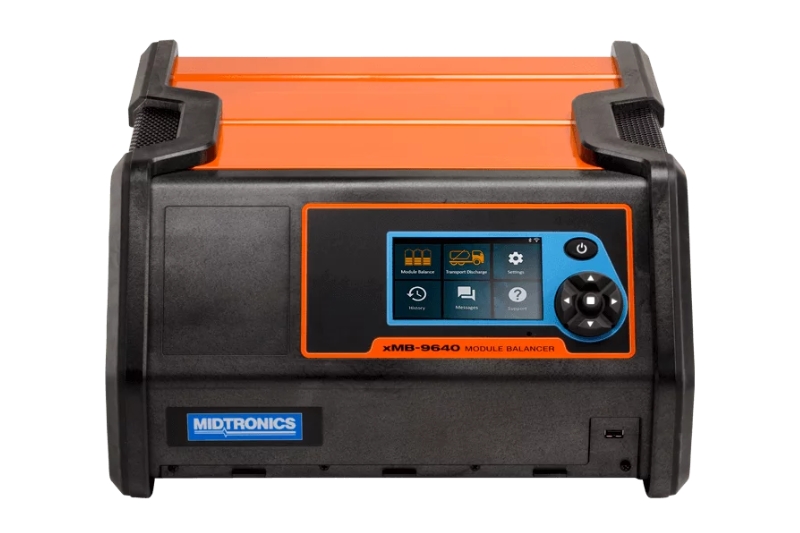
The evolving technology inside
At the core of every electric vehicle is battery technology. It’s a critical component that stores and supplies the electrical energy necessary to run EVs, hybrid cars and traditional ICE models. Lithium-ion batteries are the mainstream choice for today’s electric vehicles. Renowned for high energy density and longevity, they represent a vast improvement over their predecessors. They’re the prevalent choice for EVs today.
However, they are not without their shortcomings including issues of thermal management and resource scarcity. For these reasons, manufacturers are continuously developing new methods to improve their performance and address these concerns.
Solid-state batteries promise higher energy density, faster charging times and improved safety. Still in the development stage, once commercially viable they could revolutionise battery propulsion and manufacturers are watching developments closely.
Graphene-based batteries are another technology, offering potentially huge improvements in conductivity and charge rates. They use compounds of graphene and other materials in the cathodes of lithiumsulphur cells. This could see batteries charged in minutes rather than hours. This technology is also still in its early stages.
Don’t forget the 12V battery
While advanced batteries are generally associated with electric vehicles, innovations in traditional 12-volt car batteries are also ongoing. Enhanced flooded batteries (EFB) and absorbent glass mat (AGM) technologies have come to the forefront, offering greater durability and efficiency than standard lead-acid batteries.
EFB batteries are an evolution of the standard wet-flooded battery, designed to better support the stop-start technology commonly found in modern vehicles. This technology reduces the engine’s idle time, saving fuel and decreasing CO2 emissions, but it demands more from the battery. EFBs meet this need through improved charge acceptance and greater cyclic durability.
AGM batteries are known for their superior power and reliability. They feature a glass mat separator that holds the electrolyte solution between the battery plates, which allows the AGM battery to offer better electrical performance under high discharge and recharge cycles. AGM batteries are ideal for vehicles with heavy-load electrical demands and advanced power systems.
Some manufacturers are integrating lithium-ion batteries and new battery management systems to extend lifespan and performance. While these developments may not be as radical as those seen in EV batteries, they represent an important step in enhancing the functionality and efficiency of conventional automotive power systems.
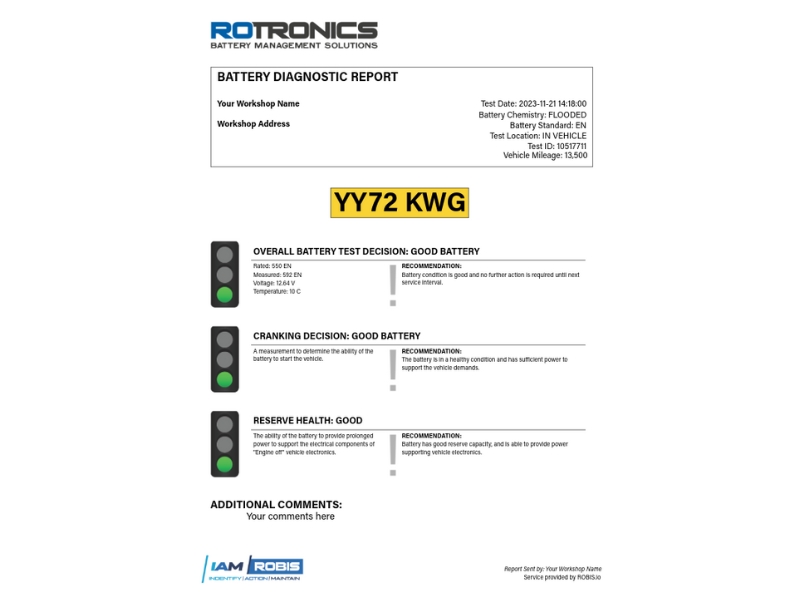
What this means for you
In the EV area Rotronics sees a growing opportunity for workshops – every EV vehicle has a traditional 12V battery onboard, which is critical to the vehicle’s operation – the same proportion of EVs have 12V battery-related breakdowns as do traditional ICE vehicles. Servicing the 12V battery is an excellent ‘bridge’ into wider EV servicing. The Midtronics CPX900ROBISP tester performs not only the traditional cold cranking test but also a reserve capacity (RC) test – which demonstrates the ability of the battery to run electrical systems. An RC test on a 12V battery on a customer’s EV will identify the health of that battery and if it requires charging or replacement.
The new Midtronics xMB9640 module balancer allows any workshop to diagnose and service EV and hybrid high voltage battery systems. High voltage packs are designed with smaller sections called modules that can be replaced individually, avoiding the expense of replacing a full battery pack. For the pack to operate as designed, the voltage for replacement modules need to be balanced. Designed specifically for aftermarket use, the xMB9640 allows individual cell modules to be replaced avoiding expense of an entire pack. It supports major EV and hybrid manufacturer brands and will allow workshops to offer a simplified and safe high voltage.
The 12V battery still offers the workshop huge business potential. ‘Best practice’ is to test every vehicle that comes in, not just those with battery related issues. This proactive approach allows early identification of problems before they become major issues. Customers appreciate this level of service, and it enhances the workshop reputation for reliability and thoroughness. The Midtronics CPX900ROBISP tests battery cranking health and also reserve capacity (RC) giving the technician a complete picture of battery health and recommended actions.
Crucially, the detailed printouts provided by the Midtronics CPX900ROBISP, and integration of test data within the Rotronics ROBIS online battery information portal. It delivers a comprehensive and accurate overview of the battery condition, supporting any workshop process. When customers see the clear report of their battery test supported with a quick ‘traffic light’ guide to the results of the criteria tested, they are more likely to understand the necessity of replacements or charging services. This builds trust and makes it easier for the workshop to explain the need for additional services.