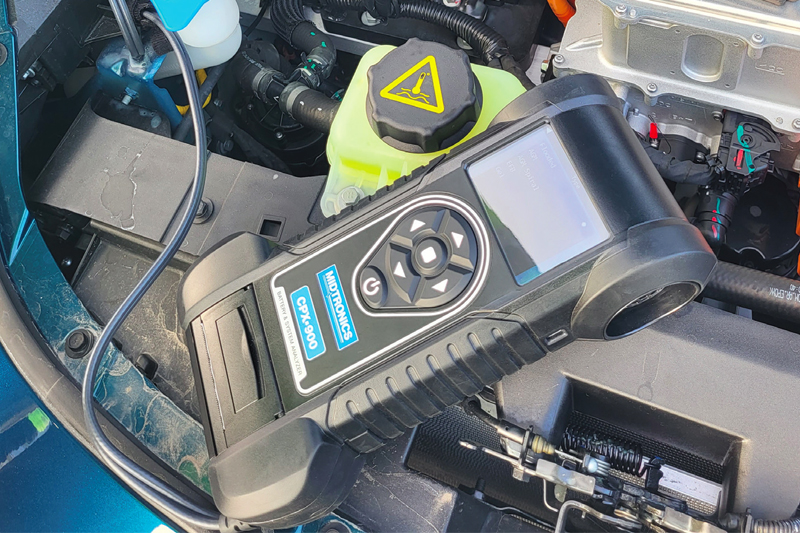
PMM asked Ken Clark, managing director of Rotronics Battery Management Solutions, to give readers an understanding of the importance of maintaining the 12 V battery in an electric vehicle.
As with traditional internal combustion engine and hybrid vehicles fitted with a 12 V battery, all electric vehicles have a 12 V “auxiliary” battery. The battery technology used in these vehicles are commonly AGM (absorbed glass mat), EFB (enhanced flooded batteries) and can be traditional (flooded) lead acid batteries, or in some cases lithium (LiFePO4) are used.
What may surprise you is that these batteries play a crucial role in managing the functions of the high voltage pack and still require the same maintenance and care practices as ICE vehicles. Improper care and maintenance can lead to acid stratification and sulphation of the battery, reducing its performance serviceable life, resulting in premature replacement and vehicle non-start, as well as an “unhappy driver” experience.
Potential failures
EVs experience roadside breakdowns due to “flat batteries” and when it comes to industry statistics, battery failure remains the top attributable factor for all vehicle roadside callouts. Recent roadside breakdown statistics show that 43 per cent of all roadside breakdowns are as a direct result of the starter battery and this includes both ICE vehicles and EVs. Despite the reduction in EVs’ maintenance requirements, these vehicles still have the same challenges, pitfalls and opportunities to maintain, support and replace the 12 V battery going forward.
What’s the purpose of the 12 V “auxiliary” battery in EVs, how can it fail and what can you do to minimise these risks?
The first table gives a brief overview of its role:
What can you do to maintain 12 V batteries?
- As with all discharged 12 V batteries, charging is required to restore full power performance and maximise battery lifespan and can be achieved using widely available intelligent chargers: it’s the same straightforward process and no special equipment is required.
- In contrast, the 12 V EV battery will require a unique diagnostic approach tailored to their application, which will assess available safety power capacity, to power critical vehicle systems.
- As EVs have no engine to start, traditional conductance testing is not a suitable measure of battery condition.
- The development of Midtronics SafetyPower diagnostics platform will accurately measure the available capacity of a 12 V battery.
- This cutting-edge technology and approach to 12 V “auxiliary” battery testing will provide a precise decision on a battery’s ability to power the vehicle’s low voltage loads.
The table below highlights the necessary evolution in 12 V battery testing, to ensure safer and correct vehicle functionality.
Are you getting EV service ready?
- As many workshops plan and implement electric vehicle service strategies, the inclusion of necessary qualifications and equipment to the support their future needs become a key requirement.
- While aftermarket tailored equipment solutions enabling high voltage battery maintenance are in development (enabling module balancing and cell replacement). Deployment of the most accurate diagnostic technology for 12 V batteries in electric vehicles is a positive step towards EV service readiness.
- Unlike electric vehicle traction packs that are relatively reliable and come with up to 10 years manufacture warranty, the 12 V battery is typically backed by a 2-3 year warranty, and can be a simple “win” for aftermarket workshops aiming to keep their EV customers mobile through maintenance and/or replacement of the 12 V battery when the need arises.
- Getting your workshop “12 V EV ready” by ensuring you have both the correct means to diagnose and charge 12 V batteries and implementing a proactive testing and charging programme as part of your workshop service plan, will ensure you keep your customers mobile, whilst increasing sales revenues and customer satisfaction.
What’s in it for you?
Ensuring your workshop is “EV service ready” begins with correctly matching the right technology to your service offering and ensuring you have the appropriate means to accurately diagnose and charge 12 V batteries in EVs.
Implementing a proactive testing and charging programme is essential in your workshops service plan, will:
- Help keeping your ICE and EV customers mobile.
- Boost customer satisfaction.
- Identify battery problems, before they appear at roadside.
- Increase revenues and replacement opportunities through pro-active charging and diagnosis.