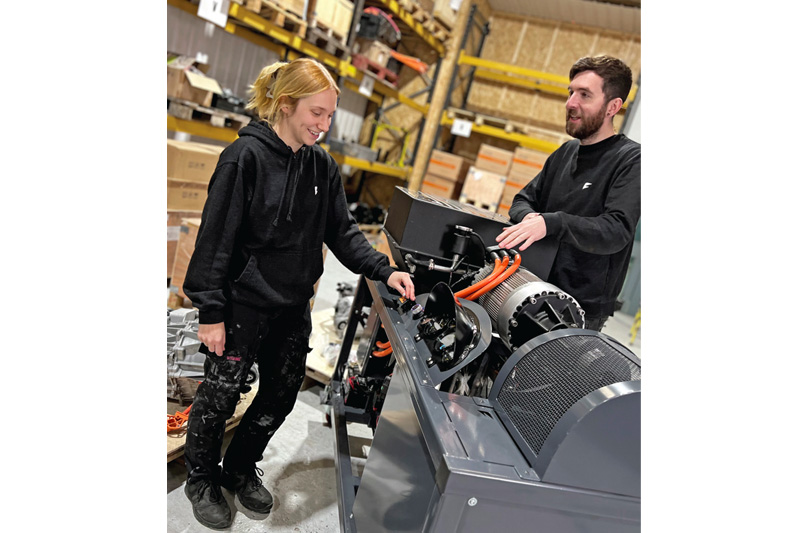
As featured recently on the PMM Podcast, Fellten provides kits and assistance to workshops taking on classic car-to-EV conversion as an extra offering. Here, the team behind the kits answers some of the questions you need to be asking before getting started.
High voltage or low voltage?
Before you do anything you need to decide what voltage motor you are going to use. Everything else ‘spins’ off that decision. Lower voltage systems (80v to 160v) have been used for years, are generally lower cost and lower power AC motors (Hyper 9 is a good example). Higher voltage systems (300v-800v) are what the OEMs are using and are also typically higher power AC motors/inverters. If you want to use any components from OEM donor vehicles like Tesla, VW, Jaguar Land Rover etc, you will be committing to a high voltage setup. You need to determine the power you require and see what is available/affordable. The inverter obviously needs to be compatible with the system voltage/motor you chose at the beginning. The ZONIC range of motors for example, come with matched inverters, are high voltage and can come with various gearbox options for transverse or longitudinal mounting.
What battery do I need?
A suitable high voltage battery pack will likely be the single largest expense of the conversion. It needs to be sized properly both in total energy capacity as well as instantaneous current capability to support the power you want to make, and not be too big to impact the vehicle’s safe handling. (Aim to stay within or at least very close to the vehicle’s original kerb weight). The BMS (Battery Management System) is the “brain” of a battery pack. It closely monitors the battery condition, voltages and temperatures down to individual cell levels and, working with the charger and Vehicle Control Unit (VCU), it tailors the energy flow in the vehicle to protect the battery cells under a wide range of operating/charging conditions. It also balances the energy available within the individual cells allowing the most efficient use of a battery’s capacity and identifying problem cells before irreversible damage is done.
A BMS provides individual cell protection by monitoring each cell’s voltage as well as the current flowing into or out of the pack. This is used along with the cell’s characteristics to determine the maximum safe current limits in its present condition which it communicates to the VCU to set limits on available power as well as the allowable regeneration energy from the regenerative braking function, why would you not have re-gen – it’s free electricity? Having a quality BMS allows the maximum power to be safely extracted from/put into a battery module at any given time.
The cell balancing feature of a BMS extends the life of the battery by continuously matching the individual cell’s state of charge with each other whilst on charge. Battery packs consist of many individual cells that have to work together so to fully utilise the available energy capacity from the battery all the cells in a pack need to be kept at the same state of charge; as the worst cell in a pack determines the current limits for the entire pack, an imbalance in an individual cell’s state of charge results in an overall loss of effective battery capacity. The BMS seeks to mitigate against this.
How big a battery do I need?
While it is impossible to say with any degree of accuracy given the almost limitless options for EV conversions, here are some very rough estimates for how many miles you can expect to travel for each useable kw/h of capacity your battery has.
- Economy driving = 3.2 mi/kWh
- Normal driving = 3 mi/kWh
- Spirited driving = 2.5 mi/kWh
- Racing = 1-2 mi/kWh
There are so many variables that affect this that you should take these numbers as a very loose guide.
How do I enclose the battery?
Your chosen batteries need to be securely and safely enclosed in a pack housing. They will perform at their best if they are kept within a warm, dry environment. Aim for this but allow them to ventilate via a Battery pack breather/PRV. This keeps moisture out but allows for expansion and contraction of the air within the enclosure due to heat changes, and should you have a battery fire it has a blow off valve fitted to prevent the pack from bursting. You will probably need to cool the battery modules inside the pack to prevent problems and keep your batteries from derating in use, or worse degrading permanently. Allow for this in your plans for your build. Placing them on cooling plates is ideal as it mounts them too, or utilising the existing modules’ cooling pathways can work well.
Does the drive layout matter?
Are you converting a RWD (MGB, Triumph, MX5 etc) and want to retain a traditional longitudinal driveline with a live axle? It’s very easy to spin a propshaft using a single speed reduction gearbox. Converting a FWD or RWD vehicle by putting a complete motor and differential in a new fabricated subframe? The physical layout of the driveline needs some thought and you may find it is not as simple as you think. You may have issues getting an MOT or even re-registered if you’ve made chassis changes even with FWD conversions. Don’t make any chassis changes as this can lead to all sorts of registration problems and ‘Q’ plates being issued. Make sure the rotation of the EV motor will work correctly and that the physical configuration fits the space. A good example here is the Tesla Model S front motor, this has the motor centreline mounted behind the differential and driveshafts and won’t physically fit in most FWD engine bays since ICE installations typically have the engine mounted ahead of the differential and driveshafts (you can make a Tesla motor spin backwards but some will require modifications to do so properly). Your drive motor will also need an inverter. The inverter takes the high voltage, the high current DC power that is provided by the battery and converts it to the alternating current electricity that is required to spin an AC motor. The inverter also controls the frequency of the power supplied to the motor to control the rotation speed and torque output of the motor. The design and operation of the inverter is closely tied to the motor being driven. In some cases the inverter and motor are combined into a single unit, like the ZONIC 120KW unit, others are often supplied as a matched pair.
Transmission or direct drive?
Some EV conversions may perform better with gearing while high power motors may not need them. Some installations will have to use a gearbox for motor mounting and drive line reasons (think rear-engined classic Beetle) so do not automatically dismiss using a transmission. However hanging a heavy flywheel and clutch on a motor shaft that was never designed for that kind of load, along with the axial thrust issues when you push down on the clutch, can lead to problems later down the line.
Do I need a parking brake?
This is a big safety/MOT issue and it is often ignored. EVs rarely have a ‘parking pawl’ like an automatic gearbox has in the transmission and you can’t leave them “in gear” like a manual as there’s nothing stopping the motor from rotating like the compression in an ICE vehicle does, so a quality e-brake (preferably with mechanical activation functionality) should be considered, however you must always retain a hand brake/parking brake at the very least though.