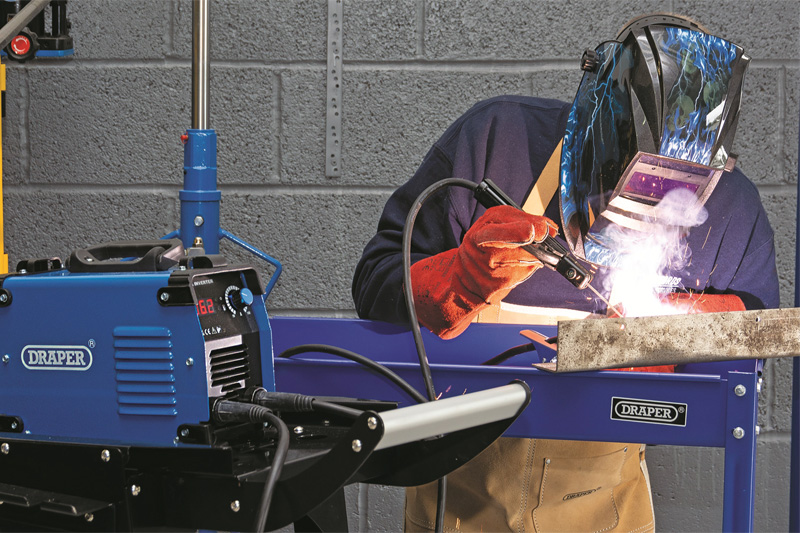
Draper Tools provides a guide to welding in the workshop and what the right options are depending on your job list.
The right welder can be a worthwhile investment for a garage, allowing for quick bodywork repairs and even repairing damaged wheel rims. The same can be said for a good quality plasma cutter. But how do you choose the right model for your garage and the jobs on your list? With so much choice on offer it can be a daunting decision. Here’s a look at the different types of welder and how to choose, plus some top tips from Draper Tools.
The world of welders: what kind do you need?
ARC Welders: Using these can be a very cost-effective and convenient welding option when you’re working with thicker materials. Predominantly used with steel, arc welding is often seen in engineering workshops, harnessing transformer technology to generate the intense heat needed to produce the perfect weld.
MMA Welders: Manual metal arc welding (MMA or MMAW) is versatile and commonly used welding technique, mainly used for welding steel and iron. It uses the same process as Arc welding, with the electric arc burning between the metal work piece and the electrode. Draper’s new range of MMA Inverter welders use inverter technology to offer a superior welding performance in a smaller, lighter machine than traditional transformer ARC welders. In the workshop they’re ideal for fabrication work and heavy duty repairs.
MIG Welders (gas and gasless): MIG welding is used in a wide variety workshop applications such as light fabrication work, vehicle chassis welding and body panel repairs. It’s an arc welding process, whereby the arc is created between the work metal and a welding wire, which melts and forms the weld filler. The welding wire spool is fed through a tensioner. At the same time a shielding gas is fed along the same supply line to the welding gun to provide an inert atmosphere and prevent oxidation which would weaken the weld. Flux-cored welding wire must be used with gasless models, in order to create the same effect. Gasless MIG welders can weld thicker metals than gas MIG welders, including metal that has rust, dirt or paint.
TIG Welders: Tungsten inert gas (TIG) welding uses a small intense arc generated from a pointed tungsten electrode making it ideal for high quality, precision welding projects on stainless steel. You need to be skilled to TIG weld but with the right preparation and training it can produce some of the strongest and most precise welds on a modern car body. TIG welding used generally for welding stainless steel, magnesium or aluminium. In the workshop you could use a TIG welder to fabricate or repair aluminium components such as radiators or sumps.
Plasma cutters: Where welders use heat to bond metals together, plasma cutters do the opposite and use heat to slice apart. They’ll cut through electrically conductive metals and just like welding, you create an arc and use heat to melt through the metal. Plasma cutters can be used for fabrication and body work. Larger, more powerful models offer a cleaner cut on thicker metals. It’s ideal to use an inert gas such as an argon/helium mix or nitrogen when cutting stainless steel or aluminium to ensure a precision cut. Plasma cutters require a clean and dry compressed air supply, so you’ll need an air compressor to use one.
Essential accessories
You’ll need the right accessories to use your welder safely, these include:
- Welding helmet, an essential for any welder, make sure your helmet is EN175 and CE approved
- Welding apron and gloves, leather is a good choice for protection and flexibility
- Welding curtain, workshops should invest in a flame retardant welding curtain to protect from welding spatter and UV and IR radiation. Check your curtain conforms to BS EN 1598
- Anti-Spatter Spray – this is designed to prolong tip and shroud life and prevent adhesion of weld spatter to your work area
Other essentials to look out for, dependent on your model of welder, include nozzle cleaners, scratch brushes, gas regulators, welding clamps and more.
Welding Best Practice
- Always protect yourself with the correct PPE and welding accessories
- Proper preparation is key. Make sure you’ve prepared the metal you’ll be working with and check your positioning and your angles are accurate too. Ensure your work area is free of fire hazards too
- Be careful not to weld near electrical systems or with the vehicle’s battery connected. Always disconnect the battery first
- One of the most common welding mistakes often comes down to simply using the wrong power supply. If your welder requires 32A power socket, do not attempt to use 13A plug
- Store your welding electrodes and wire carefully and in a securely sealed environment, moisture and poor temperatures will affect their lifespan
- Make sure you’re fitting the correct tip for wire size you’re using. This is common mistake which can mean the wire won’t feed
- Extension leads being used on welders is not advisable unless you use 2.5-3mm core wire and not over 6 meters long
- Always ensure the earth clamp is fitted to a good earthing point clean and not, for example, attached to a painted or rusted surface
- Correct cleaning and maintenance of your machine will help prolong its life and keep it operating smoothly, always refer to the manufacturer’s guidelines for this. It can help to use an air gun to blow out the inside of the welder