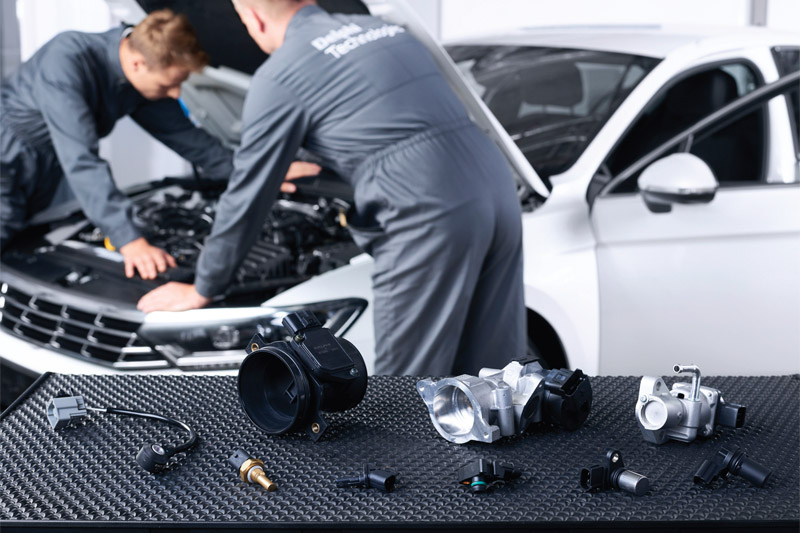
The humble ABS sensor has helped halt vehicles for decades, but what puts a stop to its own operation? Delphi Technologies explains common issues and provides tips on replacement.
Vehicle technology is evolving rapidly, from increased levels of autonomy to advanced powertrain systems. Physical brake components – with the emergence of alternative, copper-free friction materials – and the rise of accident detection systems such as AEB (autonomous emergency braking) have added to vehicle complexity, but the lowly ABS sensor has remained a staple repair for garages and is now no less important than at any time in the past 20 years.
ABS is a crucial link in a more complex chain of systems, which can be severely impacted by ABS sensor failure. For example, modules controlling an automatic gearbox can be affected by sensor malfunction and result in symptoms of expensive component failure. Workshop misdiagnosis, especially of costly components, can be an expensive mistake when it comes to reputation and promoting customer confidence and satisfaction. With that in mind, here, Delphi Technologies talks ABS sensors, diagnosis and provides some top tips on replacement.
What the experts say
“When you think about their location, it’s easy to understand why ABS sensors fail,” said Julian Goulding, Northern Europe Marketing Manager at Delphi Technologies Aftermarket. “Close to the road surface, the sensor’s reluctor wheel or tone ring can be damaged by general road dirt, especially in weather conditions seen in the UK, or foreign objects, such as rubbish. Such damage immediately jeopardises the precise operation of the sensor, weakening the signal. Operation can also be impacted by damage to wiring, sensor winding caused by excessive vibration, or a worn wheel bearing.”
According to Delphi Technologies, demand is greatest for its wheel speed sensor part number SS20160. A two-pin active sensor with 935mm cable, it fits most E8X BMW 1 Series models from 2004-13, and E9X BMW 3 Series models from 05-13.
“It’s no coincidence that the best-selling sensor covers popular models that work hard, traditionally cover a lot of miles and are now at least eight years old – it is prime ABS fault territory,” added Julian. “Our complete range of sensors are rigorously validated and tested within a temperature range of -40˚C to 140˚C. We match specifications of wire lengths, mounting and connector designs to ensure easy installation and correct fit, minimising workshop time and promoting customer confidence and loyalty. The use of planted pins within the sensors ensure greater conductivity and corrosion resistance – resulting in a long-lasting solution.”
Seeing the signs
The most common sign of failure is illumination of an ABS warning light. Some systems may also trigger the traction control/ESP light. The cause of this could be a sensor or control module, and the easiest way of establishing cause is through diagnostics.
Once the light is illuminated, that’s the ABS system over-ridden and the driver is on their own when it comes to stopping.
Another tell-tale could be the driver noticing that the vehicle takes longer to stop or that traction is compromised, especially in damp conditions or under heavy braking. The vehicle may also feel less stable in icy conditions, with reduced traction or intermittent ABS operation.
Find the location
The first step to locating an ABS sensor fault, according to Delphi Technologies, should be connection of a diagnostic tool to check for stored fault codes and, where required, analyse live data. A multimeter and oscilloscope can then be used to check the voltage and signals to the sensor, testing the connection between control unit and sensor.
A visual check of sensor connectors can then be carried out, looking for correct positioning, signs of damage or contamination. Do the same for the sensor itself and the impulse ring, cleaning any contaminants using a wire brush and cleaner where necessary.
Replacement is sometimes the only option. For such cases, it’s advised that you stick to best practice for this relatively straightforward task.
Best practice
Once wheel nuts are loosened, the correct jacking points have been used to raise the vehicle and wheels removed, some models may also require removal of the brake discs and pads for easy access to the sensor.
Remove the sensor to hub bolt and the clips securing the sensor wiring, then unplug the sensor. Use an emery cloth to carefully clean the area around the sensor.
Plug in the new sensor and make sure to route the wiring correctly before securing to the body or chassis, and re-torque the bolt holding the sensor to the hub. Refit the discs and pads, where applicable, to the correct torque settings and refit the wheels, lowering the vehicle and re-torqueing the wheel nuts.
Finally, run a diagnostic check to clear any historic ABS faults and check for new codes, visually check that the ABS light is extinguished and complete a road test for final validation.