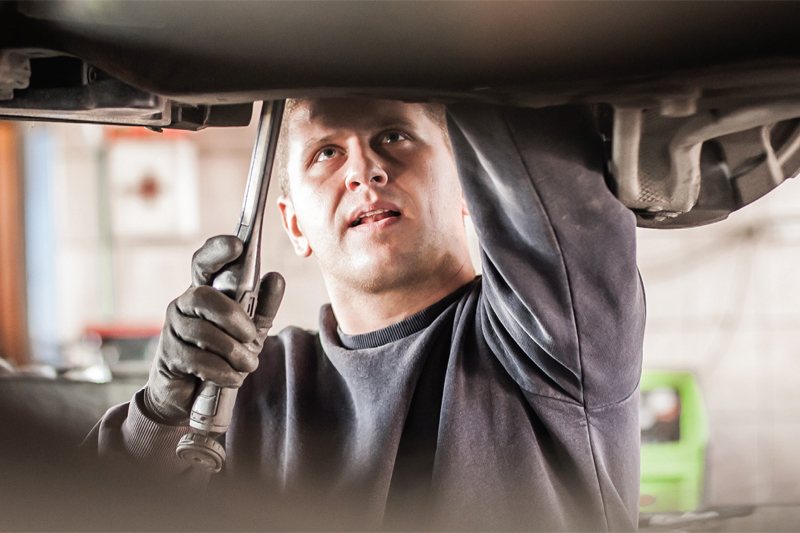
Component manufacturer FAI AutoParts has identified a selection of common problems that affect regularly replaced components, causing technicians fitment issues and, in some cases, hugely increased labour times.
To remedy vehicle-specific fitment problems, FAI AutoParts has developed a series of solutions that ensures the fitter has all the elements to turn a nightmare job into a quick and easy one.
Tesla control arms – Model S
FAI is reportedly the first in the aftermarket to offer the forward-lower arms complete with fitting bolts. The offering isn’t just a ‘nice to have’ option, but is actually a result of the original bolts needing to be cut away from the vehicle in most instances.
The design of the Model S is such that the battery housing is in very close proximity to the lower arms, making it tricky to remove without going through the painstaking process of removing the battery compartment to gain access. By cutting off the existing fixings and replacing them with the FAI kit, the job is done in no time, with the added benefit of a more complete repair having used a fresh series of fastenings.
The construction of the FAI arms has also been modified to achieve a longer component lifespan. During the part’s design process, the company’s factory found that the component had a 200% increase in the control arm fatigue test. A big part of the strength comes down to a robust ball pin, that has a pull-out rating of 80kN, an increase of 100%.
Land Rover fitting kits – Discovery and Range Rover Sport
With over 200,000 of these vehicles on the road, many doing high mileage, the wishbones are a common repair. Many technicians will have experienced frustration when trying to pry off the heavily corroded components, leaving little option other than to use brute force. The resulting damage can mean a job left unfinished until new bolts can be sourced, a problem avoided by FAI’s fitting kits.
Each kit contains all nuts, bolts and washers for the particular application, developed alongside the control arms that are already in the range. The previously mentioned points relating to reducing labour time and not relying on re-used bolts all stand for this solution, too.
Best practice after refitment
Vehicles are manufactured to have a series of tolerances to which the components operate to, but over time and with the occasional bump up a curb or pothole, the margins are moved outside of the tolerances originally set. A small amount of movement to steering and suspension components is to be expected, but this can have a knock-on effect on new parts being fitted.
After fitting control arms, FAI always suggests that the wheels are re-aligned to ensure the geometry of the vehicle is correct. No one wants a customer coming back with tyre wear issues or complaints of poor handling.