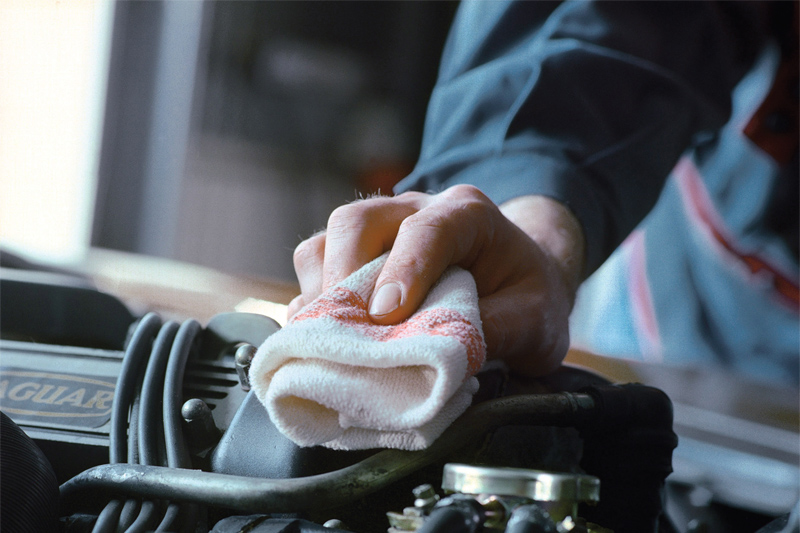
The importance of cleanliness in garage workshops is critical, especially when it comes to health, safety and compliance. MEWA UK Country Manager, Günes Yenen looks at how something as simple as your choice of industrial cleaning wipes can improve garage cleanliness, health and safety in your workplace.
It is believed that cleanliness is a sign of high standards, and multiple studies show that a clean and tidy environment makes for a more productive one. It eliminates distractions so staff can concentrate on the task at hand, helping improve efficiency and quality – and a garage workshop is no exception. A clean and tidy workshop also creates a professional image for customers and visitors.
By their very nature, workshops are greasy environments with oils, hydraulic fluids and many other liquids always being used, meaning leaks and spills are a regular occurrence. These liquids can easily drip onto surfaces and floors in high traffic areas, from where they are prone to be spread further by workers accidentally stepping in them. Keeping such areas clean and oil free can be a challenge, but is necessary to ensure health, safety and compliance.
Slips and trips
According to the UK’s Health & Safety Executive, slips and trips cause some 20% of all injuries in the motor vehicle repair industry. These accidents can be serious, often resulting in broken and dislocated bones, meaning long absences from work, which cause other problems for garage owners. Over-exposure to lubricants, used engine oil for example, may cause dermatitis and other skin disorders too, so unnecessary contact must be avoided.
Employers are required to ensure, as far as is reasonably practicable, the health and safety of all employees as mandated by the Health and Safety at Work Act. Companies must assess any potential risks to the health and safety of employees and others and take appropriate action to put effective control measures in place.
Companies which fail to prioritise workplace safety could face significant reputational and commercial risks. The HSE is responsible for regulatory enforcement that can see substantial fines levied on companies and their directors and, in extreme cases, prison.
Measures required under the Act include taking steps to control slip and trip risks as well as exposure to hazardous materials. Recommendations include cleaning up spills promptly and keeping absorbent materials to hand where there is a risk of a spillage.
Garages and workshops typically use blue paper roll or single use rags to absorb and mop up spills and clean tools and machine parts. However, any blue roll or rags which are used to mop up spills and leaks involving, for example, petrol, waste engine oil, solvents and some cleaning materials, potentially become classed as hazardous waste which then requires suitable management and disposal.
To ensure compliance with legal regulations, businesses producing hazardous waste in the UK – including contaminated wipes – have a specific ‘duty of care’ concerning that waste and must classify, separate and store any waste safely before having it disposed of by an authorised hazardous wastes contractor.
Storing contaminated wipes
Contaminated wipes may emit volatile organic compounds (VOCs) or pose a fire risk. To minimise risk to worker health and safety, they should be stored in a tightly closable container made of resistant material such as metal or special plastic (high-molecular, low-pressure polyethylene) before being disposed of.
There are also issues with laundering contaminated wipes. They must never be put straight into a washing machine; doing so could not only damage the machine’s motor, but fumes may escape and potentially cause a fire, particularly as the washing machine’s motor heats up.
Alternatives
Spillages and leaks in garages and workshops must be cleaned up quickly to minimise the chances of accidents and unnecessary exposure to hazards. The cleaning process is long- winded, and the residues and dirty cloths and rags used must be dealt with appropriately to comply with regulations – a significant and potentially costly responsibility.
With companies under pressure to ensure high standards of health and safety practice, an alternative strategy to disposable paper towels and rags is emerging in the UK.
The model is based on leasing industrial, highly absorbent, cleaning wipes as part of a full service that picks up the soiled wipes, cleans and returns them to a pre-agreed schedule. As part of the service, MEWA provides two storage containers for clean and soiled wipes. Made from robust high density polyethylene with a lid that creates a hermetic seal, it provides safe storage and transport for wipes contaminated with hazardous waste.
MEWA also supplies oil trapping mats, providing a simple way to keep the floor clean and clear from dangerous liquids. They can absorb up to 3 litres of fluid before needing to be replaced, eliminating the need for sand, granules and/or plastic tubs – also hazards on the floor.
This reusable system ensures that wipes and mats are always to hand and spills can be rapidly addressed to reduce the risks of exposure to chemicals and slipping, causing injury. The service also removes the significant burden of hazardous waste storage and disposal from companies, reducing overall costs as well as mitigating potential health and safety fines.
Even small changes to a typical cleaning regime in garages and workshops can yield considerable benefits as well as helping protect employee health and well-being and aiding regulation compliance.
Cleaning tips
- Clean little and often – create a daily cleaning rota to allow a small amount of time each day to stay on top of grease and dirt, especially for floors
- Wipe down tools and equipment after use, but always properly at the end of each day
- Have good tool and spare part storage – use cabinets, open shelves or pegboards to keep clutter off the floor and work surfaces and reduce time searching for tools
- Make sure you have all the cleaning supplies and tools you need and re-stock regularly as not having the right products will mean that the job doesn’t get done
- Have plenty of clean wipes to hand and ensure they aren’t left lying around once used, especially if they have hazardous waste on them
- Have a matting system to capture oils and other liquids to prevent their spread to other areas, particularly customer areas
- Schedule periodic deep cleaning through the entire garage to remove grime and grease, over and above daily cleaning duties