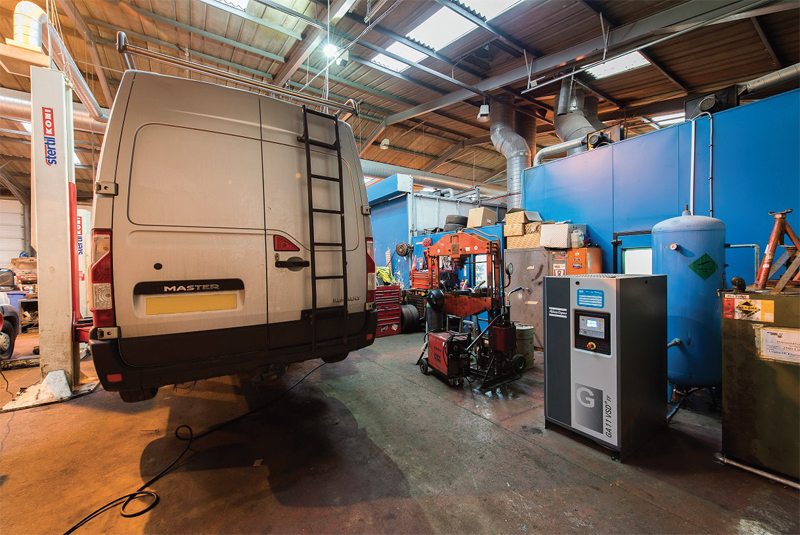
Major advances in technology make it possible for compressed air users to reap the benefits of the latest generation of rotary screw compressors. Stef Lievens, Business Line Manager for Industrial Air at Atlas Copco Compressors, explains how this type of equipment provides top performance at realistic running costs, and how it is ticking the boxes for SMEs.
The compressed air marketplace offers a complex variety of options that range from the very simple equipment offered by hardware suppliers − and even high street discount stores − right up to premier high-spec units and systems designed and manufactured by leading compressor brands for major industrial production applications.
Within that broad sweep, 75% of applications are for compressors with a unit power of less than 30kW. Until recently, this presented SMEs with the challenging task of matching a specific range of application requirements to the most appropriate type of smaller compressor with the right performance characteristics, and at an affordable price.
In order to overcome this challenge, the latest generation of compact, robust and economical rotary screw compressors has been developed with the needs of small business users firmly in mind.
A cut above the rest
In addition to overall energy efficiency, rotary screw air compressors offer multiple benefits compared to other compressor technologies. These features include low noise output, being lightweight and possessing a small footprint for point-of-use plug-and-play installation. They also offer continuous operation at temperatures of up to 46°C, extremely low oil carryover into the delivered air, simplified maintenance procedures, and a zero loss of capacity over time.
Furthermore, smaller screw compressors can be tank mounted to enable additional air storage capacity, while full-feature variants with an integrated dryer and oil-water separator protect the compressed air network and end-user output.
To see why the rotary screw compressor has made such progress in comparison to piston and vane technologies, it may help to examine the pros and cons of their operating principles and performances, relative to the average SME’s workplace requirements.
Comparing like for like
The piston, or reciprocating air compressor, has traditionally been regarded as the most economical and cheapest type of air compressor. In its simplest form, it is still the most common type found in the automotive service industry. In more demanding roles, technically advanced versions can incorporate multiple compression stages to make them particularly suitable for high-pressure applications.
However, in small to mid-range piston compressors some major drawbacks need to be considered. For instance, they are primarily intended for intermittent use. The average piston compressor can only work for about 50 to 60% of its duty cycle. These units require adequate cooling time between cycles, otherwise they can overheat and potentially fail. In contrast, rotary screw air compressors run at a cooler temperature, and are designed to operate continuously at 100% duty cycle.
Component wear is also an issue. Just like a car engine, reciprocating compressors feature piston rings and other components that are in direct contact with each other and suffer wear over time. With that wear comes a decrease in performance, oil carryover and excessive heat generation. They tend to run hotter as efficiency decreases and operating time increases. A lubricated rotary screw compressor is designed so that the compressor oil seals the internal rotors, preventing parts from wearing out. Unlike a reciprocating compressor that loses performance with age, the rotary screw compressor can maintain the same level of performance throughout its long service life.
Generally speaking, rotary screw air compressors deliver more air per kW of power compared to reciprocating compressors of the same size. This enables the use of a smaller rotary machine in place of its piston equivalent with the same output, contributing to significant energy savings.
A further complication is that reciprocating compressors require air tanks to reduce air pulses created in the compression process. As a result, they need to employ receivers to smooth the airflow and handle large demands from workplace air users, tools and equipment. On the other hand, rotary screw compressors do not create air pulses, and – depending on capacity – are able to deliver large volumes of air when required without the need for a reservoir. Furthermore, they are built to operate for an extensive working life without requiring major repair.
It is a similar story with rotary vane compressors. The simple vane principle has the longest track record since its introduction almost 100 years ago. However, such design longevity and simplicity does not necessarily equate to energy efficiency. Neither does it allow for a full range of capabilities in comparison to those offered by rotary screw compressors, in terms of turndown rates, speed range limitations and energy demand.
In much the same way as the piston compressor is affected by component wear, the vane operating principle involves continuous sliding in and out of the rotor vane slot within the stator casing. As a result, both the vane and slot are subject to excessive wear, eventually leading to failure of the vane and all that entails.
There are also significant disadvantages in terms of vane compressor’s maximum speed, which affects output; vane compressors rely on centrifugal force to operate with their maximum speed limited to 1,000 to 1,100rpm, which is a third of that for a screw compressor air element.
The new alternative
The developments embodied in advanced rotary screw compressor technology provide a clear advantage in performance and compatibility for the needs of SMEs. That is why Atlas Copco has introduced the GL15-22kW low-investment compressor range alongside its upgraded G7-15 and GX2-7 EP series, to offer robust performance, simple installation and maintenance, plus easy control and monitoring for air users in the 2-22kW (4.0 to 22.8 l/s) segment.
The GL15-22 belt-driven, fixed-speed compressor range has been designed to provide quiet, efficient, powerful and reliable performance combined with minimum total cost of ownership. The 15, 18 and 22kW compressors within the range increase free air delivery by a 7.2% margin, while also reducing the specific energy requirement by 5.6%, compared to previous models.