Neil Pattemore considers the ongoing battle for control of the diagnostic, service and repair market. With the undoubted threat posed by the ‘connected car’, will the independent aftermarket be able to survive and thrive against the VMs?
It has often been stated that if a business stands still it will not survive, but the clever bit is knowing what to change and when to change it. Often, this is a gradual process that encompasses such technologies as the telephone, the internet or social media. These external changes have allowed workshops to better communicate with their customers to support their service offers through these various forms of electronic ‘interface’.
However, the ability to communicate with the vehicle has always been the very fabric of these service offers, to conduct diagnostics, service, repair and maintenance in all its forms. Today, this process starts with the vehicle coming to the workshop, where the work or the replacement part is identified, then ordered and the ‘complete repair process’ is conducted. This has been the way that things have been done for over a century – but all this is changing and it is changing exponentially. A new challenge is coming from a direction which may not even be on your radar.
You will be familiar with the old adage, ‘familiarity breeds contempt’, but you may not be familiar with how this may soon impact your business as the ‘connected car’ becomes an everyday reality. You may never have stopped to think about it, but in one way or another, the standardised 16 pin connector has become the basis of your business. So, what is this threat and what is changing?
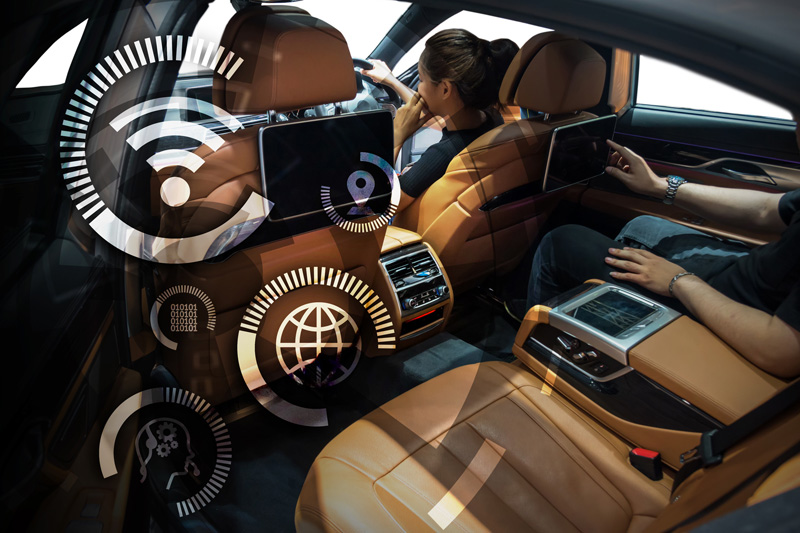
Quite simply, with new technologies supporting remote access to the vehicle, the ability to conduct diagnostics remotely, to identify the replacement part and to know what workshop resources are needed, will allow the complete repair process to be identified and planned to significantly reduce the costs at every level of your business. Great news I hear you say!
Unfortunately, this remote access is only available to the vehicle manufacturers that are entering the aftermarket and are also in a position to control the complete repair process. Your competitor is no longer the ‘garage around the corner’ (whether this is another independent workshop or a main dealer), but the competition now starts directly in the vehicle with access to the vehicle’s data and the dashboard display.
So, remote access to in-vehicle data is only available to the vehicle manufacturers – allowing them to propose service or repair offers directly to the customer, directing them to a workshop suggested by the vehicle manufacturer – one which is likely to use the vehicle manufacturer’s spare parts as part of its offer.
Perhaps you have heard about the new remote access (telematics) systems (driven by the mandatory introduction of the ‘eCall’ system in all newly type approved vehicles from 2018) and the various threats of both remotely hacking the vehicle, or being able to connect to the in-vehicle networks through the 16 pin connector to re-program keys and steal the vehicle. Subsequently, in-vehicle security is being significantly enhanced and the ability to communicate through the 16 pin connector for normal diagnostics, or for repair and maintenance, is now being restricted to when the vehicle is stationary in the workshop – in other words, there is no data available remotely when driving.
However, the vehicle manufacturers must continue to comply with the legislative requirements of providing access to vehicle data for independent operators.
This may be made available in one of two ways. Firstly, through the existing OBD connector, but this may be (legally) restricted to emissions data only and will be closed when driving for ‘security and safety’ reasons. Secondly, the vehicle manufacturers are proposing that any data which is no longer available through the OBD connector is provided via their ‘extended vehicle’ concept. This provides access to the vehicle data via the ‘back-end’ of the vehicle manufacturer’s server, but this will be restricted to repair and maintenance information only, which may exclude the remote analysis for diagnostics or predictive services.
This will introduce several new threats to your business. Firstly, the vehicle manufacturer controls all access to the vehicle and subsequently the quality and content of the data available. This may become more limited and may be defined by ‘use cases’, meaning that the data will be defined as engine or brakes, so if you need to work on steering, it will be another use case – and each use case may be restricted to pre- verified certificates/diagnostic tools and may also be separately chargeable.
There may also be other increases in costs, as diagnostic tool manufacturers will no longer be able to create their diagnostic programs using reverse engineering, but will have to buy expensive diagnostic data from the vehicle manufacturers and then spend more money to re-engineer it to become part of their multi-brand tool.
Secondly, the vehicle manufacturer is in constant communication with the vehicle, so is able to monitor the status of the vehicle, including a part failure (prognostics) or when a service is due (predictive maintenance).
“Your competitor is no longer the ‘garage around the corner’ (whether this is another independent workshop or a main dealer), but the competition now starts directly in the vehicle with access to the vehicle’s data and the dashboard display.”
Thirdly, and probably most significantly, the vehicle manufacturer can directly contact the driver and propose a repair or service offer – diverting the driver to the workshop preferred by the vehicle manufacturer – meaning that you may never see the vehicle and be able repair it. The vehicle manufacturers are now not only entering the diagnostic, service and repair market, but are in a dominant position to control it.
Even if the driver brings their vehicle to your workshop, if you then have to access vehicle data via the vehicle manufacturer’s ‘extended vehicle server’, then the vehicle manufacturer will know who you are, what vehicle you are working on and what parts may be required. From this, they can offer their service directly to the customer in direct competition.
The only solution to these threats is the ability to retain direct access to the vehicle, its data and resources, both in the workshop and (increasingly) remotely. These critical requirements are currently being discussed in Brussels, but it is not an easy discussion. The battle is to decide who will provide aftermarket services – vehicle manufacturers or independent operators.
The fundamental basis of the aftermarket having un-monitored access to in-vehicle data, free of charge and with the ability to offer customers a competitive choice, is under serious threat, both from the ability to access vehicle data, and subsequently for the aftermarket to maintain independent repair methods and to offer these critical new ‘remote services’.
Obviously, this threat is being strongly opposed by the UK Aftermarket trade associations, working through their European offices in Brussels to maintain legislative support, but never has access to vehicle data become such an important part of the aftermarket’s future.