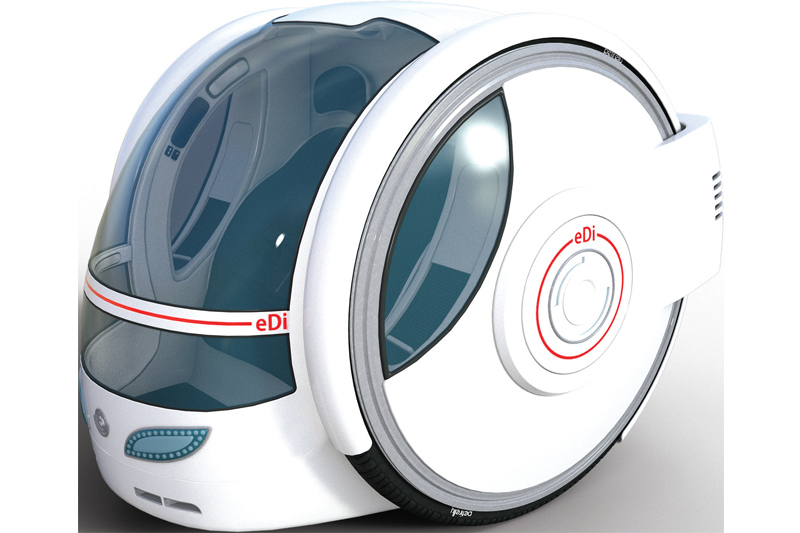
Tom Denton, founder of the Automotive Technology (AT) Academy and prolific publisher of automotive training textbooks, finishes his series of articles on learning. This month, Tom travels forward in time to 2070 to put some questions to a technician to find out how different things could be.
In the first three articles in this series, I first looked at EV training, at how we learn using different methods, and then compared different scenarios. In this final article I will consider these two questions:
What do you really need to know?
Why bother learning anything when you can just look it up?
Let’s speculate on the future. What will our job be like in about 50 years? Here is a summary of what a technician from 2070 had to say when I interviewed him…
Q. What hours do you work?
Like most people I work shifts because everything operates 24/7. I do six hours, five days a week. My job is to supervise the servicing and repair operations and diagnose unusual faults. Most people have a personal AI that is connected to the WWW (the World Wireless Workgroup).
Q. What are typical service intervals?
In most cases, servicing and repairs are only done when a car’s AI decides something is necessary. On-board monitoring systems regularly check every system and the AI has access to critical failure predictive data. This reduces the amount of service and repairs needed. Since fully autonomous cars started to be used in about 2035 the number of accidents have reduced, so body and paint repairs are also lower.
Q. What components are used and how do you diagnose faults?
When a car arrives in my workshop, I know exactly what is wrong with it because its AI has communicated all the details to our company system. The replacement subunits are already waiting. All cars are of a modular construction and consist of five major subunits: power pack, drivetrain, central computing core, electrical power control, and body. There are some major differences in body subunit types for various levels of comfort, but the others are the same for all cars.
Q. Do you personally replace the subunits?
No, don’t be ridiculous! The appropriate subunits are changed by robots (occasionally all five subunits are changed!), and the car leaves the workshop 20 minutes after it arrived at the most. The various subunits are then returned to their specific factories and are refurbished before being returned to us. Someone told me that these cars are like Trigger’s broom, but I’ve no idea what this means.
Q. Does anything complex ever go wrong that means you have to know how to diagnose faults?
Yes, occasionally, something goes wrong and that is when I really earn my wages! Yesterday for example, some kind of glitch meant that when a new power pack was fitted, it blew the electrical power control (EPC) unit, and the car wouldn’t move. The repair was simple, two different new subunits, and off the car went. However, finding out why this error occurred was more complex.
Q. What steps did you take to find the fault?
I started by remotely interrogating the EPC’s AI. The information in this unit seemed to be all correct, so it was time to break out the test equipment. I physically connected the communication network analyser to rule out any wireless issues. The comms patterns looked wrong and my personal AI confirmed this. I then checked deeper into the system by removing some of the nodes on the network and finally the comms patterns returned to normal. At least I now knew which subsystem of the subunit was at fault. After further logical diagnostic checks, I eventually found a wiring connection to a sensor that had shorted out. It looked like some of the wires had been chewed by rodents! I sent the subunit back to the repair factory with a log of my findings attached.
Q. How long did you spend learning about automotive technology?
I didn’t study automotive technology at school or college. Education and training changed radically many years ago. Nowadays, it is all about learning how to learn, what you need when you need it, rather than how to do specific things. For example, when diagnosing the fault on the car mentioned before, I downloaded detailed information about each specific system and test as I needed it.
Now back to the present day. Let’s return to our two original questions:
What do you really need to know?
You don’t need to know how a motor works to be able to change oil or coolant. But you do need to know the operating principles of an EV drive to find the cause of a fault. In the future when it may be even easier to look things up, we will still need to know the fundamentals of how systems operate, how to use equipment, and only then perhaps look up the details.
Why bother learning anything when you can just look it up?
Let’s take an example to compare two methods:
- I ‘know’ how an EV drive motor is operated by three-phase AC. I ‘know’ how to use a scope so I can measure it and show it as a waveform. I ‘know’ what the waveform should look like, so if it looks wrong I ‘know’ there is a fault.
- I look up how an EV motor works, what test to carry out, how to carry out the test, and what the results should look like. Then I carry them out and I ‘know’ there is a fault.
To me the obvious benefit of the first method is that it is much faster and we can be more confident in the process. On the other hand, the second method ensures we are using the correct information, for the specific system and comparing results with exactly the right data.
Perhaps the answer is that there is a hybrid approach where a combination of what we already ‘know’ and what we can look up is ideal. What is certain is that we definitely need to ‘know’ how to look up the right things!