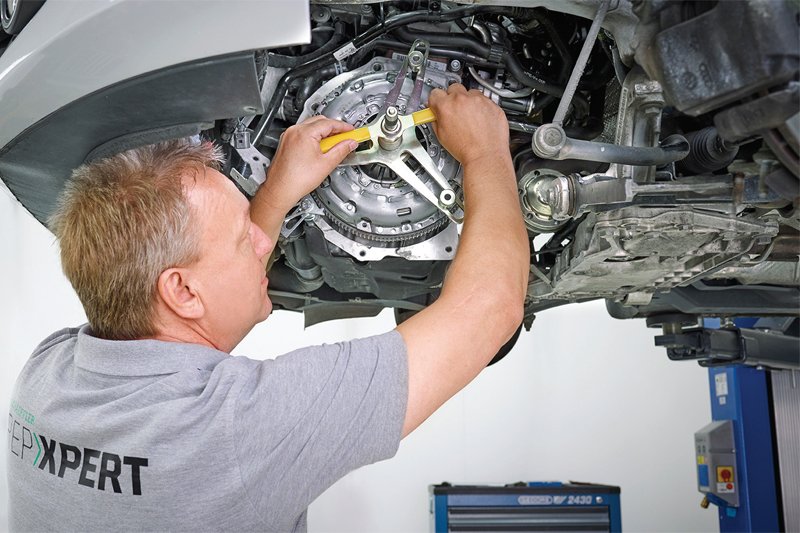
Schaeffler REPXPERT Alistair Mason explains how transmission system production has adapted to the structural changes in engine design.
Engines are changing, so the clutch and transmission system is being adapted too. Manual gearbox cars are still very popular, so there is still a high demand for clutch repairs and replacements. The number of vehicles using self-adjusting clutches continues to increase, as they give the benefits of a lighter clutch operation with a consistent bite point and clamp load.
However, we are now seeing the use of hydro-electric clutches in semi-automatic transmissions, where an electrical actuator controls hydraulic pressure to the concentric slave cylinder to operate the clutch. A position sensor is fitted to the slave cylinder to give feedback on the clutch position.
Furthermore, most vehicle manufacturers (VMs) are now using double clutch systems. The main advantage is the gearchange speed – which can be as quick as 0.08 seconds! Because of this, when accelerating, drivers tend to hold the throttle in one position until the desired speed is reached, and then they lift slightly to maintain that speed. As a result, it is lot easier for the vehicle to run at Lambda 1 to aid emissions control and, because the gearbox is controlled by an ECU, it is always in the correct gear. The dry double clutch system is the most efficient, as there is no drag on the clutch.
Make sure of maintenance
Generally, the only maintenance required on the transmission system is to change the oil on automatic, wet double clutch and constantly variable gearboxes. This is because the oil becomes contaminated as the clutch wears, losing its lubricating properties as it deteriorates, causing premature wear on associated components, and leading to expensive repair bills.
Another area to look at, to ensure gearboxes are maintained properly, is the control unit software. VMs are constantly modifying software to optimise systems and prevent potential problems.
Advice for sourcing parts
My first piece of advice in this area would be to fit quality parts from a known manufacturer – do not simply choose based on price. It is the workshop’s reputation at the end of the day, and if rectification work is required due to faulty parts, who’s going to pay? There’s also going to be an unhappy customer.
I’d also recommend not ‘mixing and matching’ parts during a clutch replacement – use all components from just one brand, as they will be optimised to work together.
Tips and tricks
Spend 10 minutes researching the job; special processes are becoming more common, which means mistakes can be costly. Software updates can resolve a lot of faults, so these are always worth checking before removing major components.
Use the correct tools; tolerances are a lot finer these days and components are more sensitive. The tool will pay for itself if the job has to be done again.
Technical bulletins are becoming more widely available on manufacturers’ websites, so it is always worth checking if there is one for your job, as this could save a lot of time and effort.