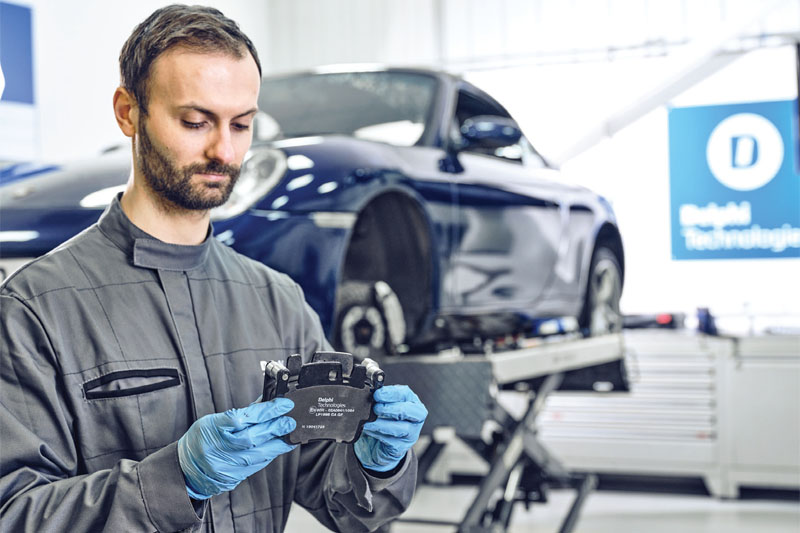
Offering significant benefits in terms of noise reduction at a time when powertrains are becoming quieter and more refined, the use of directional brake pads is increasingly common amongst vehicle manufacturers, as PMM finds out.
Although the majority of current advancements in automotive design revolve around enhancing efficiency and developing viable alternatives to traditional diesel or petrol engines, there is the general expectation that these should also have a positive effect on the driver experience, with the byproduct being a quieter, more relaxing ride. With this in mind, noise, vibration and harshness (NVH) reducing technologies are becoming even more important.
Whilst the emergence of quieter, electric and hybrid vehicle technologies should, in theory, lower NVH levels, the reality is very different – the loss of the engine masking sound is simply exposing other areas such as suspension, heating and ventilation systems and braking – noises that may not have been obvious to the driver beforehand. Add to this greater emphasis on the whole in-car experience and noise issues are becoming an area of increasing concern for vehicle and parts manufacturers alike.
One of the ways that Delphi Technologies has tried to tackle this issue is by focusing on its production of directional brake pads.
“We’ve invested significantly in the development of directional brake pads over the years, constantly evolving our offering,” said Marco Lagomarsini, Braking Category Manager, Delphi Technologies Aftermarket.
“We have two different types depending on the application, featuring either a chamfered friction surface or a crescent cut out of the shim, but both have to be mounted in a specific direction for optimal pad-to-disc contact. By introducing the pad to the disc at a gentle angle, the likelihood of both noise and vibration is significantly reduced for even quieter braking.”
The company’s chamfer directional brake pads have the chamfer between two adjoining faces, on either the leading edge or both edges of the pad. This helps to prevent the leading edge of the pad from lifting from the disc for maximum pad to disc contact, which encourages even pad wear and reduces both noise and vibration.
For its crescent directional brake pads, these have a crescent or half-moon shape cut out from the shim. The shim, made up of finely tuned layers of dampening material bonded to the pad assembly, helps to reduce both the transmission and amplitude of vibration and acts as a thermal barrier, ensuring uniform temperatures across the pad, and in turn consistent brake torque. The addition of a cut-out allows the piston to push the brake pad at the optimal angle, reducing noise and aiding even pad wear.
“As their name suggests, ‘directional pads’ must be installed in a specific direction to ensure optimal noise performance. Fitting them in the wrong direction can reduce braking efficiency, and may increase the possibility of brake noise, the very thing these pads are designed to prevent,” added Marco.
To help technicians, many of Delphi’s directional pads use either a letter, indicating which side of the vehicle the pad should be fitted to, or an arrow showing the rotational direction of the disc and hence the direction in which the pad should be fitted. If no arrow is present, then the company recommends for pads fitted with a chamfer, to introduce the chamfer (the largest if more than one) at the leading edge where the pad and disc first come into contact. Alternatively, if the pad features a cut-out, position the crescent or half-moon at the leading edge of the pad.