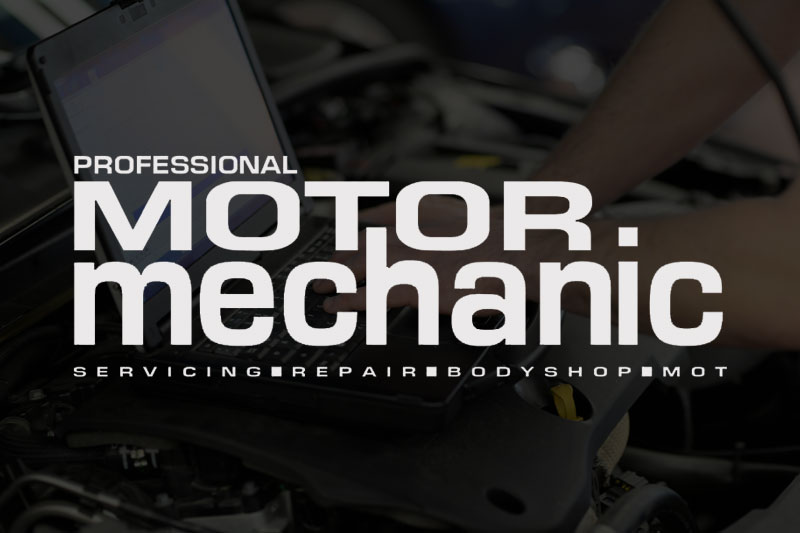
The major difference between electric powered assistance and the previous systems we’ve focused onis that there is no hydraulic fluid and associated components involved. All mechanical assistance is provided by an electric motor mounted either within the steering rack or the steering column.
Electric power assist steering systems are designed to use an electric motor to provide mechanical assistance, thus reducing driver input effort and fatigue. Torque, position and angle sensors built within the steering column or steering pinion send signals to the electric assist power steering system ECU while vehicle speed is also received via CAN bus. These signals are then interpreted to provide an appropriate level of assistance to the driver.
Most steering assistance is typically needed for low speed, high angle situations, such as parking and manoeuvring; whilst minimal assistance is required at high speeds, such as motorway driving.
Due to the fact that no hydraulic fluid is used, there is a reduced risk of environmental contamination from the steering system. Along with the benefit of having no hydraulic fluid, there is also a minimal component count, as there’s also no need for a pump, hoses, reservoir and drive too. The added benefit of this is that the installation package is smaller and there is reduction in noise too.
A typical electrically assisted steering rack with integrated motor is shown in Fig 1, whereas the alternative method of providing electrical assistance – which has the assisting motor within the steering column – is shown in Fig 2.
Fig 1
Fig 2
One similarity between the electrically powered hydraulic and the electric powered steering systems is that energy is only used when demanded by the driver’s inputs, which helps to reduce fuel consumption and emissions.
You may remember from our previous article that electrically powered hydraulic steering systems reduce fuel consumption by up to 0.3litres/100km (3.75 MPG). Direct acting electric powered steering systems go one step further by reducing fuel consumption by an additional 0.2litres/100km (2.5 MPG) over traditional belt driven power assisted steering systems. There is a reduction in weight too, typically by about 5kg.
Electrically assisted steering columns were primarily designed for smaller cars, where space within the engine compartment is typically at a premium, providing up to 100N (approx. 10kg) of assistance. Conversely, a rack-mounted electrical system can provide up to 12,500N (approx.1,270kg) of assistance. This amount of assistance requires considerable current (up to 80A), so therefore a considerable amount of heat is generated too.
The generic layout of a steering rack assist system is shown in Fig 3.
Fig 3
This illustrates a system that uses a second motor driven pinion to provide the power assistance. However, please remember that some manufacturers use a motor to drive a ‘powered nut’ to provide steering assistance.