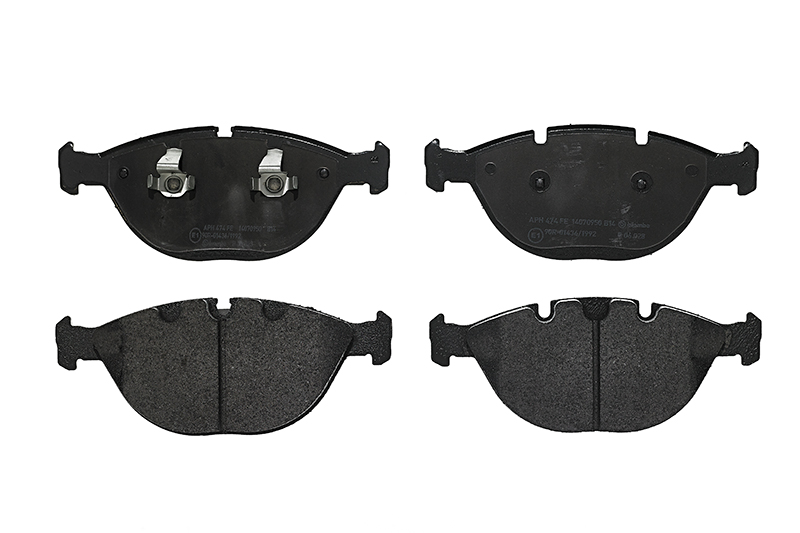
Brembo continues its look at how manufacturers can create a smoother braking experience for drivers.
As a recap, in part one of this article, noise, vibration and harshness (or NVH) produced by brake discs was explained and the preventative design measures and materials used to reduce NVH on brake discs were discussed. In this article we will cover NVH produced by other components in the braking system and discuss the solutions taken to reduce it on brake pads and calipers.
Besides the juddering that was discussed in the first article, the braking system produces several categories of brake noise e.g low or high frequency squeals.
Both are caused as a result of a phenomenon of dynamic instability that occurs at one or more of the natural frequencies of the brake system. In general, the sliding of the pad against the braking surface of the disc leads to small fluctuations in the friction force itself. This can then resonate with the components around the friction material, further amplifying fluctuations in friction force and generating noise. When the brake pad does not move in harmony with the caliper piston, the result is an increase in noise, vibration or harshness.
There is a common misconception that squealing is a result of the friction material itself. While this might be the case for high performance brakes used on the track, for road use there have been several advanced solutions used to reduce this. Brembo uses more than 100 different compounds, designed to offer the most suitable solution for each type of car and driving style, in terms of both performance and comfort. When developing the compounds, there are more than 20 different properties to be considered. When designing a pad there needs to be a balance on performance and comfort. In high friction brake pads for racing purposes this creates high energy at the friction interface this can lead to more brake squeal which isn’t acceptable for normal everyday situations. Brembo’s tribologists have developed ways of engineering out the noises audible to the human ear by knowing the exact raw material to use without compromising on performance, by adding graphites and other elements to create dampening effect. Besides the materials used, the design of the pad is also taken into context.
Chamfering
The primary role of chamfering is to improve braking comfort by eliminating squeal and noise. Chamfers can control how the edge of the pad contacts the disc. A cornered edge on the pad clamping the disc can be quite harsh. By angling the edge, we can make sure that the largest possible edge of the pad makes contact with the disc when clamping. This smooths out the clamping action. Besides reducing NVH, the other purposes of a chamfer is to induce even pad wear, to prevent the leading edge of the brake pad lifting and being pulled away by the brake disc. If the leading edge of the pads has a sharp edge, it increases the tendency to grab and bounce more than if the leading edge is chamfered.
Brake pad slots perform triple duty: firstly, they divide the surface in two smaller areas reducing the thermal deformation. Due to heat, pads will bend and flex on their backing plates. If a solid piece of friction material is used on a pad that flexes quite a bit, it can lead to excessive NVH and even chunking of the friction material. Secondly, slots break the friction material into separate units to change the frequency and amplitude of brake vibration. The slot will eliminate warping of the metal backing plate. Lastly, the slots facilitate the expulsion of friction material particles abraded during braking from the pad-disc contact surface.
Brake shims
Brake shims have the ability to control noise in three different ways:
- Prevent and reduce the transmission of vibrational forces that cause excitation of the caliper, pads and all the attached structure
- Shims can add mass to the brake pad to dampen vibrations and oscillations in the pad and caliper. Shims reduce reaction forces transmitted back into the brake piston using an elastomer interface coatings on their surface
- A good brake shim can act as a thermal barrier to ensure consistent temperatures across the entire face of the pad. This can help to ensure a consistent braking torque. Brembo provides a multi-layer shim made out of a mixture of different layers of metal and rubber for maximum comfort. The arrows on the anti-noise shim of Brembo brake pads indicate the disc rotational direction, which means they should be taken into account when fitting the pads inside the caliper body. Fitting instructions can be found here
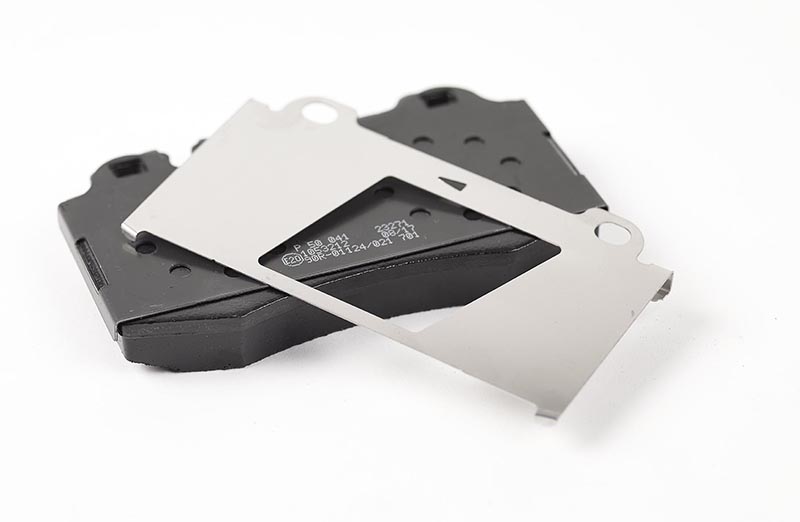
Brembo directional brake pads were created to enhance the comfort of the braking system, so fitting them on the wrong side could increase the noise level during braking, increase pad wear and reduce system performance.
A huge challenge in NVH prevention is minimising the vibrations of the components when in motion. If they do not move in harmony with each other but collide with each other this can create unwanted NVH.
This is one of the functions of the spring clips that come in the form of metal, wire or ribbon component. These reduce/eliminate noise and return the pads to the rest position after braking when the kickback from the disc is insufficient. Due to the constant exposure to varying temperatures these components can lose their tensile strength due to the annealing process.
Brembo provides the complete solution by providing brake pads complete with a range of accessories and assembly kits, included in the box. Replacing these accessories at every pad replacement is a compulsory servicing method as these fitting kits can lose up to 50% of their tensile strength in only two years. Supplying the pad as a complete kit ensures that these components are replaced at all times required to prevent further issues and is also far more economical compared to purchasing these parts separately.