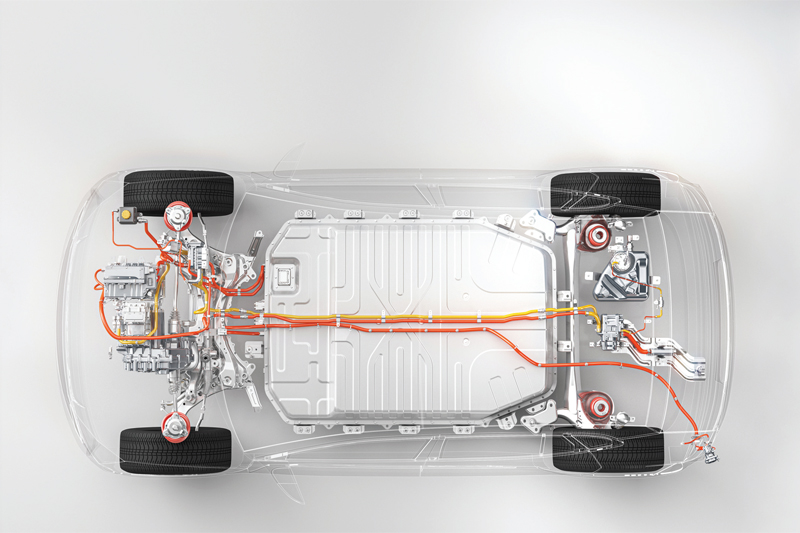
Regular PMM contributor Steve Carter highlights how the braking systems on electric vehicles have adapted as the technology has progressed.
In my previous article in the October edition, I looked at how the air conditioning system on an electric vehicle is fully integrated into the operation of the battery thermal management system, as well as the vehicle’s own climate control – providing both heating and cooling for passengers and the battery alike.
Moving on, I will now investigate the braking system on electric vehicles, often referred to as regenerative braking. More recently, this has been further enhanced and refined into ‘one-pedal driving’. This configuration in some of the latest vehicles now engages the brakes through wire systems to control all the various inputs and outputs to the control units, with FlexRay replacing the CAN-Bus network system. All hybrid, plug-in hybrid, and electric vehicles have batteries of varying sizes and power delivery modules to control the following:
- Conversion of the DC to three-phase AC currents to drive the motors, and then the conversion back to DC to recharge the drive battery when decelerating
- The torque and RPM of the motor for driving as required
Most of the electric motors we use are of the synchronous permanent magnet type, which means they will become generators when rotating force is applied during deceleration. Now, if we look at some of the latest electric vehicles, such as the four-wheel drive models, there is one powerful motor/generator (MG) on each axle. The car’s kinetic energy is applied to these MG units, which subsequently generates the AC current that can then be converted into DC current to recharge the battery and increase the vehicle’s overall range. From my own experience, I can vouch that I have regenerated 25% of the overall distance of a 156-mile journey.
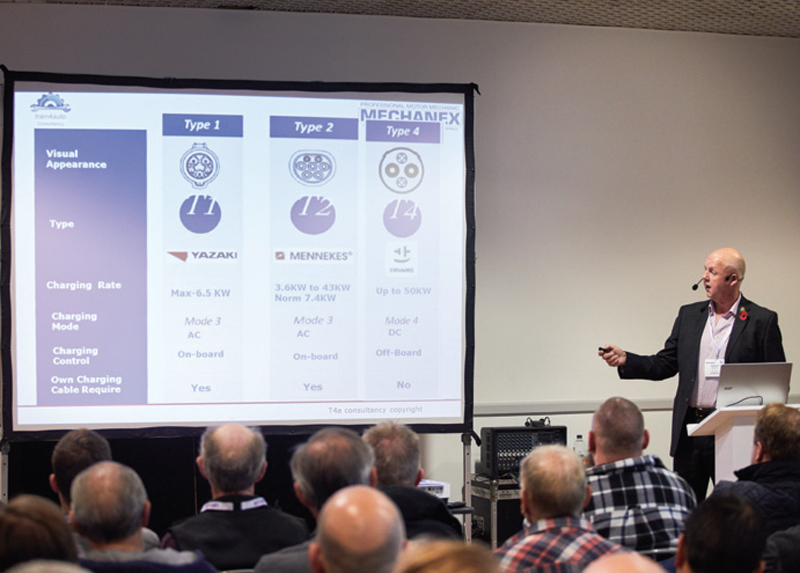
In the first generation of hybrid vehicles, the battery was so small (1kWh) that there was a limited amount of energy that could be recovered, which meant that the regenerative braking was quite poor. However, with the development of plug-in vehicles, the battery size has increased to about 14kWh. This obviously increases the amount of power the car can recover.
With more and more regenerative systems now available, the manufactures are looking for more ways to control this function progressively. For example, the Mitsubishi Outlander PHEV has selective levels of regenerative braking – achieved by the driver flicking paddles behind the steering wheel: Level 0 is the equivalent of freewheeling, whilst level 5 is significant deceleration.
However, the level of regen is dependent on the state of charge of the battery. With a high state of charge and selecting level 5 regen, the vehicle would show virtually no sign of slowing down, as there is no capacity for the battery to receive more charge. Therefore, the driver would need to apply the foot brake. A driver of this vehicle might well believe that there is a fault with the braking system as regenerative braking by the paddles would appear to be inconsistent. Yet, no fault exists, it’s just the way the system works.
With the latest range of electric vehicles now offering battery sizes of between 60 to 90kWh, we now have significant storage opportunities for regenerative braking and most manufacturers are taking this opportunity to integrate this into ‘one-pedal driving’. The gradual release of the accelerator pedal will now increase the rate of regen and the speed with which the car slows. There is now no need to put your foot on the brake pedal, in fact, the pedal is now only used to stop the car moving forward at the end of the Junction.
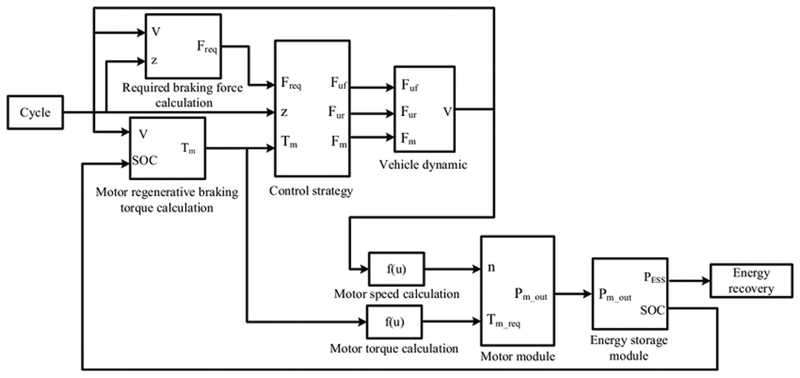
To control all these systems and the information from the various sensors, as well as provide a failsafe backup, a more robust and larger bandwidth network system was needed. The Audi E-tron and Jaguar I-Pace are both using FlexRay networks to control the regenerative braking and electric motors on their EV vehicles.
I would like to highlight that this is only a very brief overview of what ‘one-pedal driving’, brake-by-wire and regenerative braking are, and how they will affect your business. Hopefully, you have appreciated the complexities of these systems and the need to fully understand them before any work can be carried out on any vehicle using them.