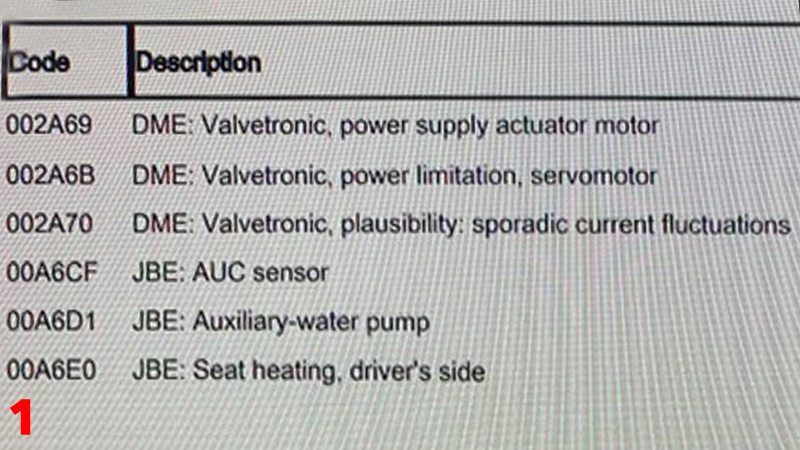
BMW diagnostics specialist Ben Johnson uncovers the layers of intrigue and mystery set upon a sorry E90 by the previous garage to discover the root cause of the valvetronic’s woes.
The tingling sensation down my spine, coupled with a touch of nausea, is a feeling all too familiar to me when a customer drops the bomb – “Joe Bloggs at Dodgy Dave’s Garage has changed the valvetronic motor because of such and such a reason.” Our protagonist in this automotive drama is none other than the N46 engine, a creation by BMW that can only be described as less than stellar in the grand history of BMW engine design. This particular E90 vehicle arrived at the workshop, a pitiful soul trapped in the clutches of a malfunctioning valvetronic system playing a lackluster tune – limp mode, with the throttle butterfly reluctantly stepping in for the variable valve lift system.
In customary fashion, my first move was to inspect the fault code printout from the previous repairer, strategically laid face up on the passenger seat. The ominous codes 002A69, 002A6B, and 002A70 stared back at me, a triumvirate of trouble that also made its presence known during the ISTA vehicle test (Fig.1). The cryptic “X Reason” continued its nonsensical dance, and my intuition hit the bullseye – the period preceding the valvetronic motor overhaul likely echoed with the familiar chorus of those troublesome fault codes. Regrettably, the fault code list, though in my possession, told a tale more perplexing than enlightening. It seemed to be a postoperation relic, concealing the original motivation behind the motor’s replacement in a veil of uncertainty. Dodgy Dave’s mysteries persist, leaving us entangled in an enigma with more questions than answers. The plot thickens, and the automotive intrigue deepens.
The alleged miscreant: a power supply glitch at the valvetronic motor – a seemingly straightforward fix, or so I hoped. All that stood between me and victory was a missing voltage supply, a minor hiccup easily rectified by consulting the wiring diagram. But, in the unpredictable world of Dodgy Dave, simplicity in uncovering what has and has not been carried out is never a given.
I couldn’t shake the feeling – call it a mechanic’s hunch – that this job held more than just a voltage supply issue. Dodgy Dave’s touch tends to leave a lasting mark, and I sensed a lurking catastrophe waiting in the wings. As we all know, in the realm of automotive challenges, nothing is ever as straightforward as it appears.
According to the wiring diagram, the valvetronic motor gets its power supply from a relay housed in the E-Box. The relay is a bit unusual in that it doesn’t follow the standard practice of using terminal 86 to switch the coil. Instead, the coil draws power from terminal 30, while the DME grounds the other side of the coil to activate the relay.
The power supply then flows through two terminal 87 outputs, making its way back to the DME. From there, the DME takes control, managing both the 12V and ground sides of the motor as needed. It’s a straightforward journey of electrical currents, and navigating it involves understanding the interplay of these components in the Valvetronic system. All of this is powered by a 30 Amp fuse on the terminal 30 input to the relay.
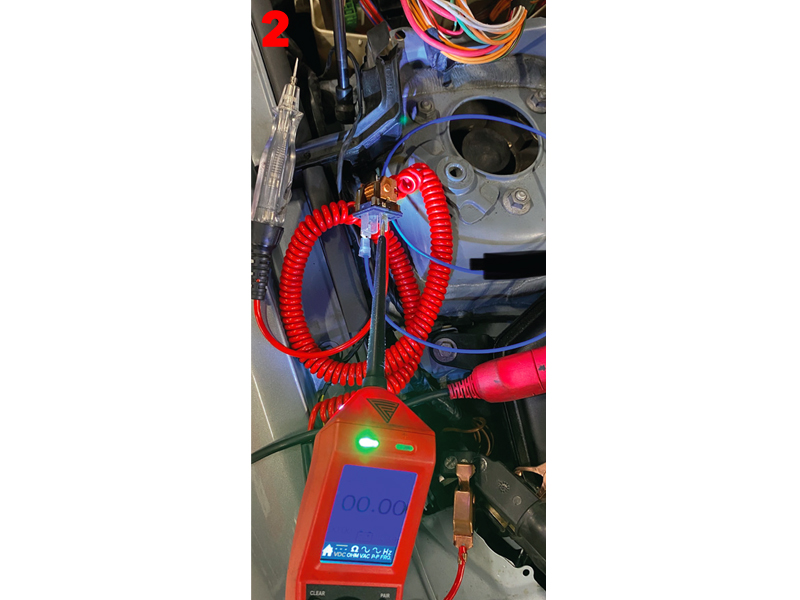
A swift check of the relay with the Maestro proved that it was as dead as a doornail (Fig.2). Bizarrely we actually had a new relay in stock which made the repair continuity sail onwards to a successful outcome – or so I had hoped.
Following the installation of the new relay, there was no delay in trying to wipe the slate clean of fault codes – and there you have it, success! Two out of three codes successfully erased. Yet, the persistent 002A70 code stood its ground, refusing to erase. It seemed like the issues related to the valvetronic motor’s operation might have been put to rest. However, a new challenge emerged as the motor remained unresponsive when attempting to teach in the valvetronic end stops.
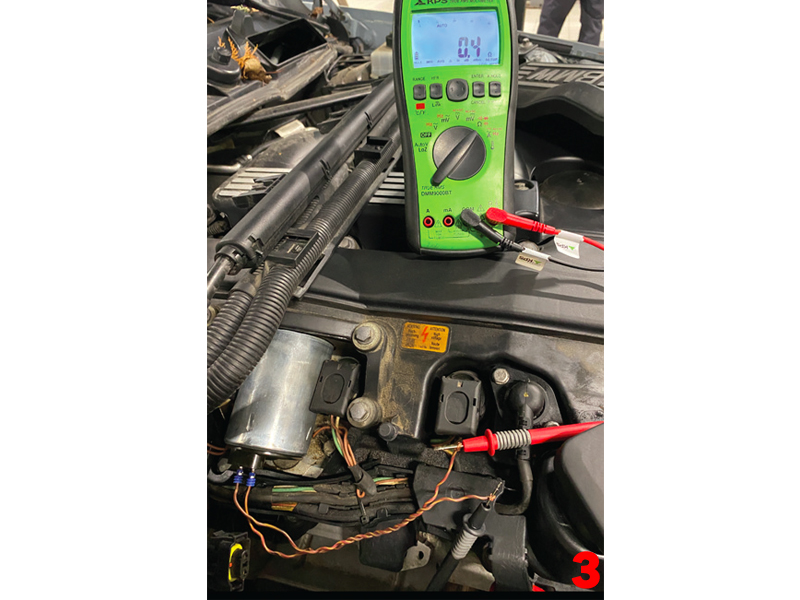
The advantage of having a visual insight into conducting valvetronic end stop learning with the cover off is undeniable. It provides a clear view of the mechanical movement in progress. Before taking the plunge and removing the cam cover, a wise move was to check the motor windings’ resistance. This step was deemed necessary, even with a new motor in the equation. And let’s not forget, this car originated from the workshop of Dodgy Dave himself, where overlooking anything is out of the question in the pursuit of coaxing this old N46 into a melodious tune – well, at least a whistle would suffice (Fig.3).
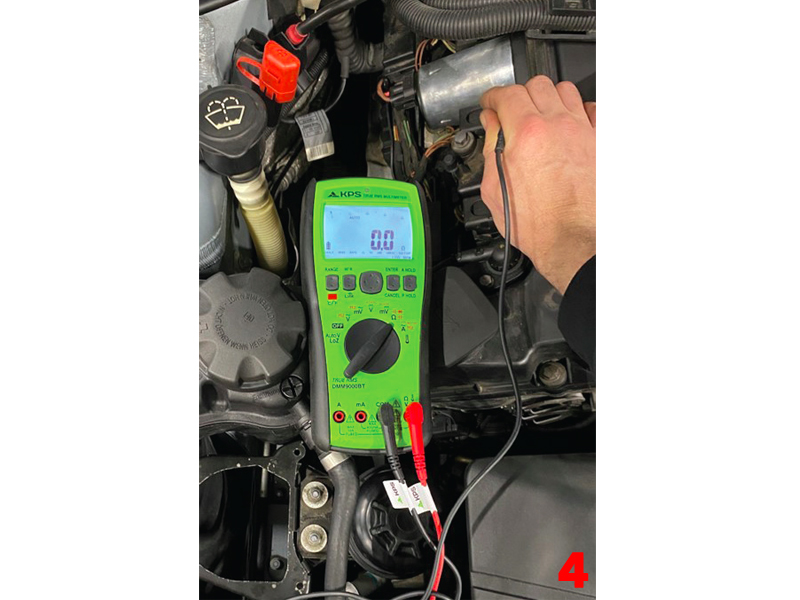
The motor resistance test sailed through with flying colours, and a thorough check of the motor’s external grounding also passed the test (Fig.4). With the anticipation building, I swiftly removed the cam cover, revealing a surprisingly clean set of internals. However, one anomaly jumped out at me the moment I laid a 17mm spanner on the end of the eccentric shaft.
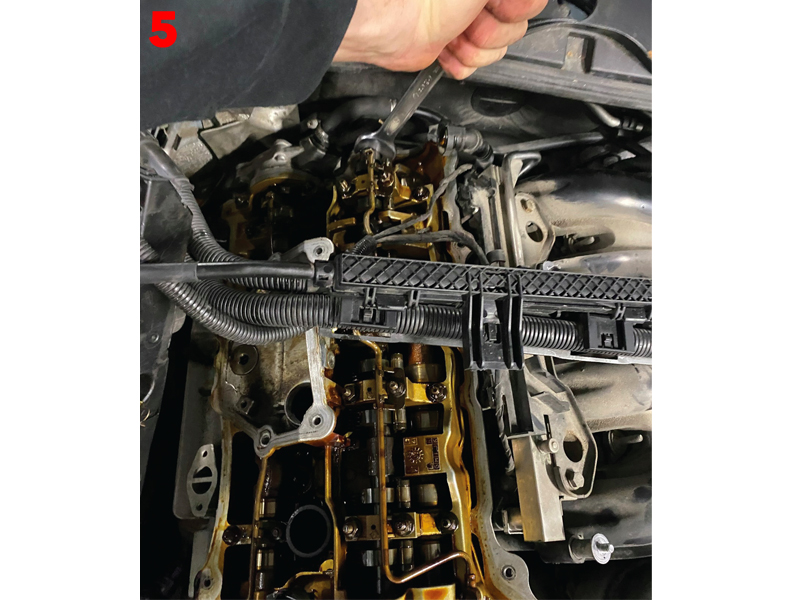
Now, the spring return action of the eccentric shaft isn’t exactly wrist-snapping strong compared to its counterparts in the BMW engine family, but it should exhibit some resistance. Alas, it seemed that the eccentric shaft was showing signs of being excessively stiff. Recalling that the valve cover had been removed at the previous garage, I had no choice but to loosen and inspect the eccentric shaft bearing cap nuts (Fig.5).
To my utter astonishment, the torque setting was massively overtightened. Comparing the recommended torque setting for these particular nuts meant that they really shouldn’t have been so tight, yet these stubborn nuts yielded with such a resounding crack that I nearly broke my wrist – a clear indication that someone, perhaps with a heavy hand, had overtightened these nuts – possibly the work of one of Dave’s henchmen.
With the bearing cap nuts now set to the correct torque, I embarked on a quick prayer and crossing of the fingers ritual before attempting to rotate the eccentric shaft once again. This time, the shaft exhibited a much smoother movement – a promising sign of success, or so I hoped.
The pivotal moment came when activating the valvetronic end stops learning via ISTA, and to my delight, success echoed through the mechanism. It moved with a newfound grace and following this triumphant movement, I was able to erase the fault codes completely. A sigh of relief swept over me as the N46 engine, once plagued by misadventure, found its rhythm once more which meant that at the very least, I would be able to get the car on a road test to evaluate the repairs.
My external demeanour may not have screamed happiness, but inside, I was ecstatic. Discovering and rectifying two faults within the span of an hour – who wouldn’t be happy? The silent triumph of rectifying automotive butchery and coaxing the N46 engine back into a harmonious state was, indeed, a cause for celebration.
Following the road test, the car stood as a testament to a successful repair. 116 horsepower chugged the car along at a reasonable pace, accompanied by a blissful absence of warning lights. The engine’s soundtrack echoed with about as much smoothness as the old N46 lump could muster and its performance was at least adequate considering when it arrived it wouldn’t pull the skin off a rice pudding. A triumphant post-repair experience, where the road test unveiled one of the better performing N46s that I have repaired.
In conclusion, the hazards of entrusting your car to an unskilled or subpar mechanic are evident in the tales spun by Dodgy Dave’s Garage. From overtightened bolts to mysterious faults, the aftermath of such encounters can be a costly and timeconsuming ordeal. A skilled and meticulous mechanic can make the difference between a smooth repair process and a cascade of complications. It’s a reminder that choosing a reliable and experienced professional can be a safeguard against the automotive misadventures that can unfold in the hands of a less-than-competent technician.