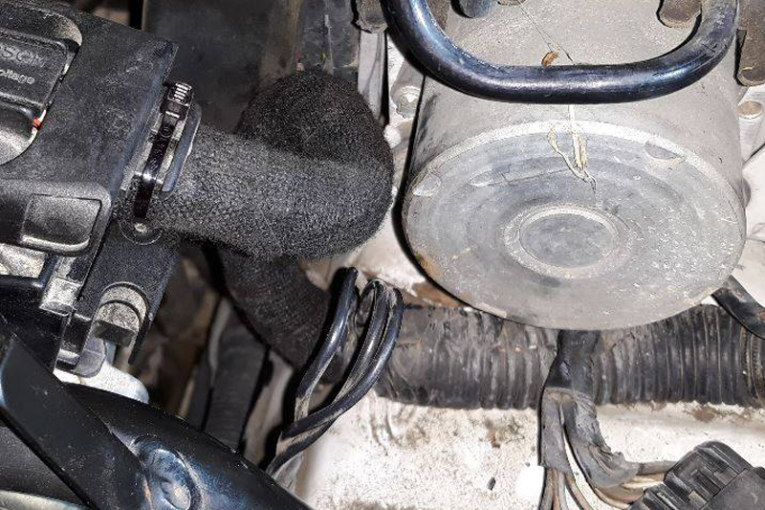
Technician Simon Littlejohn shares an interesting case study of where the parts cannon failed to fix the problem and further diagnostic work was required.
Do you need a scope to diagnose vehicles?
Having experienced many diagnostic problems over the past year, I wanted to share the biggest I was involved with when I was helping out a dealership.
The vehicle was a 2016 Fiat Ducato 2.3 Euro 6 diesel van with 80K miles on it. It had had the parts cannon shot at it (a typical case for ScannerDanner), and thanks to a Frank Massey, video I found the fault.
The vehicle had already had the following parts replaced: engine ECU, air flow meter, four injectors, intercooler, DPF, low and high-pressure EGR valves, EGR cooler, boost control valve and turbo; all new and genuine parts. In addition, the timing had been checked, the exhaust swapped and the air intake had been checked for leaks. All had no faults found and no improvement on the vehicle. This added up to over £10k in parts alone!
The vehicle had an ongoing concern; flagging an error for turbo under-boost and air flow meter drift. However, it only flagged this error around every 400 miles, so the fault was very difficult to reproduce. It would normally set at about 30% throttle and not full load as if it had a leak or a blockage.
The same error could be reproduced by disconnecting the vacuum to the turbo. The boost control worked, altering the vacuum to the turbo, and when tested with a voltmeter you could see the voltage change and the duty cycle. Unplugging the solenoid set an open circuit error. However, when road testing – even without the fault active – you could see the vacuum didn’t relate the percentage requested by the ECU intermittently.
According to the customer, the issue started after an EGR recall. This information sent us down the wrong track. I wanted to see if the high or low-pressure EGR was active when the fault set and had driven the vehicle for 300 miles with a data logger connected trying to capture more data when it finally happened. I had not been able to reproduce the fault during those first 300 miles, but I could see that the boost did not always follow the set point, just not far enough away to set the fault. This led me to think it was due to the turbo sticking. It was only after I watched Frank Massey’s video looking at the percentage commanded by the ECU and comparing to the difference in vacuum that I could see that it was low boost only in the mid-range commands.
I connected the PicoScope and captured this, almost 50 volts to operate a 12-volt control solenoid! The feed to the valve was ok from the fuse with only battery voltage, wiring to the ECU on the control wire was all ok and the ECU was new. When I checked the ECU supplies, I found one of the feeds missing, the wire had been rubbing on the ABS pump and had broken. Without a good power supply, the ECU could not control the valve correctly so at around 70% operation the vacuum to the turbo was too low so it would under-boost. The turbo does not have a position sensor on it so there is no feedback to the ECU that the turbo was in the incorrect position.
Every day is a school day as they say, and this is one I will remember.