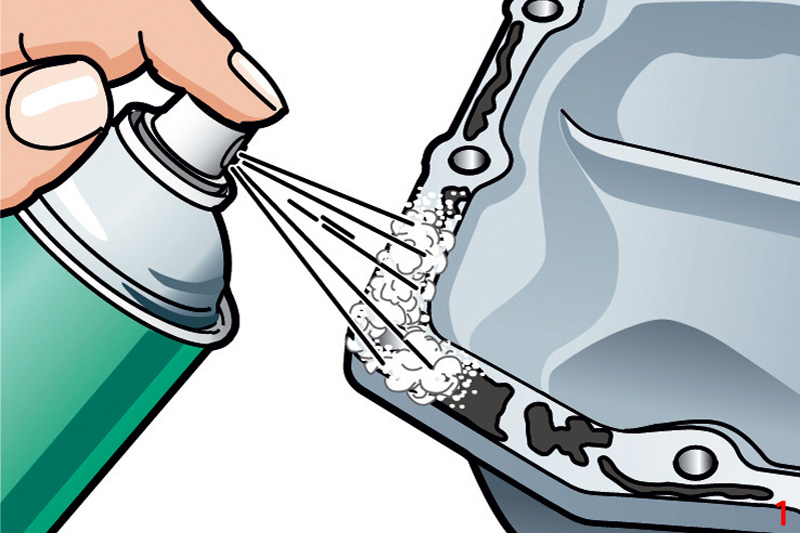
Henkel, the engineering adhesives manufacturer, presents its top tips to help improve your gasketing skills.
Gaskets are used to prevent leakage of fluids or gases by forming impervious barriers and nowhere more so than in the automotive industry. For successful gasketing, it is necessary for the seal to remain intact and leak-free over a long period of time. The gasket must be resistant to fluids and/or gases and withstand the operating temperatures and pressure to which it is subjected.
There are two different gasketing techniques:
- Compression gasketing
- Liquid gasketing
Gaskets can fail for any of the following reasons as they are subject to environmental factors such as temperature, different pressures, relative movements, etc:
- Gasket displacement
- Relaxation and creep
- Surface irregularities
- Flange bowing
- Flange deformation
Rigid flanges – anaerobic flange sealant
Rigid flange sealing typically relates to metal-to-metal assemblies where the sealing gap is zero or small (up to 0.25mm) and the product is often not visible. The LOCTITE anaerobic flange sealants are suitable for this type of gasketing. They provide self-forming seals that fill all voids – surface roughness and imperfections; provide total contact; cure to a durable seal with adhesion to both flange surfaces; eliminate flange face corrosion and of course, offer an instant seal.
Application
Firstly, remove old gasketing adhesive and ensure components are clean and free from contaminants such as grease and oil (Fig 1/main image).
- Apply the relevant LOCTITE gasketing adhesive as a continuous bead onto one flange surface. Place the bead close to the inner rim of the flange and encircle all holes (Fig 2)
- Adhesives can also be applied by roller onto large flanges
Available formulas
- LOCTITE 510 – high temperature and chemical resistance
- LOCTITE 518 – excellent oil resistance, ideal for use on iron, steel and aluminium flanges
- LOCTITE 5800 – excellent chemical and temperature resistance of cured products and superior oil and water/glycol resistance; hazard label free
Assembly
- Assemble flanges and tighten bolts as soon as possible
If the rate of cure is too slow due to passive metals or low temperature (below 5˚C), apply a LOCTITE activator to the flange surface before the gasketing adhesive.
How a LOCTITE anaerobic gasket cures
- LOCTITE anaerobic flange sealants remain liquid as long as they are in contact with oxygen
- They cure to a solid thermoset plastic in the absence of air whilst in contact with a metal surface
Disassembly
- Remove bolts with standard hand tools
- Use jacking-screws or cast-integral bosses and recesses to prise flanges apart (Fig 3)
Flexible flanges – silicone flange sealant
Flexible flanges are suited for large gap applications and assemblies (over 0.25mm), where movement can occur. Flanges can be made from different materials and the sealant product is usually visible once the seal has been formed. Finally, this type of flange can be used at T-joints where three different parts are joined at one point, for example timing cover to cylinder head and cam cover.
The LOCTITE silicone flange sealants are suitable for this type of gasketing. They are single-component products that fill voids – eliminating the need for a fine surface finish. No shimming is required so there’s no need for re-torquing; they provide an excellent seal and permit disassembly if required.
Application
Firstly, remove old gasketing adhesive and ensure components are clean and free from contaminants such as grease and oil. Next, apply as a continuous closed bead onto the chamfered flange surface around dowel and bolt holes (Fig 4)
Available formulas
- LOCTITE SI 5990 – high temperature resistance and hazard label free; typically used where operating temperatures are up to 350˚C and for electrical insulating applications
- LOCTITE SI 5660 – excellent resistance to water/glycol and hazard label free; ideal for applications involving large gaps; typical applications include transmissions and cast metal housings
- LOCTITE SI 5980 – excellent resistance to oil and hazard label free; ideal for applications involving large gaps; typical applications include timing gear covers and oil sumps where good oil resistance and the ability to withstand high joint movement are essential
Assembly
- Assemble and tighten flange assembly before silicone skins over
How a LOCTITE Silicone Gasket cures
LOCTITE silicones cure with atmospheric moisture releasing byproducts while forming a flexible elastomer (Fig 5)
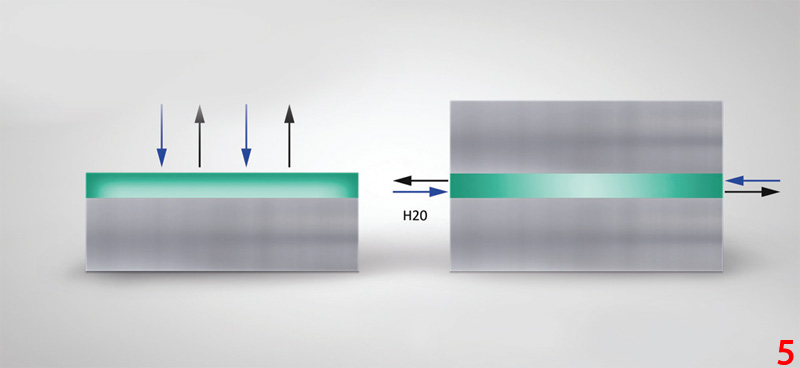
Disassembly
- Remove bolts with standard hand tools
- Use standard tools to cut the bead or jacking-screws to lift flanges apart