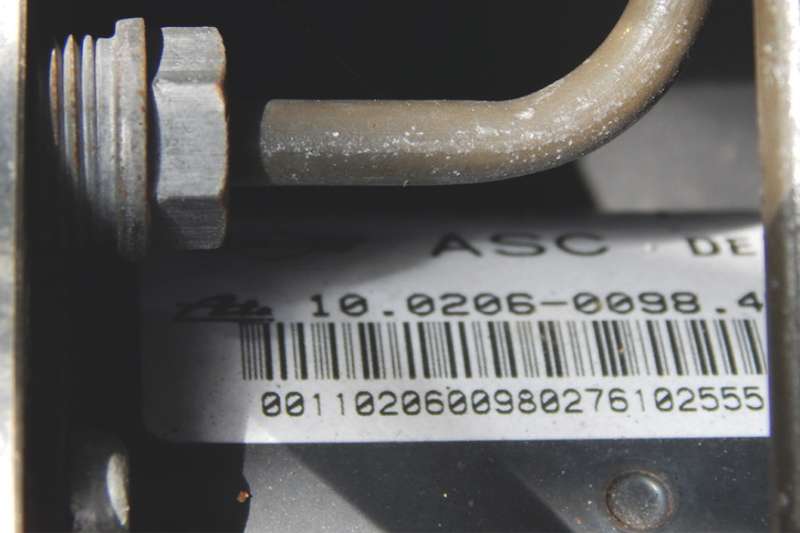
Febi takes a look at the intricacies of the braking system found on the BMW MINI.
Active vehicle safety systems have been developing at a rapid rate in recent years – systems such as Anti-lock Brakes, Traction Control, Stability Control, Adaptive Cruise Control, Automatic Emergency Brake to name but a few. These systems have been designed to help the driver avoid accidents and ultimately help save lives.
In this article, we will focus on the BMW MINI, which was a joint development between Rover and BMW from 1995, until BMW took full control of the project in 1999. When launched, many parts of the car were sourced from existing BMW models. This included the braking system. The new MINI was first introduced in 2000, and depending on the model or options selected, it was fitted with Anti-lock Braking (ABS), Automatic Stability Control (ASC) or Dynamic Stability Control (DSC), which eventually became a standard fitment in 2008.
The first generation of MINIs (R50/52/53) was equipped with a variation of the Teves Mk60 ABS unit as standard, which included the following three features:
EBV – Electronic Brake Force Distribution
(Elektronische Bremskraft Verteilung) – Control of the rear axle braking force is regulated by the ABS unit, which detects partial braking by the wheel speed sensor signals.
CBC – Corner Brake Control
Reduces vehicle instability that can arise when the brakes are applied while cornering at speed, by distributing brake pressure to the left and right brakes, or reducing the brake pressure to the rear axle.
MSR – Engine Drag Torque Control
(Motor Schleppmomenten Regelung) – Prevents the driven wheels from locking up under engine braking.
Some models of the MINI were also fitted with ASC and some with DSC:
ASC – Automatic Stability Control
A variation of traction control designed to maintain directional stability under acceleration and to improve traction. The system reduces engine torque via the ECU and applies brake pressure to the slipping wheel until traction is gained.
DSC – Dynamic Stability Control
Has additional features above ABS and ASC which include:
DBS – Dynamic Brake Support
Automatically supplements braking output when the brakes are applied under emergency braking conditions. This is monitored by vehicle speed and brake pressure.
MBS – Maximum Brake Support
Is mainly effective when the vehicle is fully laden and the ABS control is more active on the front axle. Then the rear axle is brought into the ABS control through increasing brake pressure.
DSC has additional sensors which include steering angle, yaw rate, transverse acceleration and hydraulic pressure to achieve the extra control.
But how can you tell which system is fitted to the vehicle you are working on? Simple! You can identify the system by looking along the row of switches below the heater control, and if the vehicle is fitted with ASC or DSC, it will have a switch to turn off these features from the ABS system. Alternatively, locate the ABS unit under the bonnet (close to the bulkhead) and there will be a sticker on the motor of the ABS unit (see below).
The braking system is an integrated part of the car’s electrical system and communicates information to other control units via the CAN bus network. Information such as wheel speed, brake pressure, steering angle, brake lamp switch, handbrake switch, ASC or DSC switch, Yaw rate and lateral acceleration values are all used in conjunction with the engine management, Supplemental Restraint System (SRS), Body Control Module and automatic gearbox ECU (if fitted), to implement the necessary braking to assist the driver (see below).
Febi has looked at some of the common sensors and repair procedures on this system to provide an insight into maintenance and repair. Wheel Speed Sensors on the MINI are a magnetoresistive type and fitted into the hub assembly (see below left hand, front hub pictured).
All four wheel speed sensors relay the rate acceleration, deceleration and the direction travel to the ABS control unit. The speed signals are registered by the corresponding sensors 34262 (front) and 34263 (rear) and processed by the ABS control unit.
NOTE: The rear left sensor is also used as the driving speed signal for the speedo, and the rear right sensor is used as an input signal for other control units, such as the automatic transmission if fitted.
The sensor is mounted in the hub at right angles to the magnetised impulse wheel that is built into the wheel bearing seal. The active wheel speed sensor makes use of the magnetoresistive effect; a magnet in the sensor produces a magnetic field with the lines of magnetic flux running at right angles to the sensor layer. Deflection of the lines by the impulse wheel causes changes in resistance in the thin ferromagnetic layer of the sensor element (see below).
The sensor element converts the changes in resistance into voltages. The square wave voltage detected by the ABS control unit is a measurement of individual wheel speed and this is used to derive the vehicle speed and is definitive for brake control.
A Steering Wheel Angle Sensor is only fitted to vehicles that are equipped with DSC. The sensor (36081) is located at the base of the upper steering column and is designed as a potentiometer with two wipers offset by 90° (see below). The potentiometer signal is evaluated and converted into digital form to be on the CAN network.
The sensor signals provide a steering wheel angle variable, which covers the entire range of steering wheel rotation. The signal is repeated after every 360 ̊. Voltage jumps are then evaluated, thus determining the steering wheel turns. The total angle is therefore derived from the sensor signal, the stored steering wheel angle offset, and the number of steering wheel turns.
The steering wheel angle sensor is calibrated to the individual vehicle, meaning if you replace one it must be calibrated to the ABS/DSC system using suitable diagnostic equipment. The calibration permanently stores steering wheel position at the straight- ahead position. Therefore it is very important when carrying out this procedure that the front wheels are set exactly in the straight- ahead position.
The DSC Sensor combines the functions of the Yaw rate sensor and transverse acceleration sensors and is located to the rear of the handbrake lever beneath the trim. This sensor feeds back information to the ABS/DSC control unit on the angular rotation of the vehicle around its own vertical axis (Yaw) and lateral acceleration to determine vehicle drift. If the control unit is replaced, it will need to be calibrated using suitable diagnostic equipment.
With all its safety features built into the braking system, if the vehicle reaches its dynamic driving limits, the control unit decides whether to implement ABS control, ASC or full DSC control subject to the situation.
Maintenance:
It is recommended that brake fluid is replaced regularly to the manufacturer’s service intervals due to its hydroscopic nature. If this is not carried out regularly, the boiling point of the fluid is lowered (due to increased water content) and there is an increased risk of internal corrosion to the metal brake components.
When replacing the brake fluid on a MINI, it is recommended that a pressure bleeder is used. However, this should be set no higher than 2 bar. You should also use a suitable diagnostic tool to go through the process of running the ABS pump, in order to fully bleed the brake system. With the vehicle raised and starting with the right rear, open the bleed valve with the tube and collecting bottle attached. Run through the bleeding process until the fluid is clear and free from air bubbles before closing and tightening the bleed valve. Repeat the process for the rear left, front right and front left. After replacing the brake fluid, check for leaks and reset the brake fluid service reminder on the dashboard if illuminated.