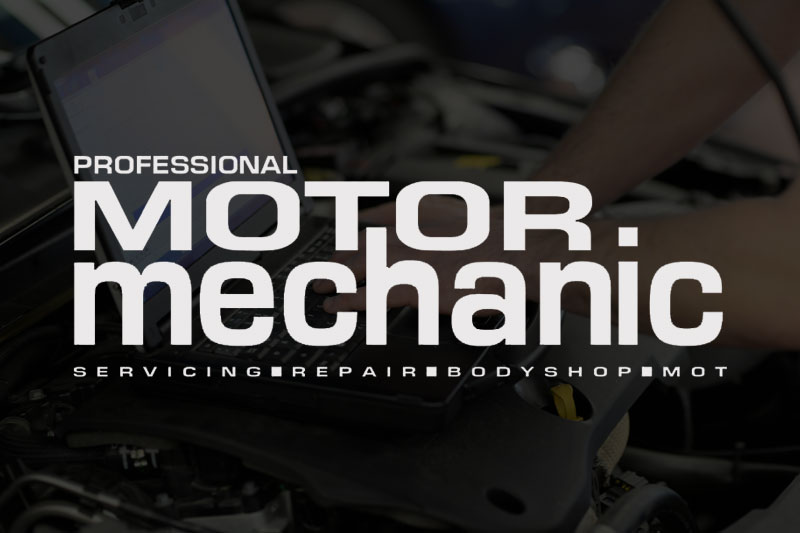
Due to the need for a reduction in response time delays and the ever increased accuracy of the control systems of the modern internal combustion engine, some new and very specific sensor technologies are being utilised by VMs. One critical area that is always under intense scrutiny is, of course, exhaust gas emissions.
Direct Petrol Injection
To make petrol engines more economical and environmentally friendly, VMs are increasingly relying on Direct Petrol Injection engines that can run at considerably leaner air/fuel mixtures under certain conditions – primarily partial load (cruise) conditions.
The result of this can be an improvement of 12-20% in fuel consumption, but, as with most things in life, there is a penalty to pay for this benefit.
One of the resultant gaseous compounds produced as a result of the combustion process within a spark ignition engine is known collectively as NOx. For the automotive industry, this term is used to describe the nitric oxide and nitrogen dioxide contained within the exhaust gas.
NOx compounds are environmentally damaging by-products of the combustion process, and most vehicles deal effectively with this by the use of a three-way catalytic converter. Spark ignition engines tend to produce greater quantities of these compounds when running at very lean fuelling conditions and the DI engine operates in this region when in ‘stratified’ mode.
The three-way catalyst can’t cope with this, due to the excess oxygen contained within the exhaust gas, which reforms the NOx; therefore, additional treatment of the exhaust gases is required.
Control strategy
One counter-measure strategy is to use a NOx storage catalyst – an additional piece of hardware fitted onto the exhaust system, which temporarily stores and, at a predetermined point, chemically reduces the compounds to harmless nitrogen and oxygen. This function of “regeneration” is triggered by a change in the fuelling calibration, causing a temporary fuel rich state within the storage device.
A vital part of the control strategy for this system is the NOx sensor, which is used to detect when the limit of storage capacity (saturation point) has been reached and will then instruct the fuelling management system to start the regeneration phase.
The frequency of this cycle can be around once every 60 seconds, then the rich regeneration period commences for around two seconds, before reverting to lean mode. The NOx sensor is an evolution of the wide band oxygen sensor and its element is constructed from special ceramics that contain two oxygen density detecting chambers that work together, allowing the determination of NOx concentration.
Their function is quite complex and these sensors require dedicated ECUs, which are either integrated into the vehicle’s control modules or are contained within a unit that is permanently attached to the sensor harness. It is common knowledge that most spark ignition vehicles must be fitted with a catalyst monitoring diagnostic sensor; however, this doesn’t have to be the case where a NOx sensor is used.