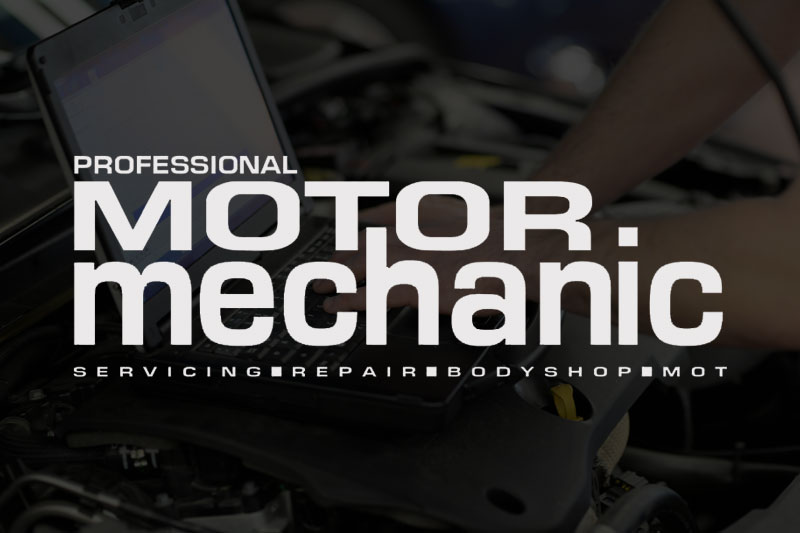
Wayne McCluskey, Technical Training Manager at ZF Services UK, explains the advantages of EPS and the technology underlying the systems available from ZF Lenksysteme.
Once limited to smaller car applications, EPS systems have recently become viable for larger vehicles with the advent of more sophisticated electric motor technology. In fact EPS can be expected to completely replace hydraulically-assisted steering on almost all new cars and light commercial vehicles within the next decade.
Eradicating the power steering pump, reservoir, pipework and oil of a hydraulic system has several clear benefits. It cuts weight, and as an on-demand system in which the motor only runs when needed, it does away with the parasitic drain of a constantly running hydraulic pump, consuming approximately 90% less energy. Both of these advantages benefit fuel economy, helping vehicle manufacturers to comply with increasingly strict emissions regulations.
Furthermore, EPS systems are maintenance-free, reducing the cost of ownership and fleet management. Passenger safety and vehicle handling can be optimised, since the self-contained system requires only electrical connections, giving more versatile mounting options.
EPS systems from ZF LenksystemeThe ZF Servolectric EPS range comprises three basic types, which between them cater for all classes of vehicle – from sub-compact city cars to prestige cars and vans. Each is a modern interpretation of the proven rack and pinion concept, featuring a high stiffness, light-weight design. The type selected for a vehicle depends on the space available for installation, the vehicle’s power supply and the steering force required. This dictates whether the servo unit that provides steering assistance is mounted on the steering column, on a second pinion meshed with the steering rack, or in parallel with the rack. Modular servo units ensure that adaptation of the EPS system to a particular model of vehicle or to suit specific performance requirements is easily achieved.
How EPS works
As the driver turns the steering wheel, sensors precisely register the corresponding steering torque and steering speed, passing them to the EPS electronic control unit (ECU). These measurements and other dynamic vehicle data are compared with stored values to calculate the required steering assistance to be provided by the servomotor. The motor then transmits the optimum servo torque via a worm gear or recirculating ball gear to the steering column, second pinion or steering rack, according to the type of system used.
If the power supply to the motor or ECU is interrupted by a fault in the vehicle’s electrical system, the driver can safely continue to steer the vehicle via the mechanical connection between the steering wheel and the steered wheels.
The electronic control unit (ECU)
The ECU is the heart of a ZF Servolectric EPS system. It registers a wide range of parameters – including road speed, steering angle, steering torque and steering speed – and processes these to calculate the assistance required and the corresponding current to be passed to the electric motor. A micro-hybrid unit in a hermetically sealed package, it houses a 32-bit microcontroller with on-chip flash memory and RAM, and the output stage for the motor. All relevant information, including stored vehicle data and current operating parameters such as vehicle speed, steering speed and engine status, remain permanently ‘in view’ to ensure optimum response.
The ECU can be networked with vehicle management systems via the CAN bus, enabling the EPS system to be integrated more effectively in stability control systems such as ABS or ESP, and also enabling functional checking via diagnostics. Steering damping characteristics are also electronically programmable to provide absorption of outside forces such as road bumps.
Motor technologyThe motor’s role is to convert the current defined by the ECU into the torque that is transmitted to the steering drive gear. A new generation of electronically commutated brushless electric motors constructed from novel materials is a vital feature of ZF EPS systems. Extremely compact yet highly efficient, their high precision, low noise generation and minimal torque ripple have been key factors enabling the development of electronically controlled steering systems for larger vehicles.
WHAT T YPES ARE AVAILABLE?
SERVOLECTRIC EPSC
TYPE: Column type
SUITABLE FOR: Small cars (steering axle loads up to 1,000kg)
Even drivers of the smallest compact cars now expect their vehicles to come equipped with power assisted steering, to make low speed manoeuvring in heavy traffic and during parking as effortless as possible. For these vehicles, ZF Lenksysteme GmbH developed the EPSc system, in which the servo unit and its electronic controls are integrated in the steering column. This is an exceptionally lightweight design that requires a minimum of installation space.
SERVOLECTRIC EPSDP
TYPE: Second Pinion type
SUITABLE FOR: Mid-size cars (steering axle loads up to 1,200kg)
In this type, the servo unit is installed on a drive pinion separate from the steering column pinion. It can be rotated by 360° around the axes of the rack and the drive pinion, enabling versatile configuration to suit multiple applications. The second pinion ratio is independent from that of the steering ratio, allowing system performance to be optimised, typically by 10-15%.
SERVOLECTRIC EPSAPA
TYPE: Parallel Axis Servo Unit type
SUITABLE FOR: Larger vehicles (steering axle loads up to 1,600kg)
For larger vehicles such as luxury cars, sports cars, off-road vehicles and vans, a different approach is necessary to achieve the low friction and high efficiency needed to satisfy the high load demands of the steering system. The drive motor is mounted parallel to the steering rack, and drives a recirculating ball gearbox on the rack via a toothed belt. Once again there are many positioning options for the servo unit to match the installation space available and ensure that crash performance requirements are met. The recirculating ball gear generates very low noise, which allows rigid connection of the steering gear to the vehicle subframe to give a more direct feel to the steering.