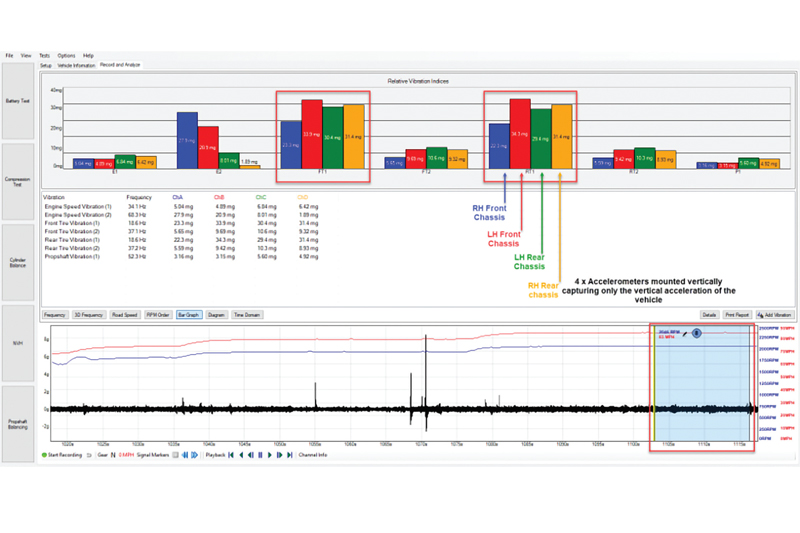
Pico technician Steve Smith examines a BMW 320D M Sport xDrive Touring after the owner complained of significant cabin vibrations when travelling at motorway speeds.
As a technician, there are a number of customer complaints that you know are going to be a real challenge, one of which is cabin vibration. Complaints of cabin vibration are subjective and depend on a number of human factors, such as tolerance levels, expectation and misinterpretation.
Tackling complaints of Noise-Vibration-Harshness (NVH) is no different from how we approach any diagnostic challenge. We use a process that will deliver results, which we can apply to make an informed decision on how to proceed to be able to form a conclusion. Note, however, that the conclusion may not be a fix but that it can still be satisfactory to all parties involved!
If I could give one tip to anyone faced with such a challenge, keep notes and capture/save objective data.
The following case study is one such example.
Customer’s description
The customer reports that vibration can be felt through the vehicle at approximately 75mph. The symptom has been present for over two-and-a-half years, and they have made numerous attempts to resolve the issue.
Technical description
Verifying the customer complaint is an essential step in the diagnostic process and with complaints of vibration, it is absolutely paramount. Given that vibrations are subjective (a matter of opinion), a tip here is to road test the vehicle with the customer and ask them to indicate when they experience their concern. Typically, at this stage of the diagnosis, you should be gathering vital pieces of information without applying any test equipment. However, I would like to break from tradition at this point in the process.
If you are lucky enough to have the chance to do a road test with the customer, I advise you have the NVH kit connected to the vehicle during this verification process. You can find information on how to connect and collect data in this case study in our NVH video series.
When our customer indicated that they could feel the vibration, we were prepared to capture an objective measurement that we could save for review, and more importantly, to obtain evidence. This may sound a little odd but one man’s vibration is another man’s harshness (once again, a matter of opinion).
Our initial NVH capture (with the customer present) (Fig 1) highlighted a firstorder front and rear tyre speed/frequency vibration (FT1 and RT1). The vertical axis was the largest offender (red bars within the bar graph). We had also captured a secondorder engine vibration (E2), which we could discount while the vehicle develops the power to maintain the road speed.
On this occasion, I agreed with the customer. An objectionable vibration was clearly evident through the floor pan and driver’s seat cushion, but I could not sense anything via the steering other than brake judder when applying the brake (a point worth adding to your notes).
Diagnosis
With the customer complaint verified, we confirmed the vehicle’s ID and specification. Confirmation of vehicle specification is of utmost importance when it comes to vibration complaints!
There is often an understandable temptation for customers to modify their vehicle with fashionable accessories that may add a ‘nice cosmetic touch’ but lack the fundamental quality control and engineering that was intended for the vehicle at the point of design.
I am referring here to wheels and tyres. You could argue that nothing changes the look of a vehicle more than wheels and tyres (and I would agree), but I would also argue that nothing transforms a vehicle’s handling, performance, drivability and noise/vibration levels than inferior wheels and tyres.
The customer interview highlighted that a number of wheel balance procedures, wheel alignments, tyre replacements (including wheel straightening) had all been actioned over the complaint period which spanned more than two years. I think it’s worth mentioning here once again, how vital the customer interview has become to the diagnostic process. Quite often customers don’t have time to be questioned, they simply want answers, and this is why we need to drill down with targeted, open questions such as:
1. How long has the problem been evident?
This is a great question for customers who are new to their vehicle as they are in a transitional period from a vehicle they knew to a new vehicle. If the customer has been using the vehicle for less than two months, I would ask about their previous vehicle. If they have moved from an SUV to a sports convertible their complaint about vibration/harshness, while justified, is a vehicle characteristic.
Note! We cannot repair or improve upon characteristic vehicle behaviour. If we try, we are openly admitting to our customer that there is a fault and it’s a long road back home if we choose this path.
2. When did you first notice the problem?
I like this question as it places a time stamp on when the vibration became objectionable. It also leads on from question one (above) if the reply is “ever since I purchased the car”. It may also lead you to historical vehicle events if the customer replies “ever since the accident repair” or “since my last service”. We fondly refer to these answers as ‘the ever since syndrome’.
3. Has any work been carried out on the vehicle recently?
This question has the potential to guide you to areas of the vehicle that you may not have considered if the customer is prepared to surrender this information. But be careful here, a customer may not consider a puncture repair as work carried out; mistakenly believing a puncture repair is a simple process not worthy of a mention. I cannot think of a single repair that could be more of a game changer when it comes to vibration than a puncture repair!
4. When do you experience the problem?
Here is your opportunity to ask additional, specific questions during the customer’s reply. For example: “The problem only occurs on the motorway”, where we can add “at what speed?” They may answer 60mph, which leads to our follow up question: “Can you still feel the problem at 70mph?”, etc. This feels more like an engaging conversation than a question and answer session. If we look back, we have asked six questions in total and gained a huge amount of key information. Moving on, the basic inspection confirmed no visible signs of damage to suspension components, alloy wheels or tyres. On the subject of tyres, in a perfect world, all the installed tyres should be the same brand/speciation with near identical construction date (stamped on the tyre wall), ‘approved’ for the vehicle and on recommended rims. In reality, this is near impossible, however, it should not be overlooked. Working with multiple vehicle manufacturers has opened my eyes to the importance of ‘approved tyres’. In this case study, the tyres were Star-rated, which ensures they are BMW approved for performance, deformation and Radial Force Variation (RFV).
RFV is often either overlooked or not even considered when diagnosing cabin vibration. However, it has proven to be the main cause of tyre speed related vibration orders (T1, T2 and T3). Luckily, the Hunter Road Force Balancer has the ability to measure rim and tyre run-out (under load), presenting the operator with the optimal tyre-to-rim phase match, as well as the preferred wheel/tyre orientation on the vehicle.
The video describes how this is achieved and I hope it can help cure nuisance vibrations that conventional wheel balancing techniques fail to resolve.
Prior to diving in, it is paramount to take a step back and check for technical bulletins (recalls, campaigns, etc.). After doing this, it appeared that none were relevant, and so based on the vehicle history and symptoms we could move on to possible causes.
Possible causes
- Wheel/tyre imbalance
- Excessive tyre RFV
- Deformed wheel/rim
- Incorrectly mounted tyre
- Brake disc/hub imbalance
- Wheel centre to hub alignment
- Drive shaft deformation, run-out or imbalance
- Excessive wear in suspension components, resulting in the transmission of inherent vibration
The action plan
The action plan was predominately governed by accessibility, probability and cost.
1. Zoning of vehicle to narrow down offending vibration
2. Confirmation of wheel balance
3. Wheel and tyre run-out measurements
4. RFV measurement
To recap:
- There is a cabin vibration at motorway speeds
- The NVH software has captured a first-order tyre speed related vibration (vertical axis)
- The peak vibration occurs at 83mph
- The replacement tyres that have been installed are approved for the vehicle (Star-rated)
- Numerous wheel balance procedures have been carried out on the vehicle to deal with the problem
One question that is often raised when we have identified a vibration is: How do we find out which corner of the vehicle is responsible for the vibration? In other words, how can we zone in on the vibration?
For those lucky enough to own an NVH advanced kit (with a 4-channel PicoScope), we have the distinct advantage of placing an accelerometer at each corner of the vehicle to measure our offending vibration (first order tyre vibration in the vertical [Y] axis). The capture (Fig 2) highlights the vertical vibration levels captured by each accelerometer placed on this vehicle.
Note how the red bar graph indicates the highest level of vibration which corresponds to the LH front chassis in close proximity to the road wheel. However, I think we can agree that all FT1 and RT1 bars indicate a high level of vibration in close proximity to all road wheels. The keen-eyed amongst us may also have recognised that, while the NVH software has separated the front and rear tyre vibration levels of this BMW, the values are almost identical in terms of amplitude and frequency (18.6 Hz).
This is because the overall diameters of the wheel and tyre assemblies are near identical even though the tyre sizes differ. With near-identical diameters, the front and rear road wheels will rotate at near-identical frequencies.
Our NVH software, however, will still list front and rear tyre frequencies separately even with such minuscule differences (Fig 3).
- Front tyre 225/40R19 = 66.26cm
- Rear tyre 255/35R19 = 66.11cm
- Diameter difference = 66.26 – 66.11 = 0.15cm
At this stage of the diagnosis, the application of the four accelerometers failed to yield a conclusion as to the offending zone of the vehicle. Or did it?
What could cause such high levels of firstorder tyre speed related vibrations at all four corners of the vehicle? What about four imbalanced wheels or deformed alloy wheels?
Given that the road wheels had been balanced numerous times (and we had no access to an RFV balancer), the alloy wheel run-out was the next step in the diagnosis.